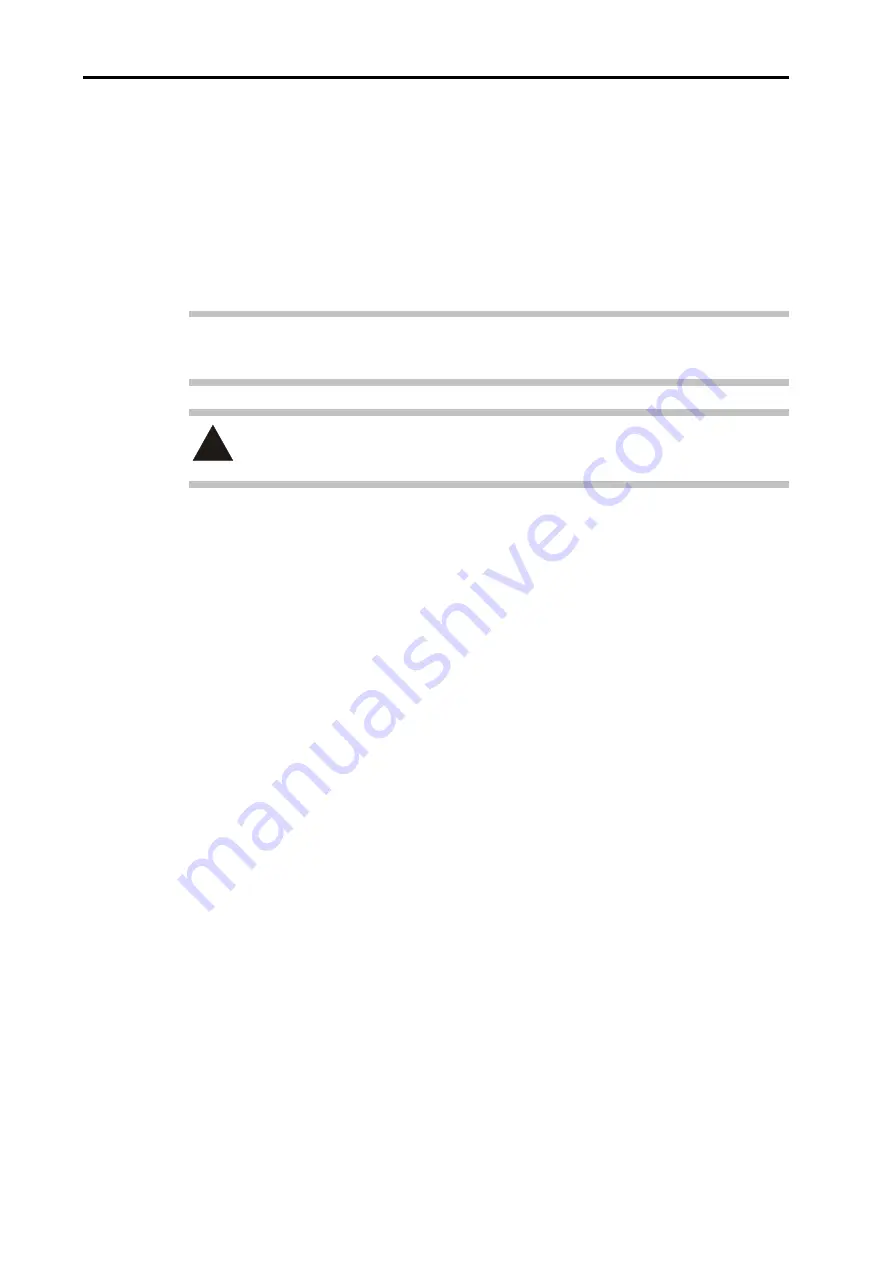
2-6
System design
2.3.2
Connector functions
J1 – 24 V dc power
The RCU10 uses 24 V dc as its power supply. Power supply requirements can be found in
Appendix A. If required, a power supply with a remote sense function can be used. For
connector pinout and hardware installation details please refer to Appendix B.
Note:
When using a network of RCU10s the 24 V supply should be applied
simultaneously for all units.
CAUTION:
The correct power supply voltage is 24 V ± 2 V. Power supplies
outside this range may give unreliable operation.
J2 – Controller output
The controller output connector provides the position feedback signals that pass to the
machine control or counter. These comprise digital A quad B (or analogue sinusoidal)
encoder signals, reference Z pulse and error signals.
The RCU10 can be configured to provide output position data to the machine controller in
either digital incremental A quad B (RS422 differential line driver output) or analogue
incremental sine/cosine format (1 Vpp differential sine and cosine line driver outputs)
using the configuration software. The output resolution of the RCU10 system may be
selected from a number of available options, depending on the encoder input resolution
and output format required.
Renishaw supplies connector kits to assist users in the construction of suitable cables –
please refer to Appendix B for connector pinout and hardware installation details.
J3 – Encoder input
The RCU10 has been designed to accept digital quadrature from three main types of
encoder:
Renishaw RLE10 laser encoder
Renishaw HS10 laser encoder
Generic tape/glass scale
The encoder type is selected through the configuration software, and the encoder input
port must be wired to suit the selected type. Renishaw supplies connector kits to assist
users in the construction of suitable cables – please refer to Appendix B for connector
pinout and hardware installation details.
The tables in section 2.4.2 show the available RCU10 output resolutions for a given
encoder type and input resolution – along with the maximum velocities, as discussed in
section 2.4.
!
Summary of Contents for RCU10
Page 1: ...Installation and user s guide M 9904 1122 09 A RCU10 quadrature compensation unit...
Page 11: ...viii Contents This page is intentionally left blank...
Page 23: ...1 12 System overview This page is intentionally left blank...
Page 39: ...2 16 System design...
Page 49: ...3 6 Kit configuration and part identification This page is intentionally left blank...
Page 67: ...4 18 System installation This page is intentionally left blank...
Page 91: ...A 6 RCU10 system specifications This page is intentionally left blank...
Page 147: ...E 8 Commissioning tests This page is intentionally left blank...
Page 175: ...F 28 Extended capability This page is intentionally left blank...
Page 189: ...G 14 Reference This page is intentionally left blank...
Page 193: ...H 4 Test records This page is intentionally left blank Cut here Cut here...
Page 195: ...H 6 Test records This page is intentionally left blank Cut here Cut here...