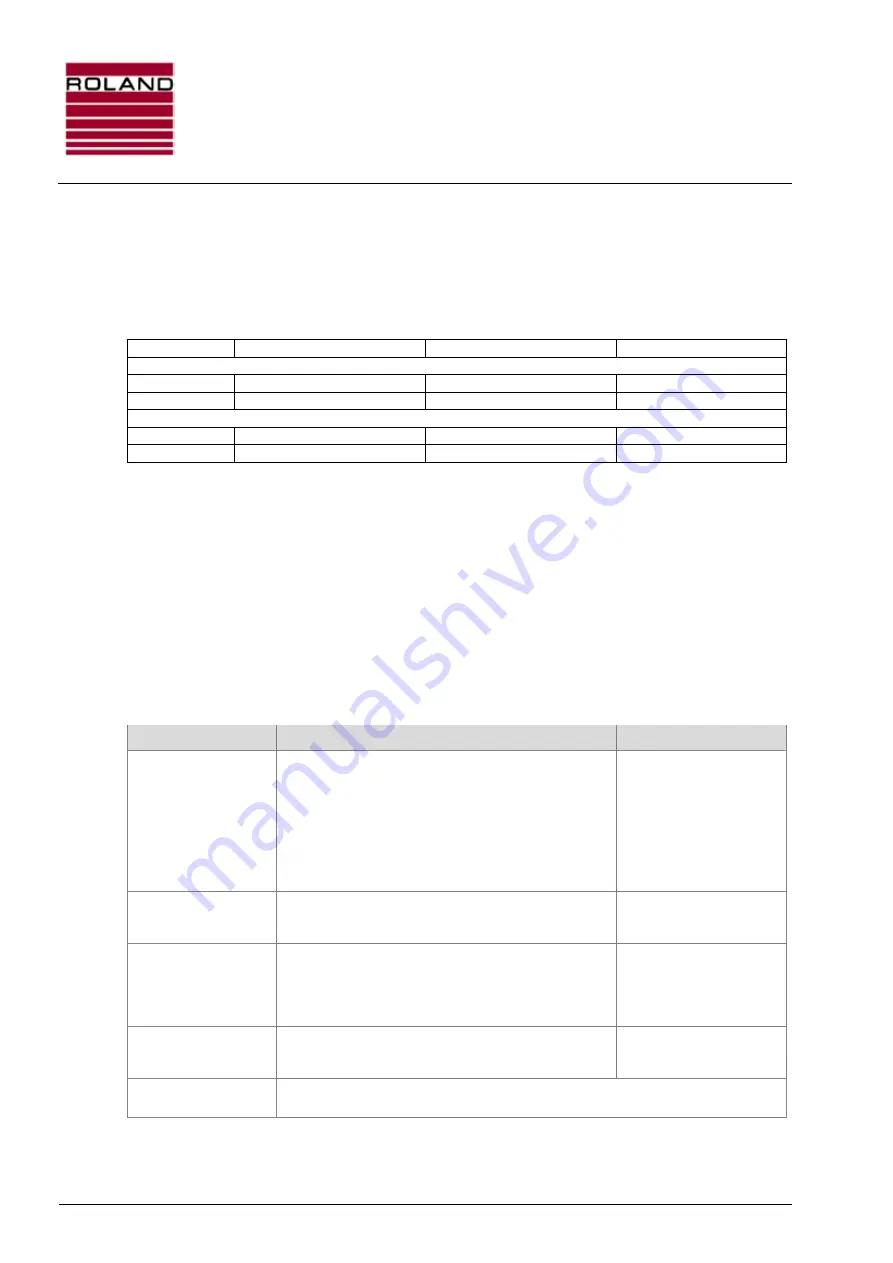
Manual
Weld Seam Detection System R4000 SND40
for Tubes, Cans and Drums
Maintenance
B0059001 / Rev. 2.3
128
ROLAND ELECTRONIC GmbH · Otto-Maurer-Str. 17 · DE 75210 Keltern · Phone +49 (0)7236-9392-0 · Fax +49 (0)7236-9392-33
10.2.1 Air gaps and wearing limits of the sensors
Due to the wearing of the rollers, the air gaps at the sensor decrease. When the wearing limit has
been reached, the rollers need to be exchanged by new ones.
