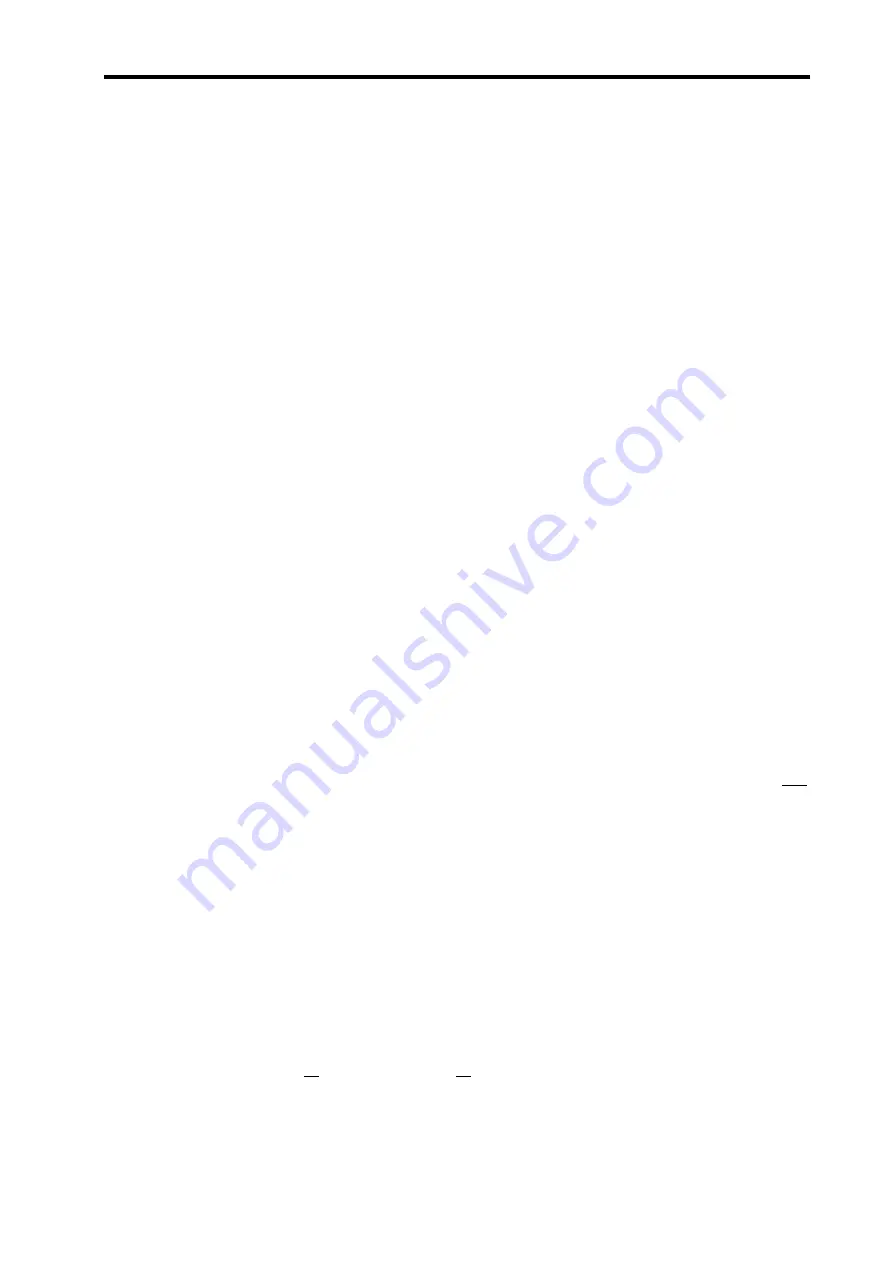
Extended capability
F-9
F.1.7.2 Operating with multiple parameter tables
Two of the commonest applications are shown below:
Using parameter tables to change material type
In the case where workpiece expansion compensation is being used and different
materials are regularly worked on the same machine, it may be necessary to change the
thermal expansion coefficient.
In this case the parameters for each axis would be configured identically. Different
material expansion coefficients would be used in each parameter table.
This may be configured as follows.
1. Make the wiring to the parameter table selection lines (Auxiliary I/O connector)
common to each axis. This makes all axes change together.
2. On the
System
tab of the
Configuration
window, select
Multiple
parameter tables.
Determine how many material types are to be used, and set the number of parameter
tables to this number (one for each material type).
3. Go to the
Parameters
tab and enter the required values in each parameter table that
is available. Repeat this for each axis. In this case
Expansion coefficient <1>
will be
set for one material and
Expansion coefficient <2>
will be set for another, etc.
4. In operation, the appropriate material type may be selected prior to homing the
machine by using the parameter selection control lines. These may be given M-codes
in the machine controller.
Using a machine with multiple home positions or zones
In this case, the use of the parameter tables is a little more complicated, as each axis and
each parameter table will contain differing values.
Consider the case where a machine has multiple home positions. For each home
position, the relevant axes could have different values for :
Air dead path (or scale offset)
(If laser encoders are used)
Workpiece temperature sensor
(If a different sensor is required for each zone)
Workpiece expansion coefficient
(If each zone is used for different materials)
Workpiece origin offset
(If a fixed offset from home is being used)
Workpiece origin type
(To select fixed offset or by logic)
In this case only those axes which are to have the multiple home/zones will need to be
switched, but all parameter tables in all axes must have valid data entered.
Summary of Contents for RCU10
Page 1: ...Installation and user s guide M 9904 1122 09 A RCU10 quadrature compensation unit...
Page 11: ...viii Contents This page is intentionally left blank...
Page 23: ...1 12 System overview This page is intentionally left blank...
Page 39: ...2 16 System design...
Page 49: ...3 6 Kit configuration and part identification This page is intentionally left blank...
Page 67: ...4 18 System installation This page is intentionally left blank...
Page 91: ...A 6 RCU10 system specifications This page is intentionally left blank...
Page 147: ...E 8 Commissioning tests This page is intentionally left blank...
Page 175: ...F 28 Extended capability This page is intentionally left blank...
Page 189: ...G 14 Reference This page is intentionally left blank...
Page 193: ...H 4 Test records This page is intentionally left blank Cut here Cut here...
Page 195: ...H 6 Test records This page is intentionally left blank Cut here Cut here...