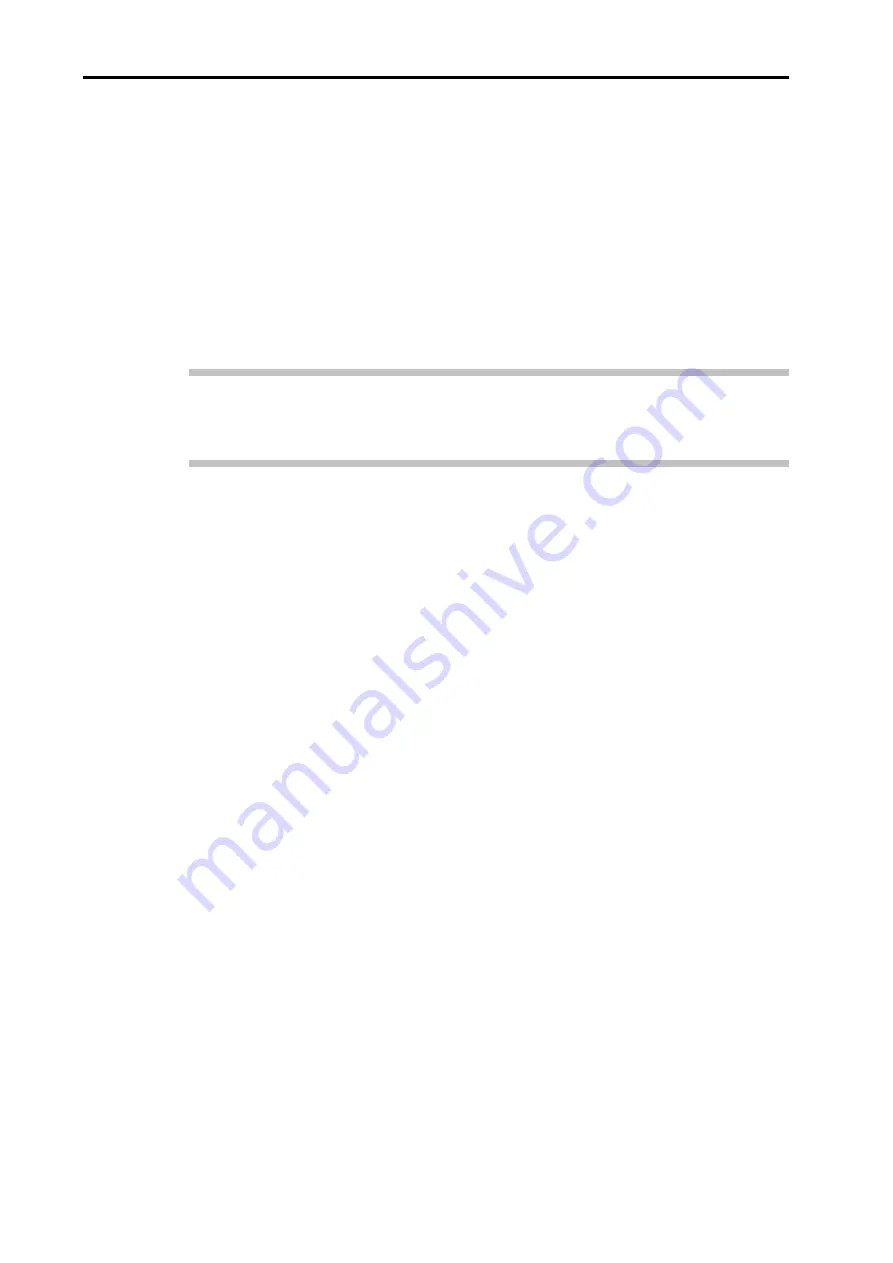
4-6
System installation
4.2.1
System configuration
Select the
System
tab of the system configuration window.
Configure each setting on the
System
tab according to the descriptions shown
below.
Make a note of the pressure sensor serial number and the RCU10 address that it is
connected to before completing the configuration on this page.
When complete, press
Validate Current Tab
to ensure that there are no errors.
NOTE:
Pressing
Cancel
at any time will cause all changes made by the user to be lost.
Pressing
OK
will check the entire configuration for validity before storing it into the
computer's memory.
Machine Description:
May be used to identify the machine to which the RCU10 system
is installed (text field).
Axis Name:
A unique identifier of up to two characters for each axis (e.g. X1).
Axis Length:
The length of the axis (in scale encoder applications the RCU10
checks that the axis position has not exceeded the total length
specified – compensation is not applied to any extra length).
Error Monitoring:
Error Line Only
– standard error mode in which the RCU10
produces an ‘Error’ output for any system error.
Error, Suspend and Warning Lines
– extended error mode in
which the RCU10 produces a three level error output
(Error/Suspend/ Warning) depending on priority (see Appendix
F.1.2 for further details).
Configure
Enables storage of system events/errors for diagnostic
Error Logging:
purposes. It is recommended that this is left at the default setting.
Parameter Tables:
Single
– a single (fixed) set of configuration parameters is
available for each RCU10.
Multiple
– up to four (user I/O – switchable) parameter tables are
available for each RCU10. This is selectable from the drop-down
list. Refer to section F.1.5 for details.
E-Stop:
Enables the compensation buffering enable line on the J7 –
Auxiliary I/O connector. This puts the RCU10 into a state where
position is monitored and the relevant quadrature pitch
conversion is performed, but any required injection (due to
environmental changes) is stored in a buffer. On
disabling
this
line, any stored compensation is introduced into the feedback
path to re-establish position.
Summary of Contents for RCU10
Page 1: ...Installation and user s guide M 9904 1122 09 A RCU10 quadrature compensation unit...
Page 11: ...viii Contents This page is intentionally left blank...
Page 23: ...1 12 System overview This page is intentionally left blank...
Page 39: ...2 16 System design...
Page 49: ...3 6 Kit configuration and part identification This page is intentionally left blank...
Page 67: ...4 18 System installation This page is intentionally left blank...
Page 91: ...A 6 RCU10 system specifications This page is intentionally left blank...
Page 147: ...E 8 Commissioning tests This page is intentionally left blank...
Page 175: ...F 28 Extended capability This page is intentionally left blank...
Page 189: ...G 14 Reference This page is intentionally left blank...
Page 193: ...H 4 Test records This page is intentionally left blank Cut here Cut here...
Page 195: ...H 6 Test records This page is intentionally left blank Cut here Cut here...