The following chart shows the air gaps of the sensors in new condition as well as the minimal
permissible air gaps at the wearing limit.
EC9… / NS9… / NS12…
NS24-EC18…
NS24-EC30…
Air gap between pole boots and sheet
in mm (inch)
in new condition
0.2 – 0.25 (.008“ - .01“)
0.5 – 0.55 (.02“ - .022“)
2.0 – 2.05 (.079“ - .081“)
at wearing limit
< 0.1 or > 0.35 (.004“ or .014“)
< 0.3 or > 0.7 (.012“ or .028“)
< 1 or > 2.5 (.039“ or .098“)
Air gap between sensor element and sheet
in mm (inch)
in new condition
0.6 – 0.65 (.024“ - .026“)
0.5 – 0.55 (.02“ - .022“)
2.0 – 2.05 (.079“ - .081“)
at wearing limit
< 0.3 or > 0.75 (.012“ or .03“)
< 0.3 or > 0.7 (.012“ or .028“)
< 1 or > 2.5 (.039“ or .098“)
Pos: 114 /Schweissnaht/Gerä te/SND40/10 Wa rtung/Norma ler Verschle iß und erhö hter Ve rschleiß @ 1\mod_1196091743484_501.docx @ 5273 @ 2 @ 1
10.3 Regular wearing and increased wearing
During operation, a sensor is subject of a certain regular wear. Thus, the sensors need to be
inspected in regular intervals and worn components must be replaced.
If increased wear within a short period is detected, this is a symptom for one or more of the fault
conditions shown below. The cause for this should be immediately found and redressed. In the
worst case a sensor can be unrepairable damaged.
A further symptom for increased wear within a short period is the gradual drift of the measuring
values, because they depend on the mechanical conditions.
The case when increased wear is existing depends considerably on the individual conditions of
application.
Increased wear
Comment
Reduced wear
Sensor is mounted
wrongly or unfavourably.
Sensor is not correctly
aligned.
The sensor can no longer move suspended in the bracket or
runs unevenly on the material. The rubber mounts might
break.
The rollers do not touch down simultaneously and evenly
onto the surface, the sensor runs tilted on the material (the
rollers are „rubbing“ over the surface and wear-out unevenly
or prematurely).
Take care that the sensor is
correctly mounted in the
bracket.
Align the sensor correctly.
All sensor rollers must be
in contact with the surface
and rotate!
This applies also for tubes
as well as for coils.
Rubber mount is
damaged or broken.
Damaged / broken rubber mounts can no longer provide for
elastic suspending and correct guidance. Thus a mis-
positioning and a wrong alignment of the sensor results.
Replace damaged rubber
mounts.
Jacking force too large.
If the sensor is pressed onto the material with too much
force, the rollers and the bearings wear-out too fast. The
rubber mounts might break.
The sensor should be pressed onto the material with a force
which equals its own weight.
Reduce the jacking force.
If the attached rubber
mounts are used, the sensor
should comply only for up to
5mm when touching-down.
Touch down motion too
vehement.
Vehement touch down motions causes severe impacts on
the rollers, their bearings and shafts. The rubber mounts as
well as the bearings of the rollers might break.
Cushion the touch down
motion.
Very uneven material
surface.
The nature of the material surface can considerably influence the wearing of the sensor.
Pos: 115 /Schweissnaht/Gerä te/SND40/10 Wa rtung/Programmstatus / Betriebszustand @ 0\mod_1131547522265_501.do cx @ 923 @ 2 @ 1