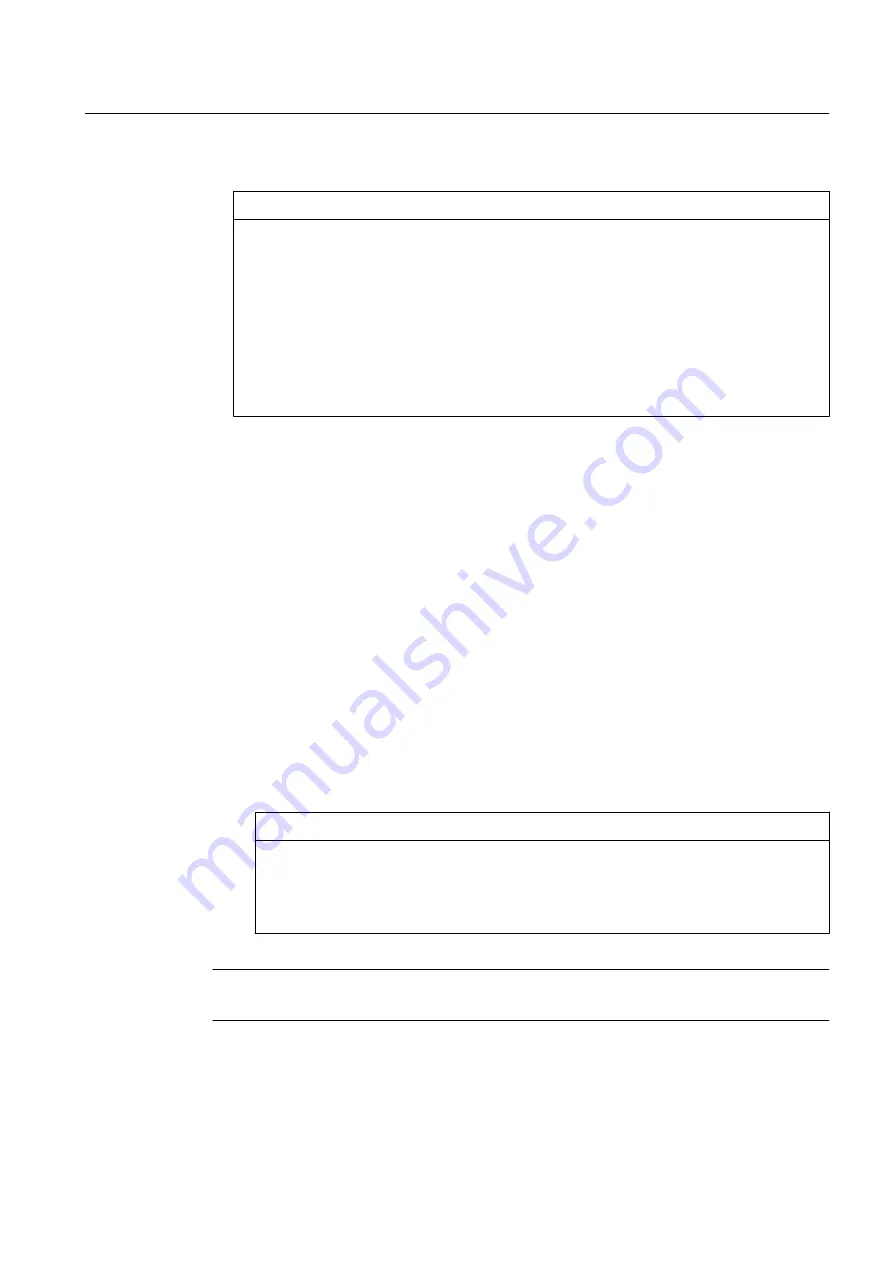
3. If it runs perfectly, connect a load.
NOTICE
Thermal overload of motors connected directly to the line supply
In addition to the load torque, the ramp-up (accelerating) time is essentially influenced by
the moment of inertia to be accelerated. While ramping up when connected to the line
supply, the inrush (starting) current is a multiple of the rated current. This can result in
thermal overload. This can damage the motor.
As a consequence, when ramping up, observe the following:
● Monitor the ramp-up time and number of consecutive starts.
● Comply with the limit values and/or ramp-up conditions specified in the catalog or the
order documentation.
4. During the test run, check and document the following:
– Check whether it is running smoothly.
– Document the voltage, current and power values. As far as possible, document the
corresponding values of the driven machine.
– If this is possible using the available measuring equipment, check the bearing and stator
winding temperatures until they have reached steady-state values.
– Check the machine for noise or vibrations on the bearings or bearing shields as it runs.
5. In case of uneven running or abnormal noise, switch off the machine. As the machine runs
down, identify the cause.
– If the mechanical operation improves immediately after the machine is switched off, then
the cause is magnetic or electrical.
– If the mechanical running does not improve immediately after switching the machine off,
then the cause is mechanical.
- Imbalance of the electrical machine or the driven machine
- The machine set has not been adequately aligned
- The machine is being operated at the system resonance point. System = motor, base
frame, foundation, ...
NOTICE
Serious damage to the machine
If the vibration values in operation are not maintained in accordance with DIN ISO
10816-3, then the machine can be mechanically destroyed.
● During operation, observe the vibration values in accordance with DIN ISO 10816‑3.
Note
You can find more information in Chapter 2 of catalog D81.8.
Start-up
7.8 Test run
SIMOTICS FD 1MM1
Operating Instructions 02/2019
101
Summary of Contents for SIMOTICS FD 1MM1 Series
Page 2: ...05 02 2019 16 03 V11 01 ...
Page 30: ...Description SIMOTICS FD 1MM1 30 Operating Instructions 02 2019 ...
Page 142: ...Maintenance 9 2 Corrective Maintenance SIMOTICS FD 1MM1 142 Operating Instructions 02 2019 ...
Page 166: ...Disposal 11 5 Disposal of components SIMOTICS FD 1MM1 166 Operating Instructions 02 2019 ...
Page 168: ...Service and Support SIMOTICS FD 1MM1 168 Operating Instructions 02 2019 ...
Page 172: ...Quality documents SIMOTICS FD 1MM1 172 Operating Instructions 02 2019 ...
Page 177: ......