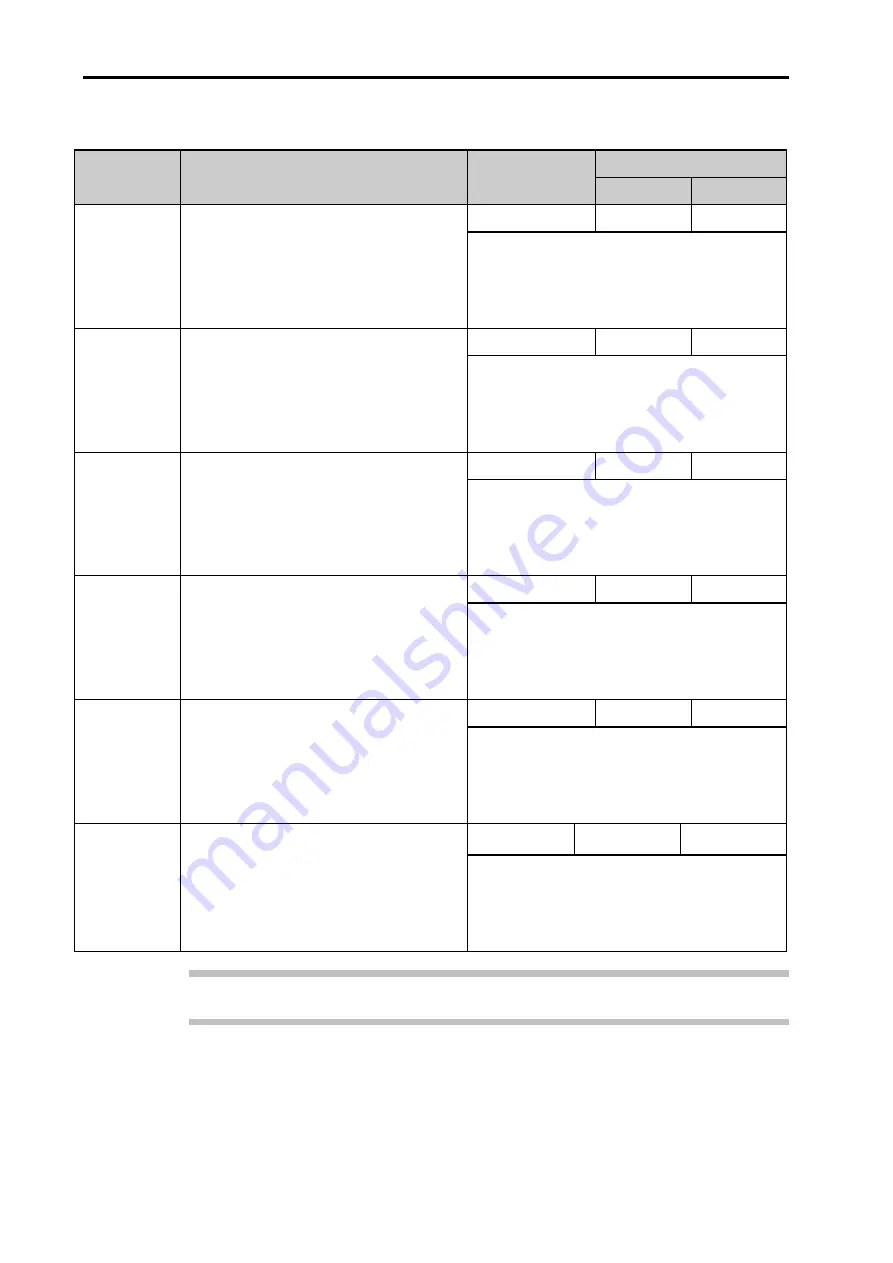
D-22
Compensation system status information and diagnostics
Table D.17 – Axis diagnostics (Sensors tab)
Error
Description
Configuration
mode
Compensation mode
Advanced
Simple
Pressure
Sensor
Failure
Allocated pressure sensor has failed.
WARNING
SUSPEND
ERROR
Check sensor connections.
Check
Sensor
screen for errors.
Check individual sensor errors.
Assert
Reset
line on Auxiliary I/O connector
(Error condition only).
Air Temp
Sensor
Failure
Allocated air temperature sensor has
failed.
WARNING
SUSPEND
ERROR
Check sensor connections.
Check
Sensor
screen for errors.
Check individual sensor errors.
Assert Reset line on Auxiliary I/O connector
(Error condition only).
Workpiece
Sensor
Failure
Allocated material temperature sensor
has failed.
WARNING
SUSPEND
ERROR
Check sensor connections.
Check
Sensor
screen for errors.
Check individual sensor errors.
Assert
Reset
line on Auxiliary I/O connector
(Error condition only).
Structure
Sensor
Failure
Allocated material temperature sensor
has failed.
WARNING
SUSPEND
ERROR
Check sensor connections.
Check
Sensor
screen for errors.
Check individual sensor errors.
Assert
Reset
line on Auxiliary I/O connector
(Error condition only).
Encoder
Sensor
Failure
Allocated material temperature sensor
has failed.
WARNING
SUSPEND
ERROR
Check sensor connections.
Check
Sensor
screen for errors.
Check individual sensor errors.
Assert
Reset
line on Auxiliary I/O connector
(Error condition only).
System
Sensor
Failure
Sensor connected to but not used by
RCU unit under interrogation has failed.
WARNING
WARNING
WARNING
Check sensor connections.
Check
Sensor
screen for errors.
Check individual sensor errors.
Assert
Reset
line on Auxiliary I/O connector
(Error condition only).
Note:
If mode is simple, any rate of change errors are treated as a warning.
Summary of Contents for RCU10
Page 1: ...Installation and user s guide M 9904 1122 09 A RCU10 quadrature compensation unit...
Page 11: ...viii Contents This page is intentionally left blank...
Page 23: ...1 12 System overview This page is intentionally left blank...
Page 39: ...2 16 System design...
Page 49: ...3 6 Kit configuration and part identification This page is intentionally left blank...
Page 67: ...4 18 System installation This page is intentionally left blank...
Page 91: ...A 6 RCU10 system specifications This page is intentionally left blank...
Page 147: ...E 8 Commissioning tests This page is intentionally left blank...
Page 175: ...F 28 Extended capability This page is intentionally left blank...
Page 189: ...G 14 Reference This page is intentionally left blank...
Page 193: ...H 4 Test records This page is intentionally left blank Cut here Cut here...
Page 195: ...H 6 Test records This page is intentionally left blank Cut here Cut here...