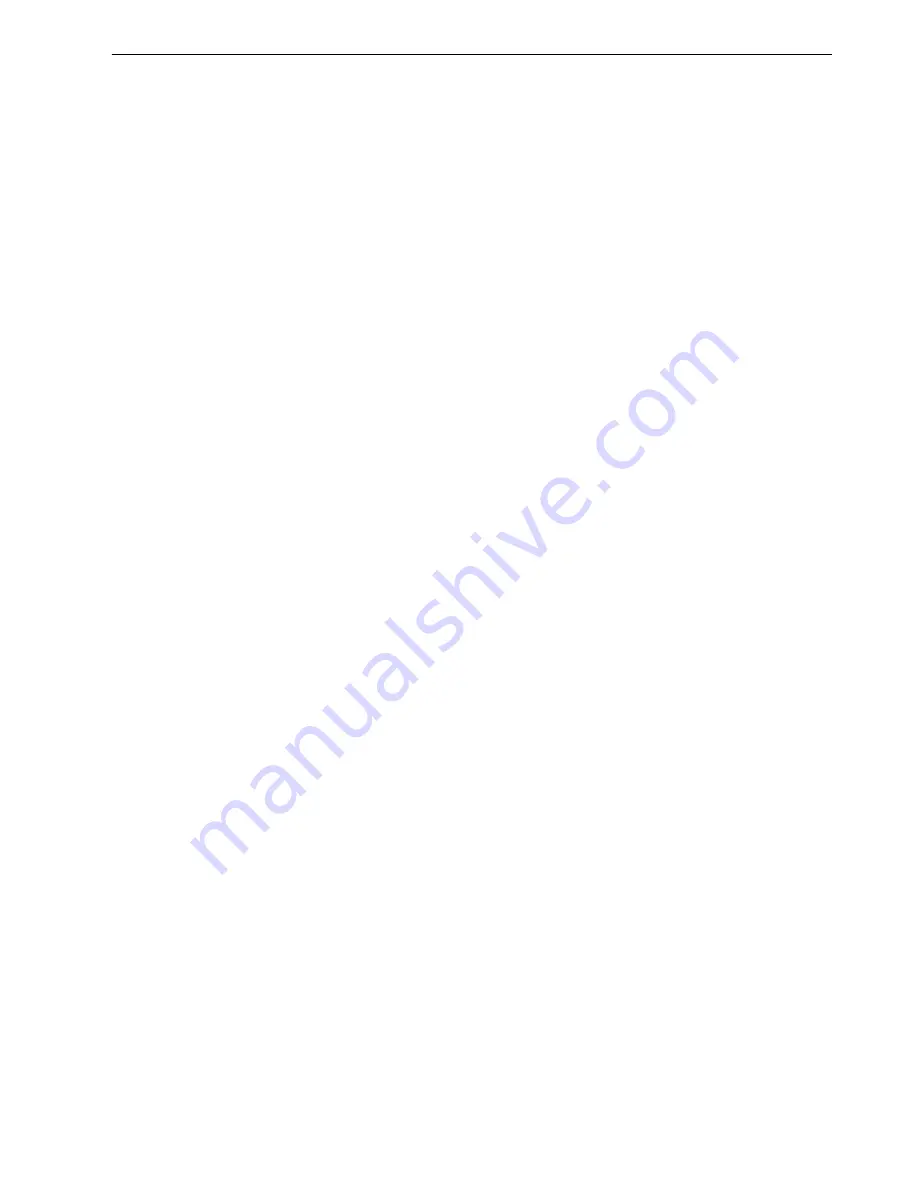
Refrigeration Service Procedures
121
Final System Charge
1. Install a gauge manifold set on the suction
service valve and the discharge port of the
scroll compressor.
2. Start the unit and use the Service Test mode to
run the unit in COOL. Maintain a -17.8 C (0
F) box and 37 C (99 F) ambient. Suction
pressure should be 83-174 kPa (12-20 psig)
and discharge pressure to 2000-2137 kPa
(290-310 psig) (suction service valve
cracked). Cover the condenser coil if needed.
3. Observe the suction pressure and slowly open
gauge manifold hand valve to allow liquid
refrigerant to flow into suction service valve.
Control liquid flow so suction pressure
increases approximately 138 kPa (20 psig).
4. Add refrigerant until sight glass is 3/4 full -
i.e. sight glass level ball should be at this
marker.
5. Stop the flow of refrigerant into the system by
closing the low-side gauge manifold hand
valve.
6. Continue to operate unit in COOL for 10
minutes to ensure ball is at correct level in
receiver tank sight glass. The total charge in
the system will be about 4.0-4.5 kg (8.8-9.9
lb) of refrigerant.
Refrigerant Gauge Removal
NOTE: Low loss fittings must be used on hoses
when Schrader port fittings are encountered on
units.
1. With a low loss fitting on the discharge gauge
line, remove this line from the discharge
service port.
2. Backseat the suction service valve, and then
crack it open one turn.
3. Start the unit and use the Service Test mode to
run the unit in low speed cool. See the
appropriate Microprocessor Diagnostic
Manual for information about the Service Test
mode.
4. Open both service manifold hand valves.
5. Front seat the receiver tank outlet valve.
6. Run the unit until a 3 to 5 psig (21 to 35 kPa)
reading is obtained on the suction gauge, then
back seat the suction service valve.
7. Stop the unit.
8. Back seat the receiver tank outlet valve.
9. Remove all remaining hoses.
10. Install and tighten service port and valve stem
caps.
11. Unit is ready for a functional check out.
Refrigerant Leaks
Use a reliable leak detector (e.g., electronic
detector) to leak test the refrigeration system.
Inspect for signs of oil leakage which is the first
sign of a leak in the refrigeration system.
NOTE: It is normal for compressor shaft seals to
have a slightly oily film.
Refrigerant Charge
Testing the Refrigerant Charge with
an Empty Box (Controlled Check)
If the unit has an insufficient charge of refrigerant,
the evaporator will be “starved” and the box
temperature will rise even though the unit is
operating. The suction pressure will drop as the
refrigerant charge decreases. The charge may be
determined by inspection of the refrigerant
through the receiver tank sight glass with the
following conditions established:
1. Close the truck box doors.
2. Install a gauge manifold. On units equipped
with an ETV and a Premium HMI Control
Panel the pressures may be viewed on the
screen.
3. Run the unit on high speed cool until the air in
the box indicates 0 F (-18 C).
4. The discharge or head pressure gauge should
read 290 to 310 psig (1999 to 2137 kPa).
If the pressure is below this, it can be raised by
covering a portion of the condenser coil with a
piece of cardboard.
Summary of Contents for UT-1200
Page 10: ...Table of Contents 10...
Page 20: ...Safety Precautions 20...
Page 76: ...Operating Instructions for Premium HMI Control Panel 76...
Page 88: ...Electrical Maintenance 88...
Page 98: ...Engine Maintenance 98 Figure 167 Fuel Components...
Page 142: ...Refrigeration Service Procedures 142...
Page 148: ...Clutch Maintenance 148...
Page 150: ...Structural Maintenance 150...
Page 162: ...Wiring and Schematic Diagrams Index 162...
Page 163: ...163 Schematic Diagram Page 1 of 2...
Page 164: ...164 Schematic Diagram Page 2 of 2...
Page 165: ...165 Wiring Diagram Page 1 of 5...
Page 166: ...166 Wiring Diagram Page 2 of 5...
Page 167: ...167 Wiring Diagram Page 3 of 5...
Page 168: ...168 Wiring Diagram Page 4 of 5...
Page 169: ...169 Wiring Diagram Page 5 of 5...