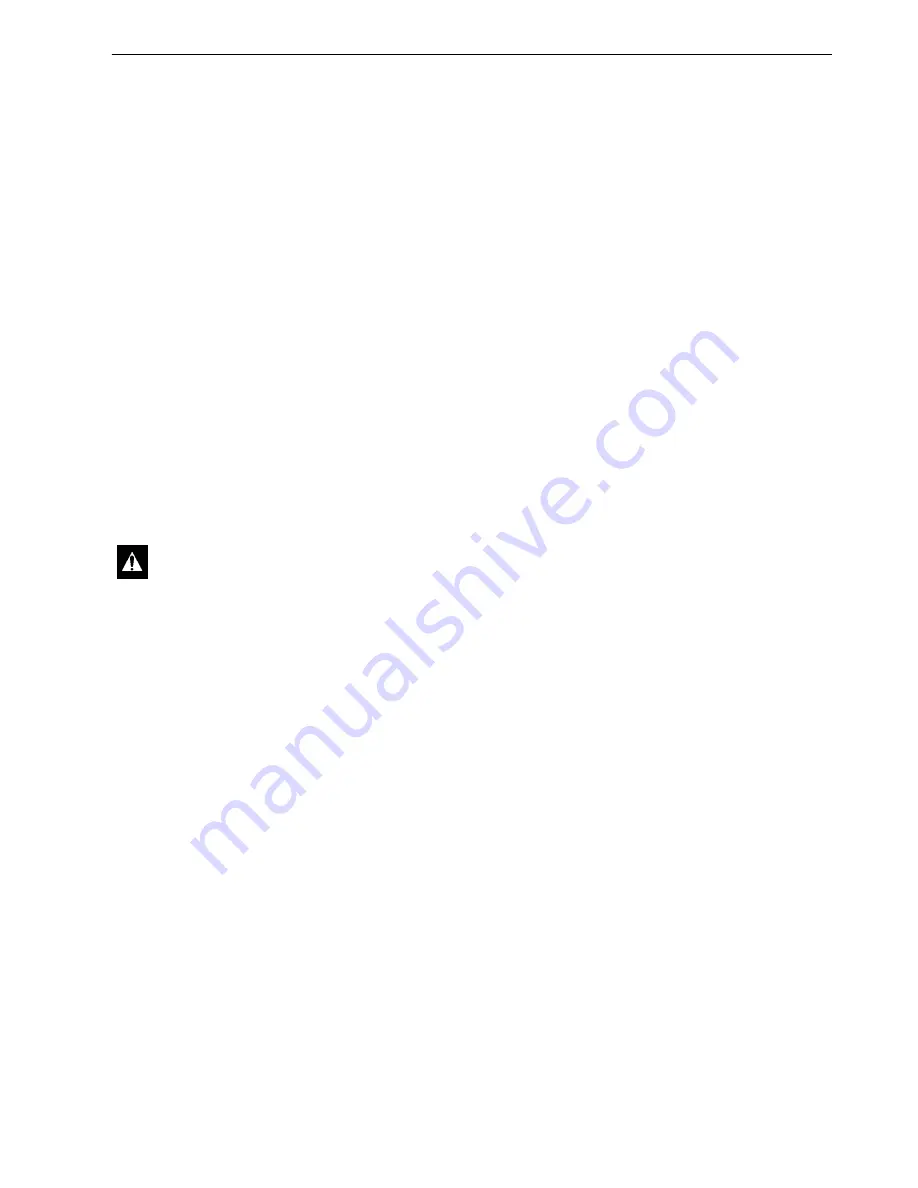
Refrigeration Service Procedures
139
4. Solder the inlet and outlet connections.
5. Pressurize the refrigeration system and test for
leaks.
6. If no leaks are found, replace the liquid line
drier then evacuate the system.
7. Recharge the unit with proper refrigerant and
check the compressor oil.
Liquid Injection Solenoid (LIS)
Test
1. Attach a gauge manifold to the suction service
valve and the discharge service port. A low
loss fitting must be used on the hose
connected to the discharge service port.
2. Run the unit in low speed cool until the
system pressures stabilize.
3. Front seat the suction service valve and allow
the compressor to pump down to 0 to 5 in. Hg
vacuum (0 to -17 kPa).
4. Turn the unit Off.
5. Monitor the suction pressure. It will rise very
slowly as the discharge pressure leaks back
through the discharge device into the
compressor. If the suction pressure is rising
steadily, the LIS might be leaking.
6. Check the temperatures of the refrigeration
lines on each side of the LIS by hand. A
temperature difference between the two sides
of the LIS indicates it is leaking.
7. Use the Mechanics/Premium HMI Control
Panel to enter the Interface Board Test Mode.
Refer to the appropriate Microprocessor
Diagnostic Manual for specific information
about the Interface Board Test Mode.
8. From the Interface Board Test Mode select
Liquid Injection Valve.
9. Momentarily (for approximately 1 second)
energize the LIS with the Interface Board Test
Mode. The suction pressure should rise
slightly. If the suction pressure does not rise,
the LIS is not opening. Check the continuity
of the wiring and the solenoid coil before
assuming the solenoid is faulty.
10. Back seat the suction service valve and
perform a “Refrigerant Gauge Removal”
procedure.
Liquid Injection Solenoid (LIS)
Replacement
Removal
1. Recover the refrigerant charge.
2. Unsolder the inlet/outlet lines from the liquid
injection solenoid.
3. Remove liquid injection solenoid mounting
bolts and remove the liquid injection solenoid
from the unit.
Installation
1. Install and bolt the liquid injection solenoid
assembly in the unit.
2. Solder (95-5 Solder) the inlet liquid line and
the outlet line to the injection solenoid.
3. Pressurize the system and test for leaks.
4. If no leaks are found, replace the liquid line
drier then evacuate the
system.
5. Recharge the unit with refrigerant and check
the compressor oil.
6. Test the unit to see that the valve is properly
installed.
Purge Valve (PV) Test
1. Attach a gauge manifold to the suction service
valve and the discharge service port. Attach
another low pressure gauge to the suction
access port located in the suction line near the
accumulator inlet. Low loss fittings must be
used on the hoses connected to the discharge
service port and the suction access port.
2. Operate the unit in low speed cool.
3. Front seat the receiver tank outlet valve and
allow the low side to pump down to 0 to 5 in.
Hg vacuum (0 to -17 kPa).
CAUTION: Do not run scroll compressor
in a vacuum for more than 1 minute.
Summary of Contents for UT-1200
Page 10: ...Table of Contents 10...
Page 20: ...Safety Precautions 20...
Page 76: ...Operating Instructions for Premium HMI Control Panel 76...
Page 88: ...Electrical Maintenance 88...
Page 98: ...Engine Maintenance 98 Figure 167 Fuel Components...
Page 142: ...Refrigeration Service Procedures 142...
Page 148: ...Clutch Maintenance 148...
Page 150: ...Structural Maintenance 150...
Page 162: ...Wiring and Schematic Diagrams Index 162...
Page 163: ...163 Schematic Diagram Page 1 of 2...
Page 164: ...164 Schematic Diagram Page 2 of 2...
Page 165: ...165 Wiring Diagram Page 1 of 5...
Page 166: ...166 Wiring Diagram Page 2 of 5...
Page 167: ...167 Wiring Diagram Page 3 of 5...
Page 168: ...168 Wiring Diagram Page 4 of 5...
Page 169: ...169 Wiring Diagram Page 5 of 5...