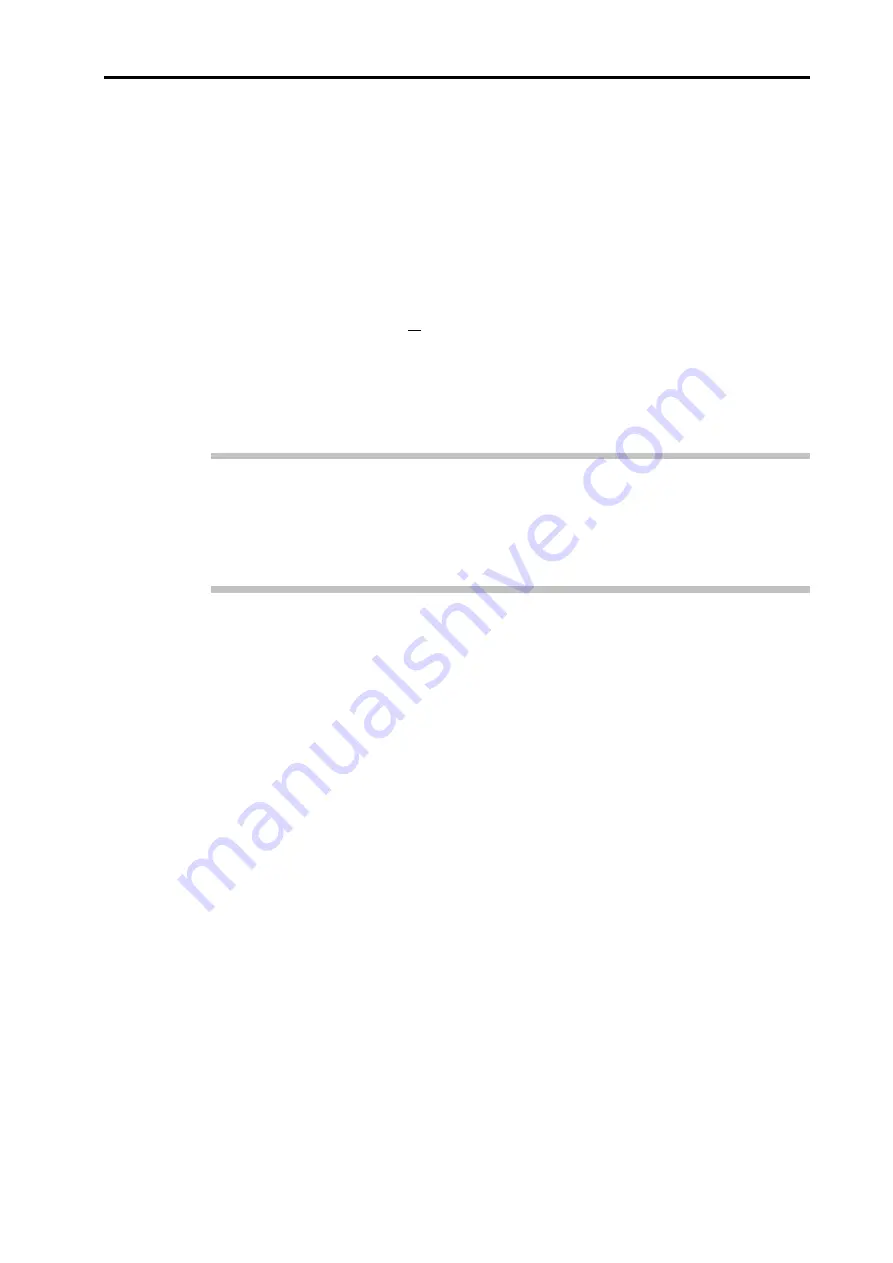
System design
2-9
J8 – PC port
The PC port is used to connect the RCU10 to the RS232 port of a computer. Once
connected, the PC may be used with the Renishaw RCU CS software to both configure
the RCU10 and monitor the RCU10 during operation.
The PC port may be used with either a standard RS232 interface or an RS485 interface.
The RS485 format is used when long distances are required between the RCU10 and the
PC or, in situations where a high level of electrical noise is expected. Connection should
be made to either the RS232 or RS485 as required, but not to both simultaneously.
The PC may be connected using the standard pre-made RS232 cable available in a 1 m
length from Renishaw. Alternatively, custom cables may be made by the user (connector
kits are available). Please see Appendix B for connector pinouts and standard cable
specifications.
Notes:
New PCs are increasingly being supplied with no RS232 ports (ie USB ports
only). Because of the interface problems this presents, Renishaw supplies a
serial-USB adaptor (see section 3.3 for ordering details).
On multi-axis systems only one PC must be connected.
2.4 Velocity/resolution/bandwidth considerations
One of the key considerations in configuring an encoder feedback system is to ensure
that certain frequency dependent parameters are configured correctly.
These parameters are:
Encoder resolution
Maximum required axis velocity
RCU10 input sample rate
RCU10 output resolution
RCU10 output update rate
Controller sample rate
The logical sequence for determining these parameters is as follows:
Summary of Contents for RCU10
Page 1: ...Installation and user s guide M 9904 1122 09 A RCU10 quadrature compensation unit...
Page 11: ...viii Contents This page is intentionally left blank...
Page 23: ...1 12 System overview This page is intentionally left blank...
Page 39: ...2 16 System design...
Page 49: ...3 6 Kit configuration and part identification This page is intentionally left blank...
Page 67: ...4 18 System installation This page is intentionally left blank...
Page 91: ...A 6 RCU10 system specifications This page is intentionally left blank...
Page 147: ...E 8 Commissioning tests This page is intentionally left blank...
Page 175: ...F 28 Extended capability This page is intentionally left blank...
Page 189: ...G 14 Reference This page is intentionally left blank...
Page 193: ...H 4 Test records This page is intentionally left blank Cut here Cut here...
Page 195: ...H 6 Test records This page is intentionally left blank Cut here Cut here...