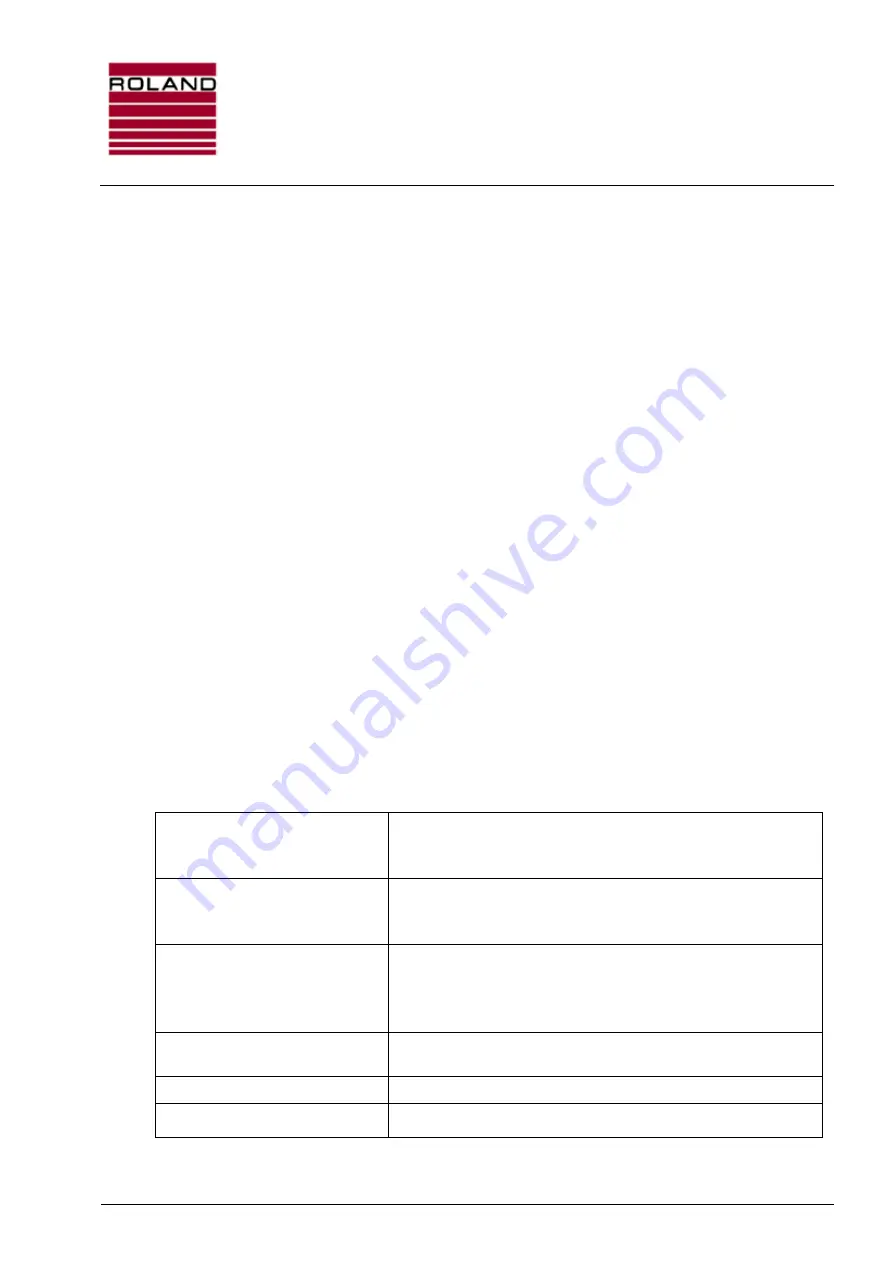
Manual
Weld Seam Detection System R4000 SND40
for Tubes, Cans and Drums
B0059001 / Rev. 2.3
System description
ROLAND ELECTRONIC GmbH · Otto-Maurer-Str. 17 · DE 75210 Keltern · Phone +49 (0)7236-9392-0 · Fax +49 (0)7236-9392-33
25
2.7
Measures for improvement of Weld Seam Detection
2.7.1.1 Process tubes with constant quality
Tubes from different batches, production lines and suppliers may have different seam
characteristics. If problems occur it is advisable to make the decision only to use tubes from one
manufacturer who have a proven process stability. See table in chapter 2.7.6.
2.7.1.2 Alternate Program
If a seam cannot be detected with enough certainty, a second test with an alternate program
should be possible.
2.7.1.3 Multiple locations
The seam characteristic may change with the position on the tube. An actuator can be used to
move the sensor to a 2nd location and to do a second test.
2.7.1.4 Sort out
If a seam cannot be detected with enough certainty, the tube must be sorted out in order to avoid
the processing of wrongly positioned seams! (Eventually after a test with an alternative program on
2
nd
location.)
2.7.1.5 Factors that influence the Weld Seam Characteristic and the Detectability of Weld Seams of
tubes
•
Tube material
•
Tubes forming process, tube coating
•
Welding technology and welding process
•
Drawing process
•
Annealing process
•
Tube handling
•
2.7.2 Measures to improve detectability of Weld Seam
Tube forming process
Adjust for uniform curvature. Do not allow edges
Reduce roller marks
Optimize seam shaving
Welding
Do not change weld additives.
Control welding process for steady width of seam and close
limit of welding heat.
Drawing process
Avoid unnecessary drawing.
Always use same drawing process and same number of
drawing processes.
Do not use outworn drawing tools.
Annealing process
Control process for stability of heat level, heating-up and
cooling phases.
Tube coating
Control process for stability of heat level.
Tube handling
Avoid scratches and dents during handling and transport.