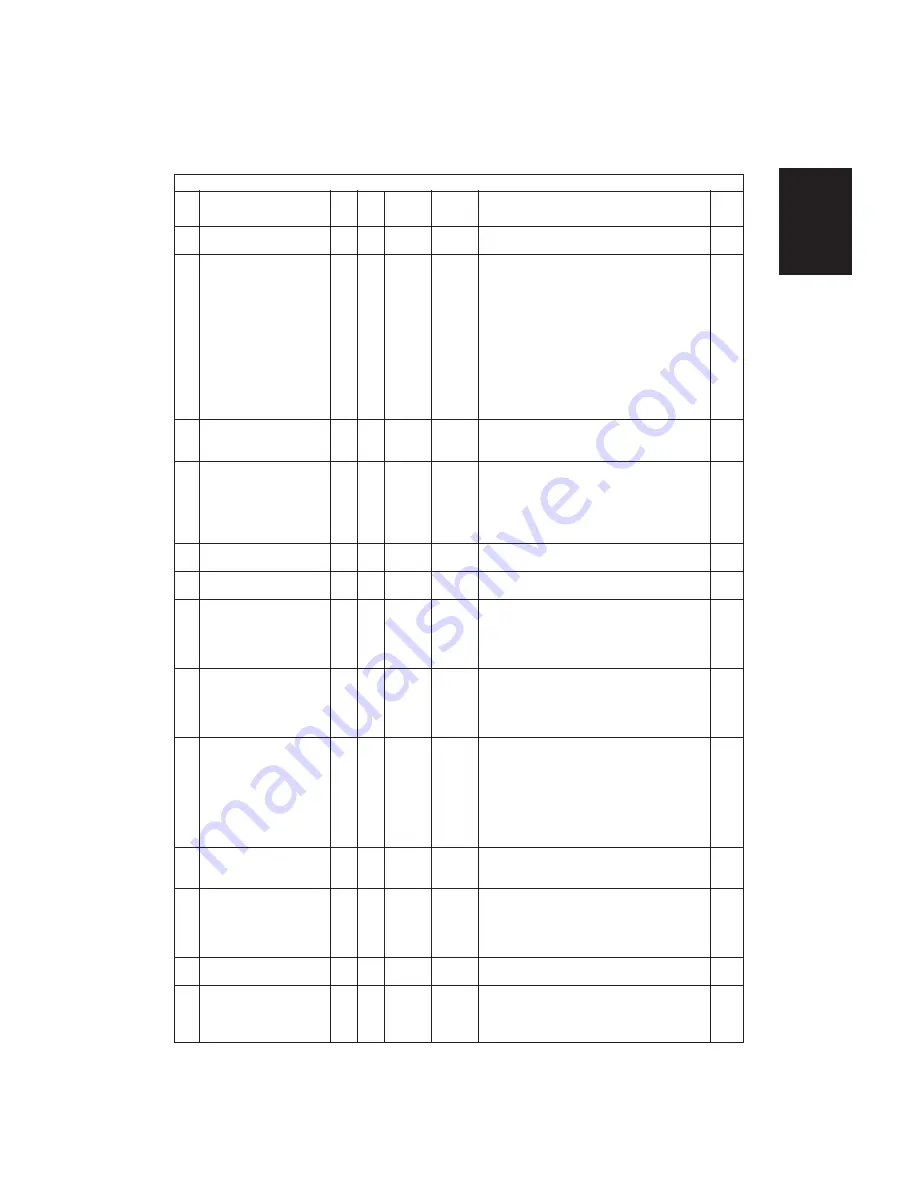
1 - 29
ADJUSTMENT
418 Charge corona wire
All
0
0-1
1
cleaning
449 Temporary laser running service All
0
0-1
1
mode when the laser beam
position adjustment fails. Key in
the value, press the SET key to
store or the CLEAR key to reset.
Set to 1 until copier laser unit
can be replaced. Service call
Error Codes CA3, CA4, CA5,
CA6, CAA, CAB, CAC, CAD,
CAE, CAF, or CD0.
