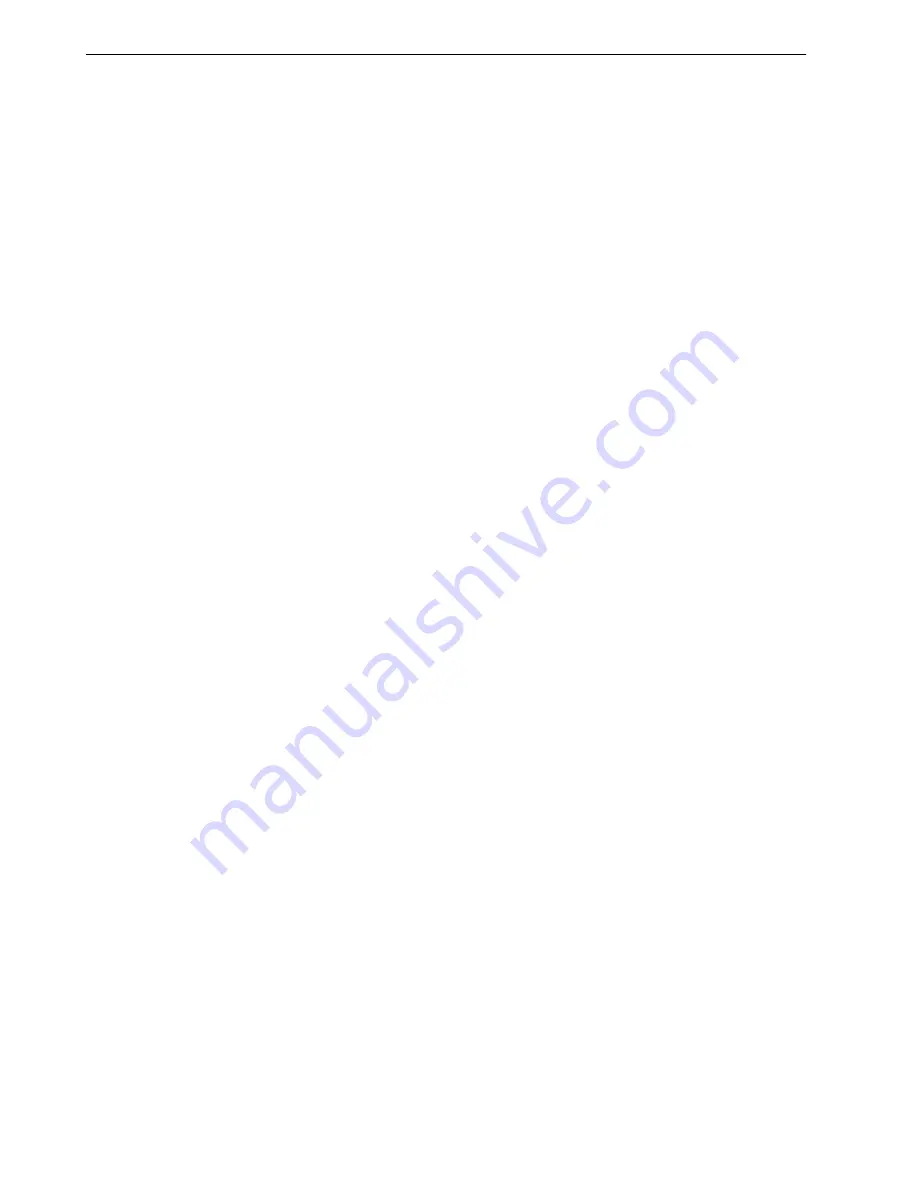
Refrigeration Service Procedures
134
3. Check the discharge pressure on the gauge
attached to the discharge service port. It
should be within the range shown for the DPR
setting in the “Specifications” chapter. If the
setting is incorrect, remove the protective cap
and try to adjust the DPR to the correct setting
before assuming it is faulty.
4. Remove the gauges to return the unit to
normal operation.
Discharge Pressure Regulator
(DPR) Replacement
Removal
1. Recover the refrigerant charge.
2. Remove the mounting clamp from the DPR.
3. Unsolder and remove the DPR. Note the
position of the DPR so the new one will be
placed in the same position.
Installation
1. Clean the tubes for soldering.
2. Place the new DPR in the same position from
which the old one was removed.
3. Use a heat sink or wrap the DPR with a wet
rag to prevent damage and solder the tubing
connections.
4. Install the mounting clamp on the DPR.
5. Pressurize the system and test for refrigerant
leaks.
6. If no leaks are found, replace the liquid line
drier then evacuate the system.
7. Recharge the unit with the proper refrigerant
and check the compressor oil.
8. Run the unit and test the DPR. Adjust the
setting if necessary.
Discharge Pressure Transducer
Testing
The discharge pressure transducer is used on units
equipped with an ETV. It is not used on units
equipped with a suction pressure regulator. The
discharge pressure transducer is located on the
discharge line near the discharge service port.
The discharge pressure transducer supplies
pressure information to the SR-3 Microprocessor
Control System. Alarm Code 86 (Check
Discharge Pressure Sensor) indicates a possible
problem with the discharge pressure transducer.
The pressure reading can be monitored with a
Mechanics/Premium HMI Control Panel by
pressing the
G
AUGES
key. Check the reading by
comparing it to the reading on a gauge attached to
the discharge service port. Refer to the
appropriate Microprocessor Diagnostic Manual
for more information about the testing and
operation of the discharge pressure transducer.
Discharge Pressure Transducer
Replacement
Removal
1. Recover the refrigerant charge.
2. Disconnect the wires and remove the
discharge pressure transducer from the
discharge tube.
Installation
1. Apply a refrigerant Loctite to the threads of
the discharge pressure transducer.
2. Install and tighten the discharge pressure
transducer and reconnect the wires.
3. Pressurize the system and test for leaks.
4. If no leaks are found, evacuate the
system.
5. Recharge the unit with refrigerant and check
the compressor oil.
Discharge Strainer Test
If the discharge strainer is plugged or restricted,
the unit will stop very quickly after is starts to run
and will record Alarm Code 10 (High Discharge
Pressure). This can also be caused by a faulty
HPCO. It can be difficult to determine whether
the discharge strainer of the HPCO is causing this
problem. See the following procedure and
guidelines.
1. Connect a high pressure gauge to the
discharge service port to monitor the
discharge pressure.
Summary of Contents for UT-1200
Page 10: ...Table of Contents 10...
Page 20: ...Safety Precautions 20...
Page 76: ...Operating Instructions for Premium HMI Control Panel 76...
Page 88: ...Electrical Maintenance 88...
Page 98: ...Engine Maintenance 98 Figure 167 Fuel Components...
Page 142: ...Refrigeration Service Procedures 142...
Page 148: ...Clutch Maintenance 148...
Page 150: ...Structural Maintenance 150...
Page 162: ...Wiring and Schematic Diagrams Index 162...
Page 163: ...163 Schematic Diagram Page 1 of 2...
Page 164: ...164 Schematic Diagram Page 2 of 2...
Page 165: ...165 Wiring Diagram Page 1 of 5...
Page 166: ...166 Wiring Diagram Page 2 of 5...
Page 167: ...167 Wiring Diagram Page 3 of 5...
Page 168: ...168 Wiring Diagram Page 4 of 5...
Page 169: ...169 Wiring Diagram Page 5 of 5...