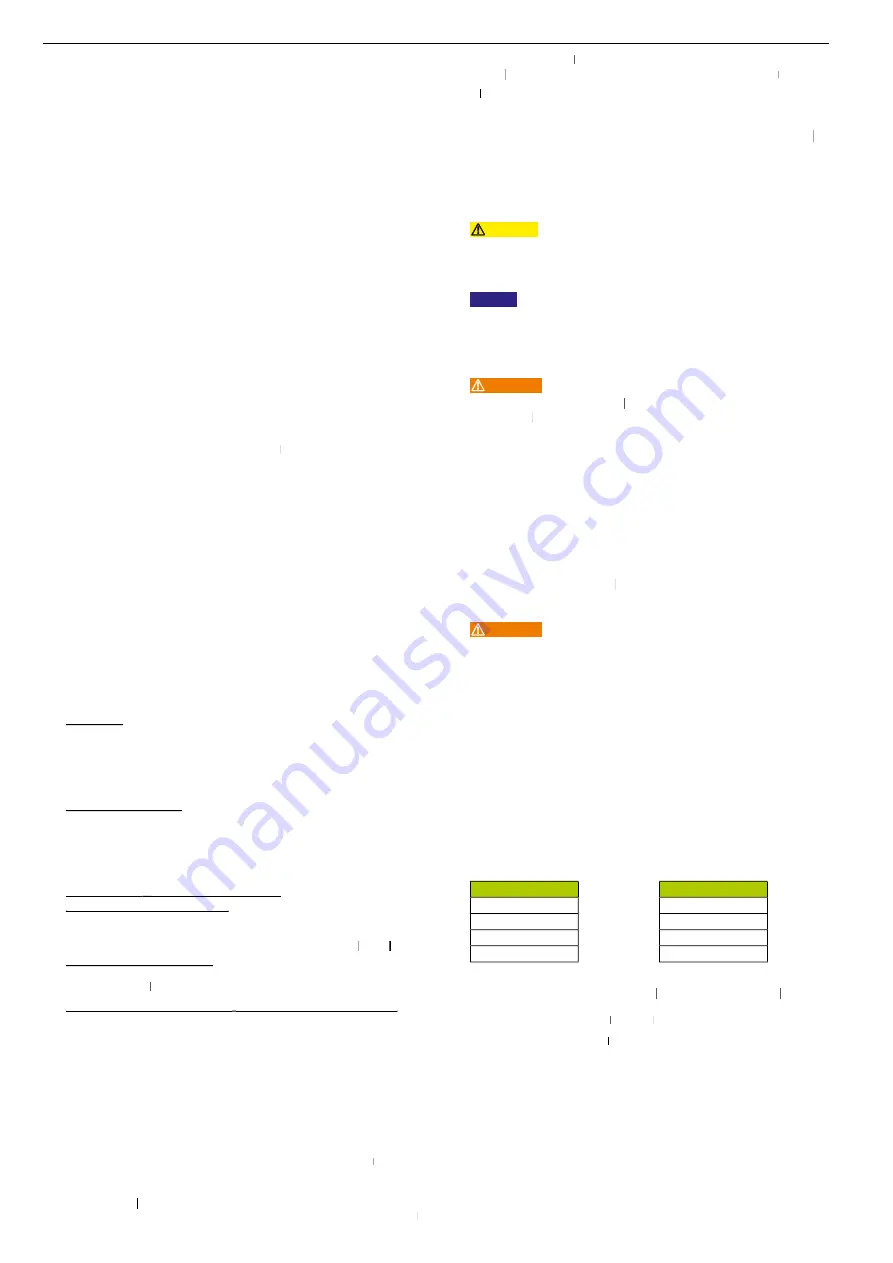
eng eng
ROLLER’S Multi-Control SLW, electronic fl ushing and pressure testing unit,
pressure test with compressed air and water, without accessories
115601
ROLLER’S Inject TW, disinfection unit
115602
ROLLER’S Inject H, cleaning and preservation unit
115612
Printer
115604
Paper roll, pack of 5
090015
Case with inserts for printer
115703
ROLLER’S Plus TW-D Color, dosing solution for disinfection
115605
ROLLER’S Plus H-R, cleaner for heating systems
115607
ROLLER’S Plus H-K, corrosion protection for heating systems
115608
Test strips 0 – 1000 mg/l H
2
O
2,
pack of 100
091072
Test strips 0 – 50 mg/l H
2
O
2,
pack of 100
091073
Suction/pressure hose Ø 1", 1.5 m long, with 1" hose screw fi ttings,
for fl ushing, disinfection, cleaning, preservation
115633
High-pressure hose Ø ½", 1.5 m long, with ½" hose screw fi ttings,
for pressure testing with water (ROLLER’S Multi-Control SLW)
115634
Pneumatic hose Ø 8 mm, 1.5 m long, with quick couplings NW 5
115637
Connecting hose compressor/water connections with 1" hose
screw fi tting and quick coupling NW 7.2 for pressure testing
with air (ROLLER’S Multi-Control SL/SLW)
115618
Compressed air hose pneumatic tools, 1.5 m long,
with quick couplings NW 7.2, for connecting pneumatic tools
115621
Compressed air hose Ø 8 mm, 7 m long, with quick coupling
DN 5 (plug) and G ½" hose screw fi tting, for pressure testing
with compressed air (ROLLER’S Multi-Control SL/SLW)
115667
Compressed air hose Ø 8 mm, 1.5 m long, with quick coupling
DN 5 (plug, socket) for gas testing with compressed air
(ROLLER’S Multi-Control SL/SLW)
115747
High-pressure hose Ø ½", 7 m long, with G ½" hose screw fi ttings,
with caps, for pressure testing of pipe systems and vessels
with caps, for pressure testing of pipe systems
with caps, for pressure testing of pipe systems
with water (ROLLER’S Multi-Control SLW)
115661
1" double nipple, for connecting 2 suction/pressure hoses
045159
Fine fi lter with fi lter cartridge 90 µm
115609
Fine fi lter cartridge 90 µm
043054
Caps 1" with chain (ROLLER’S Multi-Control)
115619
Plugs 1" with chain (suction/pressure hoses)
115620
Plugs ½" with chain (ROLLER’S Multi-Control SL/SLW) 115624
Caps ½" with chain (high-pressure hose)
115623
Pressure gauge 6 MPa/60 bar /870 psi
115140
Fine scaled pressure gauge 1.6 MPa/16 bar/232 psi,
115045
Fine scaled pressure gauge 250 hPa/250 mbar/3.6 psi,
047069
Machine cleaner
140119
1.3. Applications
Device storage temperature
≥ 5°C (≥ 41 °F)
Water temperature
5°C – 35°C (41 °F – 95 °F)