See troubleshooting section
for additional information.
460 RADF reversing of transfer belt
All
0
0-1
1
during original feed to align
originals against the original stop.
461 RADF automatic detection
All
0
0-1
1
of the original size.
464 Correspondence for
All
1
0-1
1
Exposure fluetuations
480 Paper source priority
All
1
0-4
1
selection
481 Automatic paper source
All
1
0-2
1
change.
482 Paper feed retry.
All
0
0-1
1
483 Polygonal motor pre-running.
All
All
0
0-2
1
484 Polygonal motor stops at an
All
All
0
0-1
1
auto clear (time out) of
control panel settings.
485 Polygonal motor rotation or
All
All
0
0-1
1
stop mode.
486 Polygonal motor stop time
All
All
0-2
1
487 Duplexer initial alignment
All
0
0-1
1
operation
0: Enabled (cleans every 2,000 copies/prints)
1: Disabled (no cleaning)
0: Normal Mode
the laser unit operates in this mode unless a
service call is indicated when the beam position
adjustment fails.
1: Continuous Mode
Set to this mode when the laser beam adjust-
ment has failed. The results of this setting
places the laser beam close to target even
though the beam position adjustment has failed.
0: Disabled
1: Enabled
0: Non-standard(Machine will not stop and prompt
operator to select copy size when non-standard
originals are used).
1: Standard(Machine will stop and prompt
operator to select copy size when non-standard
originals are used).
0: Disabled
1: Enabled
0: LT/A4
1: LCC
2: Upper drawer
3: Middle drawer 4: Lower drawer
0: OFF
1: Normal
3: Extended
when 1 is set, a paper source becomes empty and
the same size paper is present in another source
the machine will automatically switch to that
source of paper.
0: Enabled
1: Disabled
when set to 0 the machine will only attempt to feed
the paper 1 time before display a misfeed condition.
When set to 1 the machine will attempt to feed the
paper 2 times before displaying a misfeed condition.
0: Enabled - RADF (when originals are placed in the
tray) and Exposure Glass (when RADF is lifted).
1: Disabled - Motor starts running when the
START key is pressed. This will delay the start
of copying by 30 seconds.
2: Enabled - RADF only (when originals are
placed in the tray)
Note: This code is effective only when 08-485 is set to 1.
0: Enabled - RADF and exposure glass.
1: Disabled
Note: This code is effective only when 08-485 is set to 1.
0: Rotation
1: Stop
When Code 485 is set to 1 the polygonal motor
runs all the time.
When Code 485 is to 1 the polygonal motor runs
according to the settings of Codes 483 and 486.
0: 1 minute
1: 3 minutes
2: 5 minutes
Effective when 08-484 is set to 0.
0: Enabled
1: Disabled
Correct the side skew and the paper corner
folding within three copies. If default 1 is selected,
the copying speed is a little lower than normal.
08 MODE
IMAGE
ALLOWABLE
PROCE-
CODE
NAME
MODE
DEFAULT
INPUT
CONTENTS
DURE
MODE
VALUES
GROUP
Summary of Contents for AR-650
Page 103: ...MAINTENANCE 2 6 Rear drive system 38 36 37 3 54 54 54 54 54 54 96 12 81 63 63 46 ...
Page 104: ...2 7 MAINTENANCE ADF front sectional view 100 104 109 105 106 102 108 99 101 103 107 98 ...
Page 122: ...SUPPLIES 3 10 13 CONNECT 15 CLOSE 2 1 14 CLOSE 1 2 16 TURN ON 17 PRESS 18 END ...
Page 169: ...Click Finish button then Virtual Modem installation is completed 5 5 ...
Page 179: ...To make the connection ONLINE mode click button before firmware downloading 5 15 ...
Page 194: ......
Page 195: ...MEMO ...
Page 196: ...MEMO ...
Page 197: ...MEMO ...
Page 198: ...MEMO ...
Page 199: ...MEMO ...