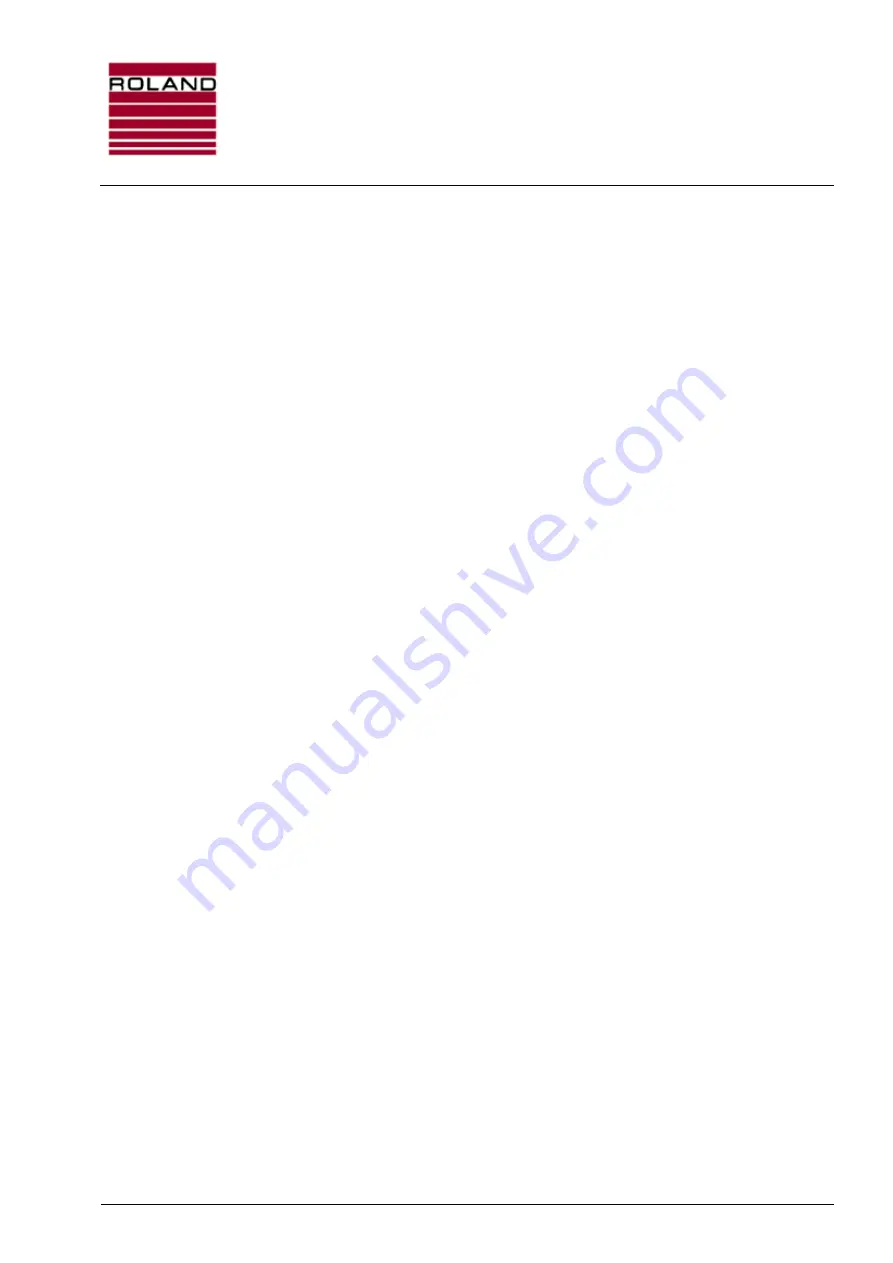
Manual
Weld Seam Detection System R4000 SND40
for Tubes, Cans and Drums
B0059001 / Rev. 2.3
Communication with the PLC
ROLAND ELECTRONIC GmbH · Otto-Maurer-Str. 17 · DE 75210 Keltern · Phone +49 (0)7236-9392-0 · Fax +49 (0)7236-9392-33
61
5.3
Monitoring the Inputs / Outputs of the Control
On triggering the unit via the PLC-IO-interface, the correct function can be checked by the reaction
of the unit.
1)
After the measurement has been initiated with the signal “
IN0 Measuring Start
“, the output
signal “
OUT 7 Motor
” must switch to HIGH within 100 ms. If not, a fault condition exists.
2)
After the max. measurement time (depending on tube diameter, rotation rate and program
parameter “
Transient Time
“) the SND40 must have switched the output “
OUT7 Motor
“ to
LOW. If not, a fault condition exists.
Sequence plan for measuring:
1.
Prepare the tube for measuring
2.
Check if signal “
OUT2 Ready for measuring
“ is HIGH
If YES, continue. If NO, the unit is not ready for measuring (e.g. during Teach-In)
3.
Switch the signal “
IN0 Measuring Start
“ to HIGH and start the tube turn
4.
Check if signal “
OUT7 Motor
“ is HIGH within 100ms
If YES, continue. If NO, error condition exists
5.
When signal “O
UT7 Motor
“ is LOW, stop the tube turn instantly.
At the same time, monitor whether the signal “
OUT7 Motor
“ is not LOW after time xx
otherwise a fault condition exists
6.
Evaluate the signal “
OUT6 reduced detection capability
“ or “
OUT5 Error
“
7.
Switch the signal “
IN0 Measurement Start
“ to LOW
8.
Remove the tube.
The time xx depends on the tube diameter, the tube rotation rate and the set transient
time.