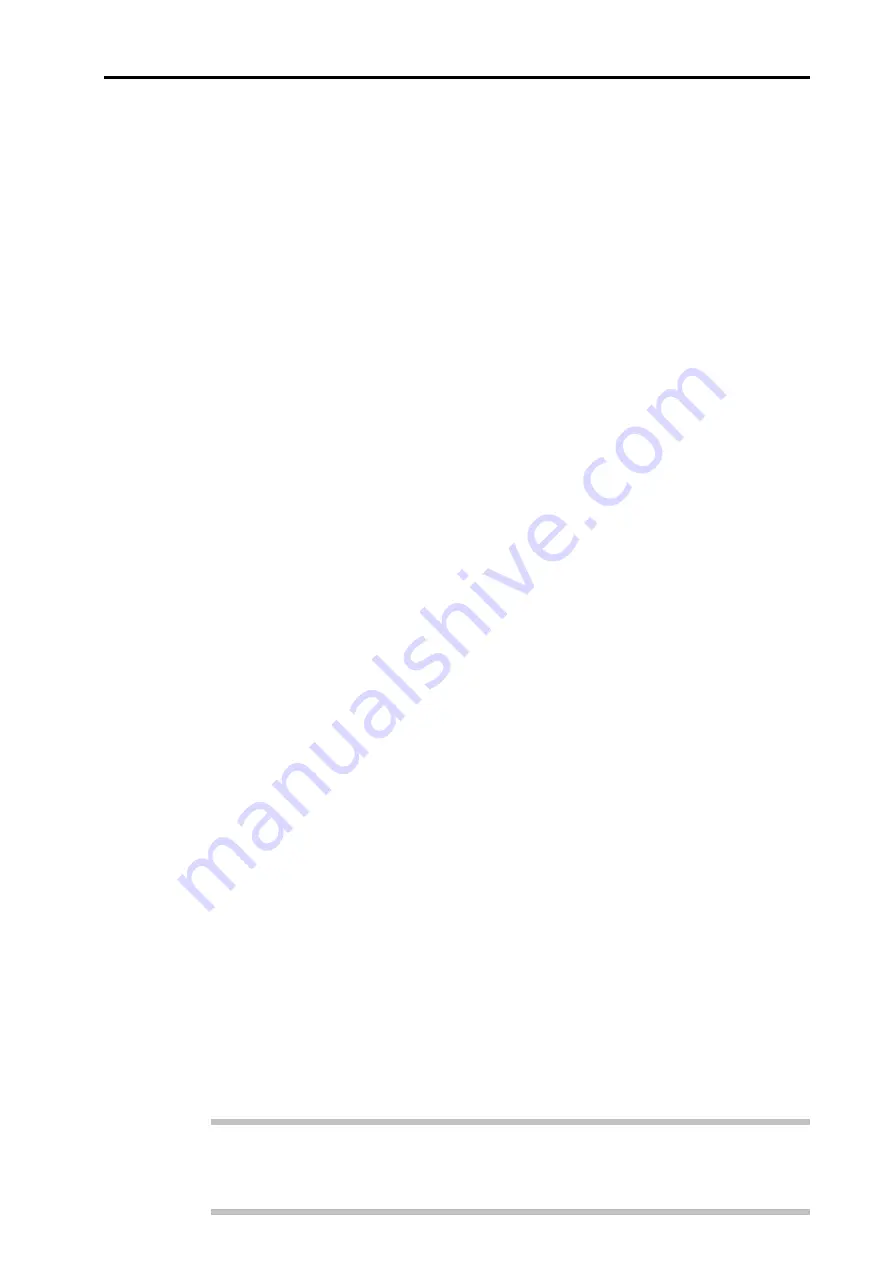
Controller integration
5-11
Open the system
Configuration
and under the
Compensation
tab reverse the
input and/or output settings as required.
Incorrect magnitude
If you are experiencing an incorrect magnitude, you must check the input and output
resolutions:
Using RCU-CS, return the RCU10 to configuration mode.
Open the system
Configuration
and under the
Compensation
tab check the
Resolution
and
Sample Rate
setting in the
Encoder Input
section. Also check the
Resolution
and
Update Rate
setting in the
Output To Controller
section.
5.2.9
Closing the control loop
Once you are satisfied with the direction, resolution and integrity of the feedback signals,
complete the integration by converting all axes concerned to take feedback directly from
the RCU10 system.
With the machine feedrate turned down (<1%), move all axes and ensure that the
machine responds correctly.
Repeat all safety tests described in Section 5.2 to ensure that the machine
responds correctly to all error conditions.
5.2.10 Motor drive tuning
It is often found that, when an encoder and compensation system is installed on to an
existing machine (a retrofit), or a machine that has already had its motors tuned according
to a rotary encoder, then a different tuning set-up is required.
This may happen for two reasons:
The laser encoder or tape scale feedback resolution is much higher than the
existing system’s rotary encoders.
A machine fitted with laser encoders or tape scales has a different mechanical
feedback characteristic to that of a motor rotary encoder. This difference is due to
the fact that an encoder mounted in the machine’s gearbox or on the motor shaft
itself will have very little backlash or lag characteristics. The laser encoder or tape
scale, however, is measuring the real linear machine position that has to be
controlled by the motors through this different mechanical chain.
It will be necessary to tune the motor drives after the integration has taken place,
and it is common to see vibration in axis movement until tuning has been done.
NOTE:
The subject of control loop/motor drive tuning is not a simple one, and is beyond
the scope of this manual. It is recommended that a qualified and experienced engineer,
who is familiar with the type of drive being used, perform the tuning operation.
Summary of Contents for RCU10
Page 1: ...Installation and user s guide M 9904 1122 09 A RCU10 quadrature compensation unit...
Page 11: ...viii Contents This page is intentionally left blank...
Page 23: ...1 12 System overview This page is intentionally left blank...
Page 39: ...2 16 System design...
Page 49: ...3 6 Kit configuration and part identification This page is intentionally left blank...
Page 67: ...4 18 System installation This page is intentionally left blank...
Page 91: ...A 6 RCU10 system specifications This page is intentionally left blank...
Page 147: ...E 8 Commissioning tests This page is intentionally left blank...
Page 175: ...F 28 Extended capability This page is intentionally left blank...
Page 189: ...G 14 Reference This page is intentionally left blank...
Page 193: ...H 4 Test records This page is intentionally left blank Cut here Cut here...
Page 195: ...H 6 Test records This page is intentionally left blank Cut here Cut here...