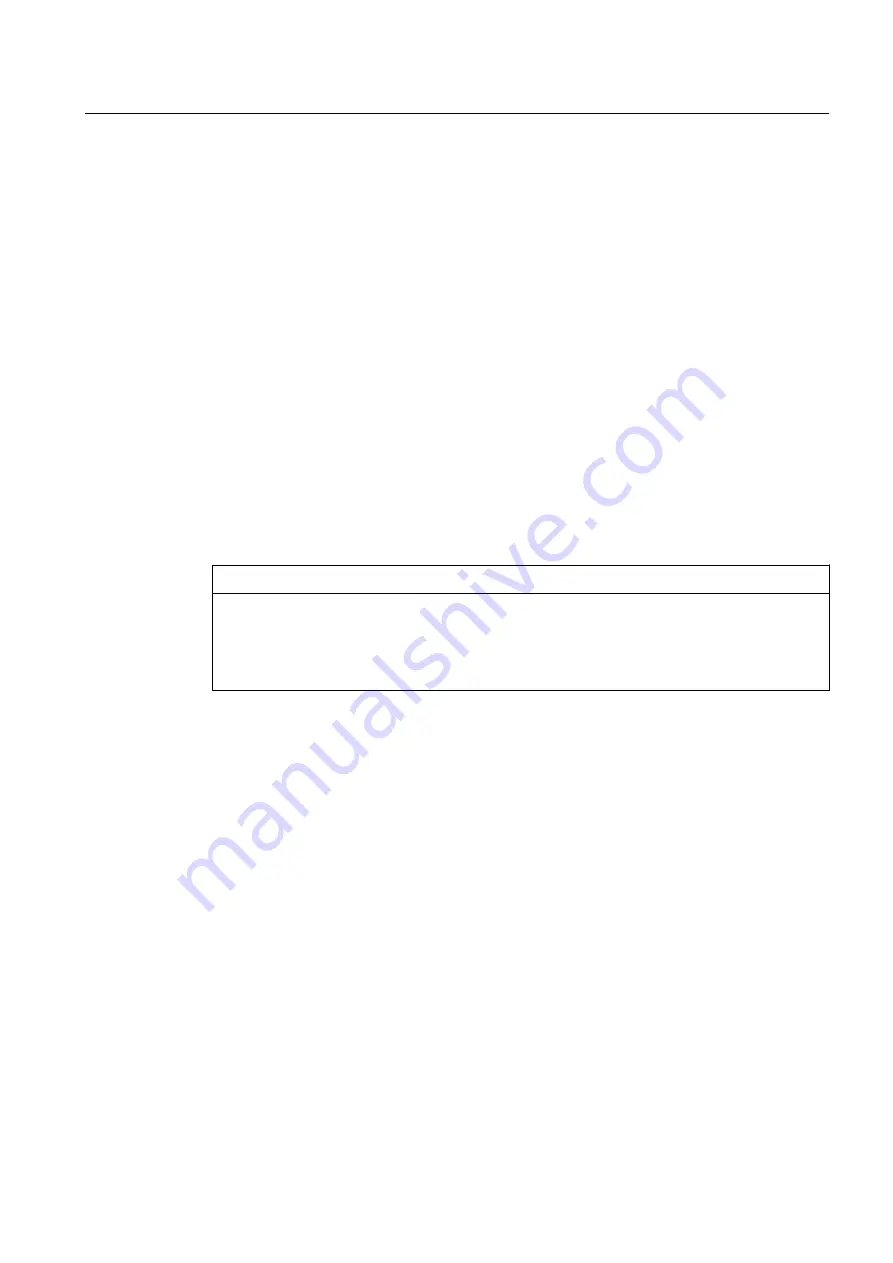
If the motor has been ordered with brought-out leads, in this case you must comply with the
relevant conditions for Zone 2. It is assumed that the buyer, the installer and users of the
installation are familiar with these conditions and will carefully observe them.
6.4.6
Connecting the machine for a specific direction of rotation
If the machine has one shaft extension or two shaft extensions with different diameters, the
direction of rotation when looking at the front of the single or the thicker shaft extension is
defined as follows:
● If you connect the line cables with phase sequence L1, L2, L3 to U, V, W or according to
NEMA at T
1
T
2
T
3
, then a clockwise phase sequence is obtained.
● If you interchange two connections, e.g. L1, L2, L3 at V, U, W or according to NEMA at
T
2
T
1
T
3
, then a counterclockwise phase sequence is obtained.
● On machines which are only allowed to run in one direction, the rating plate shows an arrow
which indicates the permitted direction of rotation, and it also specifies the terminal
connections in the required phase sequence.
Check the appropriate data before connecting the line feeder cables.
NOTICE
Incorrect direction of rotation
The machine will not be adequately cooled if it is operated other than how it was originally
ordered or with the incorrect direction of rotation. This can result in machine damage.
Observe the direction of rotation data on the nameplate.
6.4.7
Undrilled entry plate
If the entry plate is undrilled, you should match the number and size of the cable glands to the
operating conditions.
1. Unscrew the cable entry plate.
2. Drill the required number of holes or threads in the required size into the cable entry plate.
The thickness of the plate is selected in such a way as to give a sufficient number of turns
when the holes are tapped.
Please note that you are responsible for ensuring that the entry plate still has sufficient
strength after the holes have been drilled and tapped.
3. Mount the cable entry plate and the cables with the cable glands onto the terminal box.
Electrical connection
6.4 Preparation
SIMOTICS FD 1MM1
Operating Instructions 02/2019
81
Summary of Contents for SIMOTICS FD 1MM1 Series
Page 2: ...05 02 2019 16 03 V11 01 ...
Page 30: ...Description SIMOTICS FD 1MM1 30 Operating Instructions 02 2019 ...
Page 142: ...Maintenance 9 2 Corrective Maintenance SIMOTICS FD 1MM1 142 Operating Instructions 02 2019 ...
Page 166: ...Disposal 11 5 Disposal of components SIMOTICS FD 1MM1 166 Operating Instructions 02 2019 ...
Page 168: ...Service and Support SIMOTICS FD 1MM1 168 Operating Instructions 02 2019 ...
Page 172: ...Quality documents SIMOTICS FD 1MM1 172 Operating Instructions 02 2019 ...
Page 177: ......