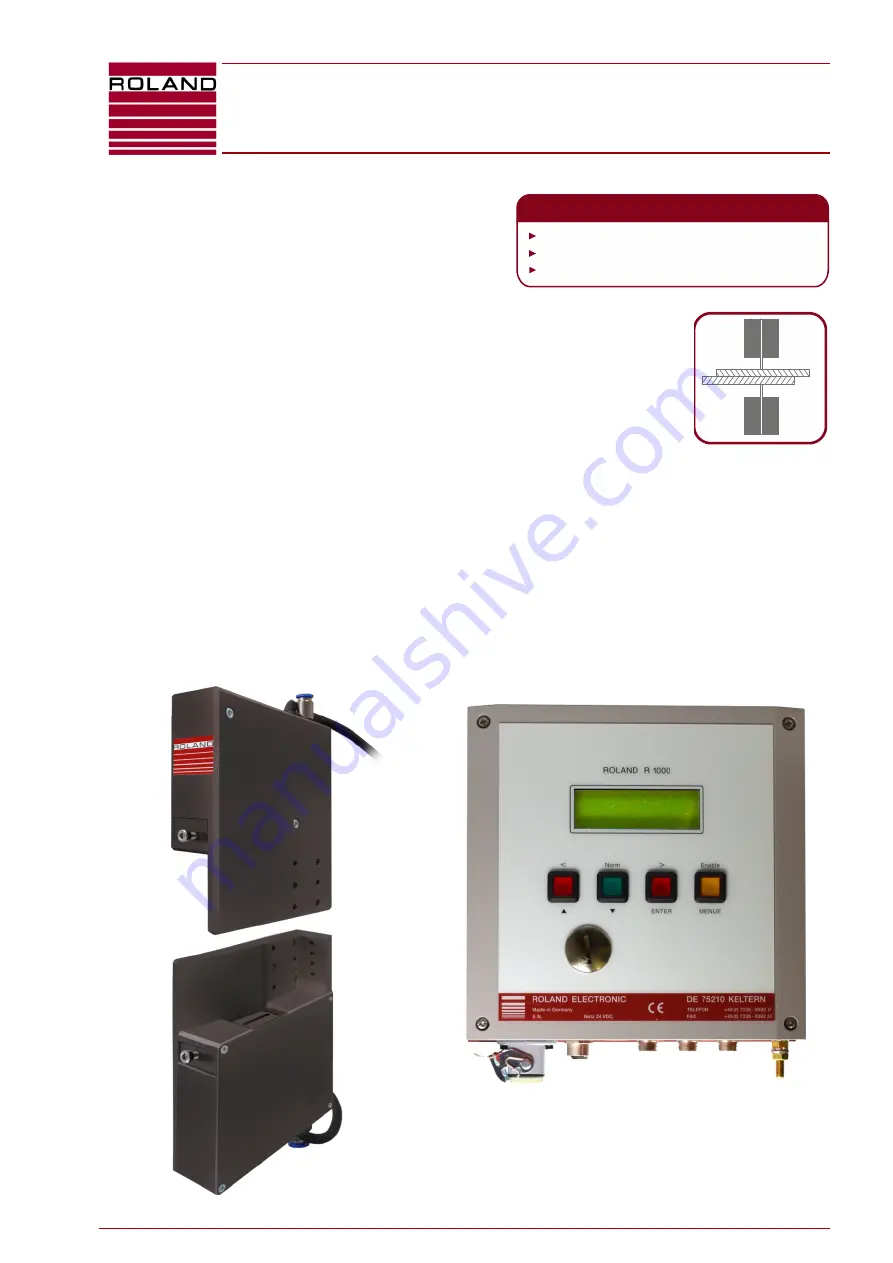
Manual
Double Sheet Control System R1000-Series L20
with integrated fieldbus interface
Double Sheet Control-System
L20
Dual Head Double Sheet Control System
for Metals and Non-ferrous metals
Laser based Function principle
Thickness Control from 0.3 to 15 mm
►
Up to 3 pairs of sensors can be connected to the control unit (3 channel version)
►
Suitable for magnetic feeder systems without velocity limitation
►
Absolute measuring method
►
Digital display of sheet thickness and operational parameters
►
Monitoring of over-gauge and under-gauge limit
►
Integrated fieldbus interface with process and parameter interface
THE ROLAND PLUS:
All common Fieldbus standards
Maintenance-free
For composite materials also