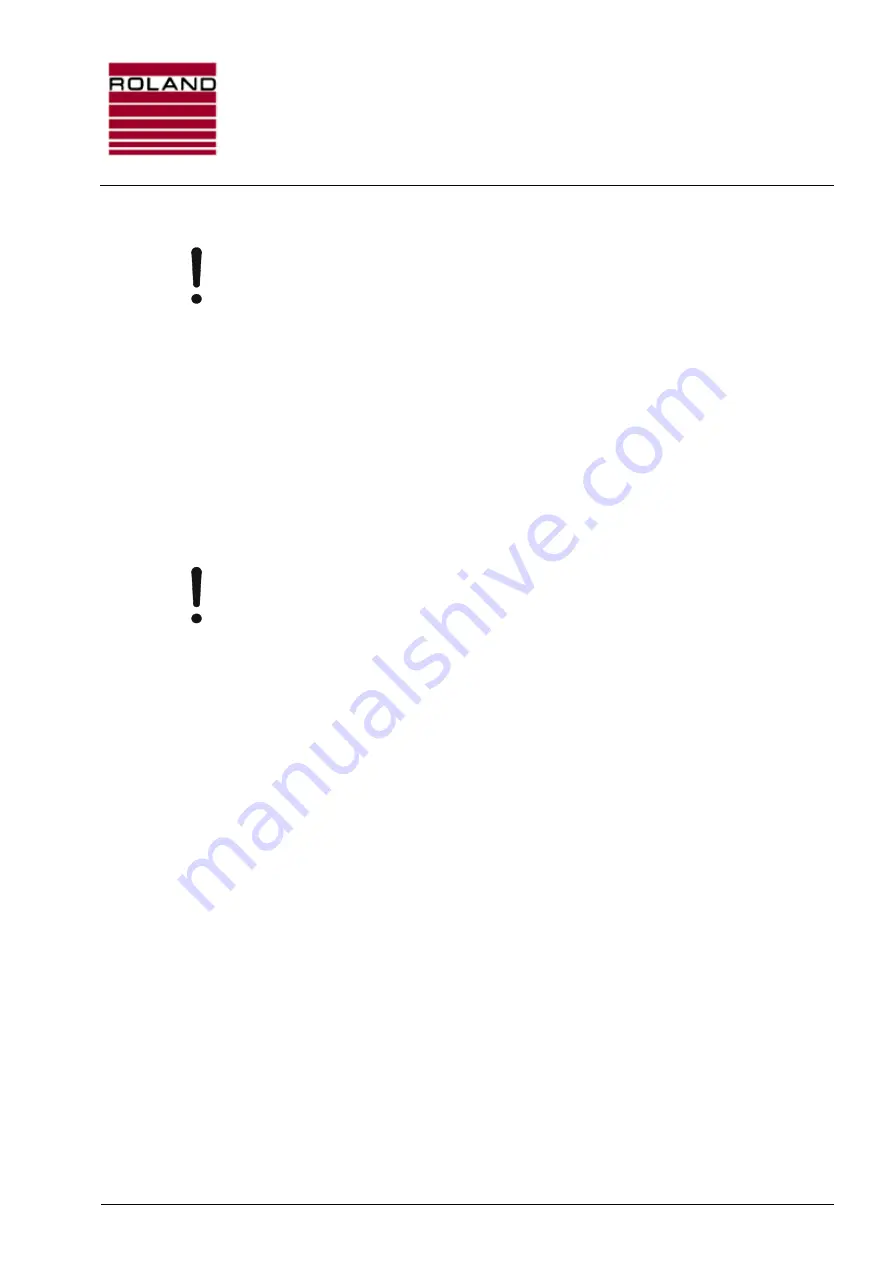
Manual
Weld Seam Detection System R4000 SND40
for Tubes, Cans and Drums
B0059001 / Rev. 2.3
System description
ROLAND ELECTRONIC GmbH · Otto-Maurer-Str. 17 · DE 75210 Keltern · Phone +49 (0)7236-9392-0 · Fax +49 (0)7236-9392-33
21
2.4.4 The clamping device for the tube
Important:
Ensure that the tube is not twisted before lifting the sensor
Possible reasons are:
•
the tube is mechanically pre-tensioned
•
a residual adhesive force which causes the tube to stick to the sensor when it is withdrawn
For drives with a chuck and tapered rollers a brake to stop the tube from turning while the sensor is
withdrawn is normally sufficient.
When the tube is placed on friction roller drive, a separate clamping device is only preventable if
the unloading device grips the tube safely before the sensor is lifted.
2.4.5 The unloading device for the tube
Special attention should be paid to the twist-safe grip and transport of the tube. Reason: The
achieved positioning accuracy at the measuring point is required at the processing station. A poorly
designed transporter device causes angular errors of more than 90 °.
Important:
Comply to positioning accuracy over the entire transportation
2.4.6 Notes on applying eddy current sensors
If the results of the specimen analysis stipulate the use of an Eddy current sensor rather than a
magnetic flux sensor, please note the following:
•
the distance of the eddy current sensor to the tube surface must be kept constant, for example
by using a roller support
•
the placement for a leakage flux - or combined sensor should be planned in a way to permit
easy retrofitting in case of changed tube material
•
if measured from the inside, no magnetic material is allowed to be present at the measuring
point on the outer skin of the tube - exceptions may be clarified with the application laboratory