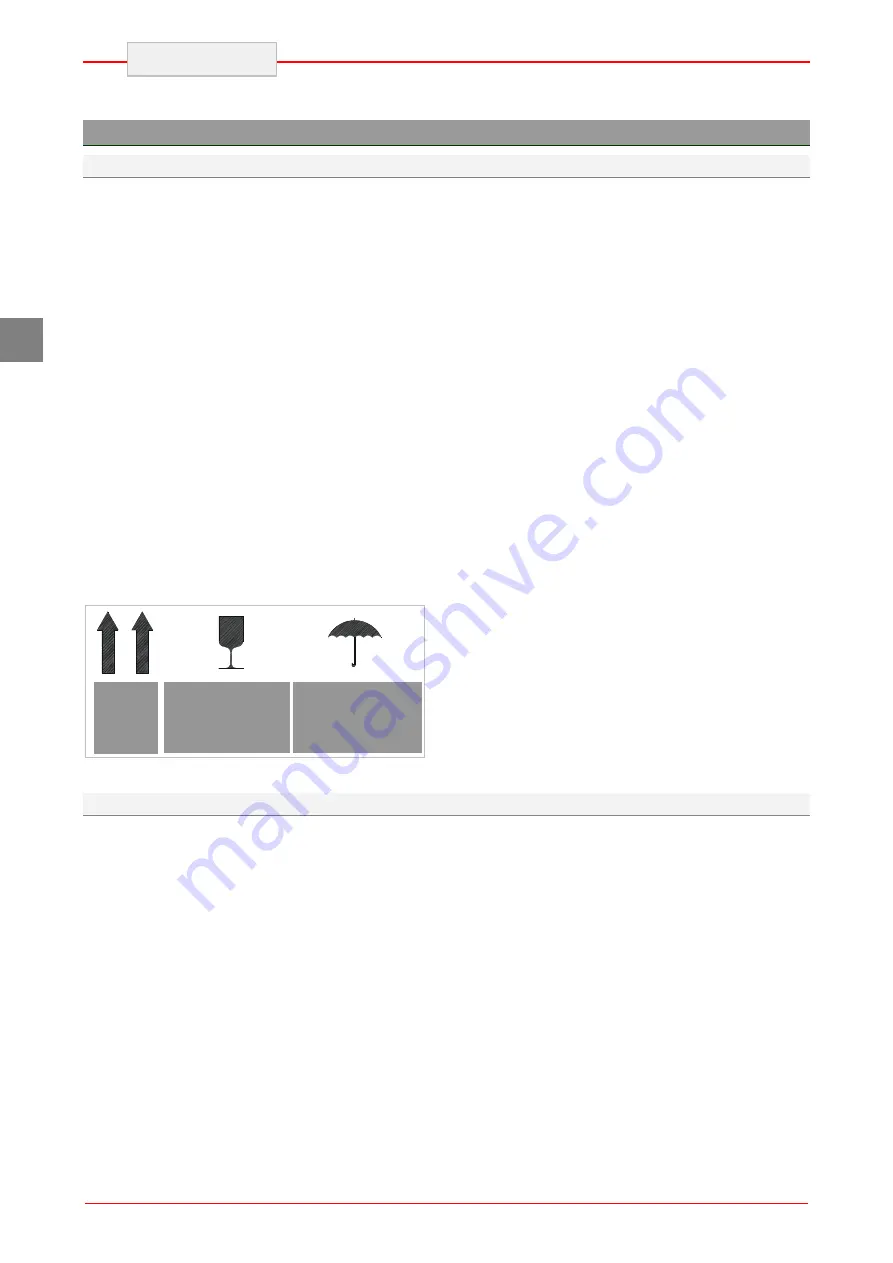
50
ENGLISH
GB
8. INSTALLATION
8.1.
Packaging And Unpacking
Handle and install the appliance respecting the
information provided by the manufacturer, shown
directly on the packaging, on the appliance and in
this manual.
The lifting and transportation system of the
packaged product envisions the use of a fork-lift
truck or a pallet stacker. When using these,
particular attention must be paid to balancing the
weight in order to prevent the risk of overturning
(avoid excessive tilting!).
!
ATTENTION: When inserting the lifting
device, pay attention to the power supply cable
and the position of the feet.
The packaging is made of cardboard and the
pallet of wood. A series of symbols is printed on
the cardboard packaging which highlights, in
accordance with international standards, the
provisions to which the appliances are subjected
during loading, unloading, transport and storage.
On delivery, check that the packaging is intact and
has not undergone any damage during
transportation.
The transportation company must be notified of
any damage immediately.
The appliance must be unpacked as soon as
possible to check that it is intact and undamaged.
Do not cut the cardboard with sharp tools so as
not to damage to the steel panels underneath.
Pull the cardboard packaging upwards.
After having unpacked the appliance, check that
the features correspond to those requested in the
order;
Contact the dealer immediately if there are any
anomalies.
!
Packaging elements (nylon bags,
polystyrene foam, staples …) must not be left
within reach of children.
Remove the protective PVC film from the internal
and external walls, avoiding the use of metal
tools.
8.2. Installation
All the installation phases must be considered,
from the moment of creation of the general plan.
The installation area must be equipped with all
power supply and production residue drainage
connections and must be suitably lit and respect
current laws regarding hygiene and sanitary
requirements.
The performance of the appliance is
guaranteed with a room temperature of 32°C. A
higher temperature can compromise its
performance and, in more serious cases, cause
the appliance’s protections to start up.
Therefore, consider the most critical room
conditions that can be reached in that position
before making a choice.
Level the appliance by acting on the individual
feet.
!
This appliance can only be installed and
operate in rooms which are permanently
ventilated, in order to guarantee correct operation.
Connect and leave for a certain period of
time (at least 2 hours) before checking
functioning. During transport it is probable that the
compressor lubricant oil has entered the
refrigerant circuit blocking the capillary: as a
consequence the appliance will function for a
certain period of time without producing cold until
the oil has returned to the compressor
.
TOP
FRAGILE
HANDLE
WITH CARE
DO NOT EXPOSE
TO HUMIDITY