Ambient temperature
5°C – 40°C (41 °F – 104 °F)
pH value
6,5 – 9,5
Smallest test volume
approx. 10 l
Compressor
Compressor
Operating pressure
≤ 0.8 MPa/8 bar/116 psi
Oil separation rate
oil-free
Extraction rate
≤ 230 Nl/min
Compressed air vessel volume (Fig. 1 (35))
4.9 l
Condensation and particle fi lter
5 µm
Flushing of pipe systems
Flushing of pipe systems
Flushing water connections
DN 25, 1"
Water pressure pipe network
≤ 1 MPa/10 bar/145 psi
Water pressure when fl ushing with compressed air ≤ 0.7 MPa/7 bar/101 psi
Water fl ow rate
≤ 5 m³/h
Pipe diameter installation
≤ DN 50, 2"
Pressure testing
Pressure testing of drinking water installations
f drinking water installations
(ROLLER’S Multi-Control SL/SLW)
(ROLLER’S Multi-Control SL/SLW)
Pressure test with compressed air
≤ 0.4 MPa/4 bar/58 psi
Reading accuracy < 200 mbar
1 hPa/1 mbar/0.015 psi
Reading accuracy ≥ 200 mbar
100 hPa/0,1 bar
Reading accuracy ≥ 200 mbar
100 hPa/
Reading accuracy ≥ 200 mbar
100 hPa/
/1.5 psi
0,1 bar
0,1 bar
(ROLLER’S Multi-Control SLW)
(ROLLER’S Multi-Control SLW)
Pressure test with water
≤ 1.8 MPa/18 bar/261 psi
Reading accuracy
0.02 MP
Reading accuracy
Reading accuracy
a/0.2 bar/3 psi
Pressure testing of gas installations
Pressure testing of gas installations (ROLLER’S Multi-Control SL/SLW)
(ROLLER’S Multi-Control SL/SLW)
Pressure test with compressed air
≤ 0.3 MPa/3 bar/44 psi
Reading accuracy < 200 mbar
10 Pa/0,1 mbar/0.002 psi
Reading accuracy ≥ 200 mbar
100 hPa/0,1 bar/1.5 psi
1.4. Electrical/electronic data
230 V~; 50 Hz; 1,500 W
110 V~; 50 Hz; 1,500 W
Type of protection terminal box
IP 44
Type of protection device, motor
IP 20
Protection class
I
Operating mode (continuous operation)
S 1
Screen (LCD)
3.0"
Resolution
128 ×
Resolution
128
Resolution
128 64 pixels
Data transfer with USB stick
USB port
Printer, battery
NiMH 6 V –
---, 800 mAh
Charger printer
Input
100 – 240 V~; 50 – 60 Hz; 0.15 A
Charger printer
Charger printer
Output
5 V –
---; 680 mA
; 680 m
; 680 m
1.5. Dimensions L × W × H
570 ×
imensions L × W × H
imensions L × W × H
370 × 530 mm (22.4"× 14.6"× 20.9")
Paper roll printer B × Ø
Paper r
Paper r
57 ×
57
57 ≤ 33 mm
1.6. Weight
W
W
ROLLER’S Multi-Control S
32.0 kg (71 lb)
ROLLER’S Multi-Control SL
36.7 kg (81 lb)
ROLLER’S Multi-Control SLW
39.0 kg (86 lb)
ulti-Control SLW
39.0 kg (86
ulti-Control SLW
39.0 kg (86
1.7. Noise information
Work place-related
Emission value L
PA
= 73 dB(A); L
WA
= 92 dB(A); K = ± 1 dB
2. Start-up
CAUTION
CAUTION
Transport weights above 35 kg must be carried by at least 2 persons.
