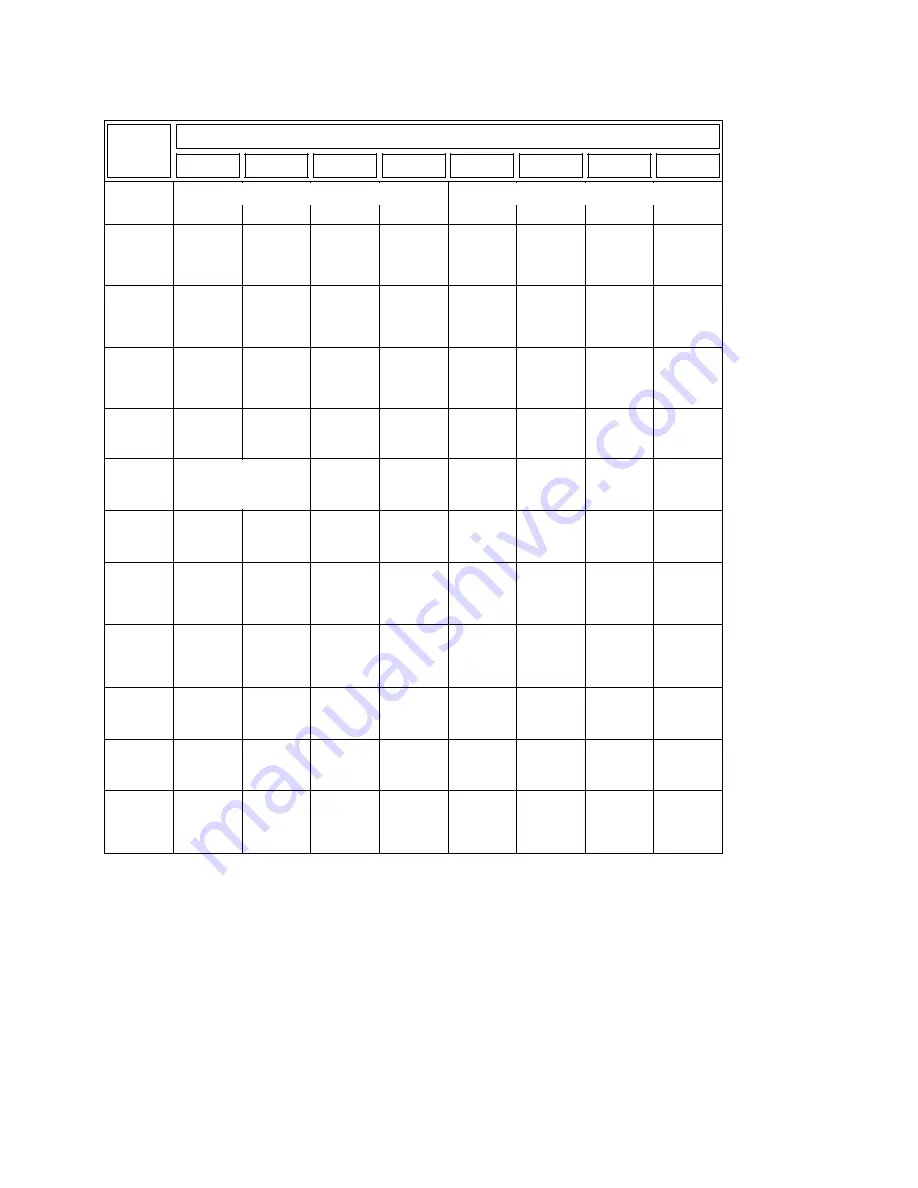
1 NC/Drive Machine Data
01.99
1.9.3 Axis-specific MD bits 2 (max. 30 axes)
1.9.3
Axis-specific MD bits 2 (max. 30 axes)
7
6
5
4
3
2
1
0
Bit No.
MD No.
1800*
1804*
Adaption
1)
QEC
1)
Axis can
travel against
fixed stop
Sensor signal
PLC travel
against fixed
stop 2)
Monitoring
clamping tol.
act.
Automat.
tacho.
compen-
sation
1)
Symm.
travers. range
with ENDAT
abs. encoder
(from SW 6.3)
1808*
Range
extension
ENDAT
absolute
encoders
SIPOS
Singleturn
abs. enc.
available
1)
2nd meas.
sys. distance
coded
1st meas.
sys.
distance-
coded
Absolute
offset
MD 396*
valid
Absolute
encoder
counts CCW
Value range
extension of
absolute
offset
Axis with
absolute
encoder
system
1812*
Sign
change
setpoint
master/
slave
4)
Torque
comp.
control acts
on ma-
ster/slave
4)
Torque
comp.
control acts
on ma-
ster/slave
4)
Master/
slave mode
after Power
On
4)
Position-
contr. corr.
if error
occurs
5)
Adapt.
comp. time
const. neur.
QEC
3)
Learning
phase
neural QEC
3)
Neural
QEC
3)
1820*
Contour
monitoring
not acitve
Pulse
encoder
ON
No. of encod.
pulses (611D)
2nd meas.
system
2nd measur.
system with
external zero
mark
2)
No. of
encod. puls.
(611D) 1st
meas. syst.
1st measur.
system with
external zero
mark
2)
Zero
monitoring
ON
Setpoint
smoothing
ON
1824*
Setting of
reference
dimension
allowed
3)
Sign change
actual value
2
1)
Set absolute
system to
reference
dimension
3)
Multiple
assignment
setpoints
2)
2nd meas.
system
exists
1)
QEC un-
delayed
4)
1828*
Linear scale
from
SW 6.3
Extended
para. set
switch-
over
3)
1832*
from
SW 6.3
Monitoring
axis 2nd
measuring
circuit
Monitoring
axis 1st
measuring
circuit
Multiple
assignment
actual value
2nd meas.
circuit
Multiple
assignment
actual value
1st meas.
circuit
PT2
contour
monitoring
active
1844*
Velocity
limitation of
following
axes
(from SW 6)
Test bit
compensat.
controller
LINK_ON
after
POWER ON
Overwriting
position
permitted
Change link
factor
permitted
Reconfig-
uration
permitted
Axis may be
following
axis
1848*
Synchroni-
zation in
tooth pitch
(SW 6)
Block change
after pos.
reached (SW
5 and higher)
Block change
after
synchroniza-
tion reached
Following
axis overlay
index related
Suppression
of
acceleration
limitation
Block change
with
synchronism
fine
1852*
TO
corrections
included
in calc.
Include
programmed
zero offset
G58...G59
Include
external ZO
in calc.
Calculate
settable ZO
G54...G57
Include DRF
and Preset
in calc.
Reference
system
GI positions
1856*
Time-
optimized
synchroni-
zation
(from SW 6)
Acceleration
limitation of
ELG
following
axes
Position control resolution
Display resolution
Effect on meas. systems
LEC assignment
00=first
01=second
10=both
11=both
_______
1)
SW 2 and higher
* .... 0
1st axis
1
2nd axis
.
.
.
11 30th axis
2)
SW 3 and higher
3)
SW 4 and higher
4)
SW 4.4 and higher
5)
SW 5 and higher
1–42
© Siemens AG 1992 All Rights Reserved 6FC5197- AA60
SINUMERIK 840C (IA)
Summary of Contents for SIMODRIVE 611-D
Page 2: ......