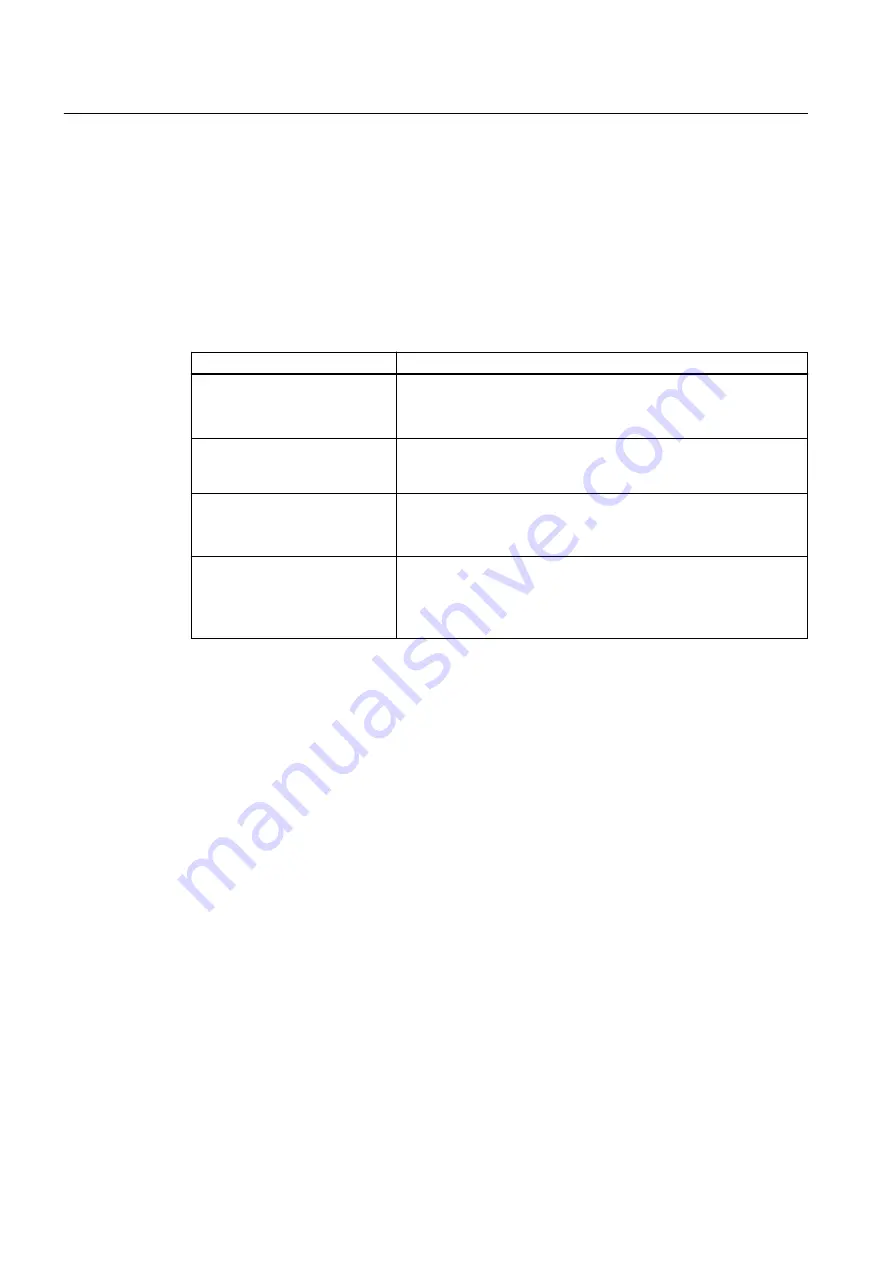
Rolling-contact bearings
The machines are equipped with different types of rolling-contact bearings depending on the
version and the operating conditions described in the order. The different types are listed on the
lubricant plate of the machine. In converter operation an insulated bearing is usually installed
on the non-drive end. The following rolling-contact bearing variants are available:
Table 3-4
Rolling-contact bearing variants
Version
Rolling-contact bearing
Horizontal type of construction,
coupling output
● Drive end: Deep-groove ball bearing as a fixed bearing
● Non-drive end: Deep-groove ball bearing as a floating bearing
with axial compression springs
Horizontal type of construction,
for increased transverse forces
e.g. in the case of belt coupling
● Drive end: Cylindrical-roller bearing as a floating bearing
● Non-drive end: Deep-groove ball bearing as a fixed bearing
Vertical type of construction,
shaft height 315, coupling output
● Drive end: Deep-groove ball bearing as a fixed bearing
● Non-drive end: Deep-groove ball bearing as a floating bearing
with axial compression springs
Vertical type of construction,
shaft height 355 ... 450
● Drive end: Pairing of angular-contact ball bearing / deep-groove
ball bearing as a fixed bearing
● Non-drive end: Deep-groove ball bearing as a floating bearing
with axial compression springs
The standard version of the machine is not suitable for belt couplings. This can result in damage
to the machine.
Automatic regreasing system (option)
The roller bearings are optionally equipped with an automatic regreasing system. The roller
bearings are supplied with new grease portions by the regreasing system in parameterized
time intervals.
Rolling-contact bearing design for "Increased degree of protection" (option)
Improved sealing of the bearing units to prevent dust and water from getting in can be achieved
by positioning a grease chamber ahead of the actual bearing unit. Although the same grease
is used in both cases for reasons of convenience, a distinction is made here between
"lubricating grease" and "sealing grease" because of their different functions.
Layout
The spent lubricating grease collects in the space between the bearing housing and the outer
bearing cap. The latter also forms the sealing grease chamber with the labyrinth sealing ring
(optional). The second lubricating nipple containing the grease duct for pressing in the sealing
grease is also located in the outer bearing cap. The chamber is sealed off from the space where
the lubricating grease collects by a V-ring or a V-ring and felt ring combination which prevents
the sealing grease in the chamber from penetrating into the lubricating grease collecting space.
Description
SIMOTICS FD 1MM1
28
Operating Instructions 02/2019
Summary of Contents for SIMOTICS FD 1MM1 Series
Page 2: ...05 02 2019 16 03 V11 01 ...
Page 30: ...Description SIMOTICS FD 1MM1 30 Operating Instructions 02 2019 ...
Page 142: ...Maintenance 9 2 Corrective Maintenance SIMOTICS FD 1MM1 142 Operating Instructions 02 2019 ...
Page 166: ...Disposal 11 5 Disposal of components SIMOTICS FD 1MM1 166 Operating Instructions 02 2019 ...
Page 168: ...Service and Support SIMOTICS FD 1MM1 168 Operating Instructions 02 2019 ...
Page 172: ...Quality documents SIMOTICS FD 1MM1 172 Operating Instructions 02 2019 ...
Page 177: ......