Compressed air line compressor/pressure vessel (47) gets hot and can cause
burns if touched.
NOTICE
NOTICE
ROLLER’S Multi-Control is not intended/suitable for permanent connection to
the installation. Disconnect all hoses from the installation after completing the
work. ROLLER’S Multi-Control may not be operated unattended.
2.1. Electrical connection
WARNING
WARNING
Caution: Mains voltage present! Before connecting the electronic fl ushing and
Caution: Mains voltage present!
Caution: Mains voltage present!
pressure testing unit, check whether the voltage given on the rating plate corre-
pressure testi
pressure testi
sponds to the mains voltage. Only use sockets/extension leads with a functioning
PE contact. The function of the PRCD fault current circuit breaker (Fig. 1 (1))
must be checked every time before start-up and before beginning work:
1. Plug the mains plug into the socket.
2. Press the RESET button (2), the PRCD control lamp (Fig. 1 (39)) lights red
(operating state).
3. Pull out the mains plug, the PRCD control lamp (39) must go out.
4. Plug the mains plug back into the socket.
5. Press the RESET button (2), the PRCD control lamp (39) lights red (oper-
ating state).
6. Press the TEST button (3), the PRCD control lamp (39) must go out.
7. Press the RESET button (2) again, the PRCD control lamp (39) lights red.
7. Press the RESET button (2
7. Press the RESET button (2
The control lamp (Fig. 2 (5)) lights green. ROLLER’S Multi-Control is ready
for operation after about 10 s.
WARNING
WARNING
If the described functions of the PRCD fault current circuit breaker (Fig. 1 (1))
are not fulfi lled, the device may not be used. There is a danger of electric shock.
The PRCD fault current circuit breaker tests the connected device, not the
installation before the socket nor interconnected extension leads or cable reels.
On building sites, in a wet environment, indoors and outdoors or under similar
installation conditions, only operate the electronic fl ushing and pressure testing
unit on the mains with a fault current protection switch (FI switch) which interrupts
the power supply as soon as the leakage current to earth exceeds 30 mA for
200 ms. A cable cross-section that corresponds to the power of the electronic
fl ushing and pressure testing unit must be selected when using an extension lead.
2.2. Menu structure and on-screen displays
Press the On/Off button on the input and control unit's operating panel (Fig. 2
(4)) for approx. 2 s, then release it. ROLLER’S Multi-Control is switched on and
the compressor switches on. The screen (6) is illuminated and the Logo
ROLLER’S Multi-Control logo appears followed by the Start menu:
ti-Control logo appears fol
ti-Control logo appears fol
ROLLER’S Multi-Control S:
ROLLER’S Multi-Control SL/SLW:
Flushing
Ingredients
Memory Manager
Flushing
Ingredients
Testing
Compressed Air Pump
Memory Manager
The screen display contains a maximum 5 lines with 20 characters each. Lines
with defaults or test values are displayed
language-independently
with defaults or test values are displayed
with defaults or test values are displayed
with phys-
language-independently
language-independently
ical formula symbols, a uniform verbal abbreviation and the value of the test
ical formula symbols, a uni
ical formula symbols, a uni
criterion in the sub-routines. These hav
criterion in the sub-routines. T
criterion in the sub-routines. T
e the following
hese hav
hese hav
meanings:
e the following
e the following
p refer bar xxx
reference tes
p refer bar xxx
ref
p refer bar xxx
ref
t pressure bar
p refer mbar xxx
reference test pressure mbar
p actual bar xxx
actual test pressure
bar
p actual mbar xxx
actual test pressure
mbar
p diff
bar xxx
differential test pressure bar
p diff
mbar xxx
differential test pressure mbar
t stabi min xxx
stabilisation/wait time min
t test
min xxx
test time
min
Δ > 10K
difference >10°C (10 Kelvin) water/environment
PfS
press fi tting system (ZVSHK)
P+M
load test p metal
p H
2
O bar
water pressure
v H
2
O m/s
minimum fl ow speed
t H
2
O
min
Flushing/disinfecting/cleaning/preservation time
22