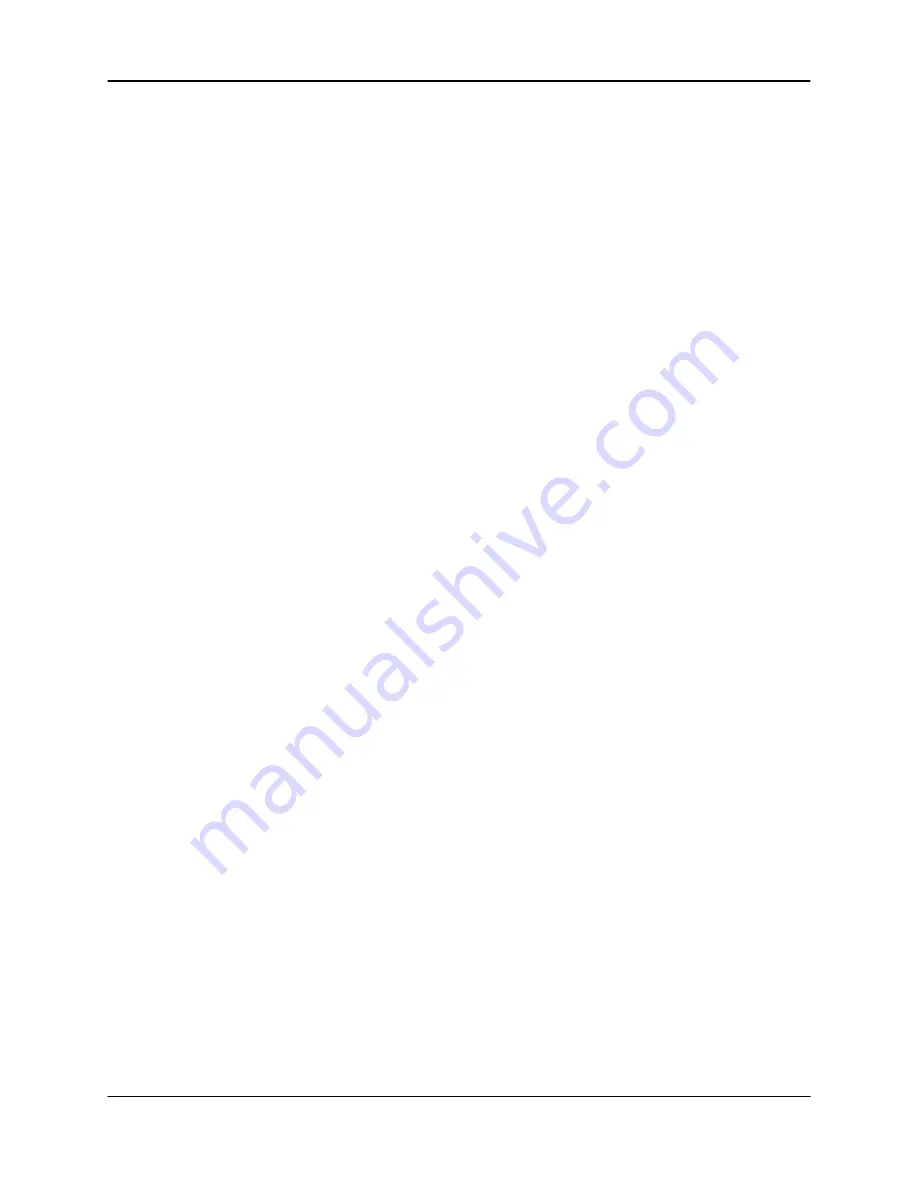
Pressure Systems, Inc. Model 9116 User’s Manual
Page 122
www.PressureSystems.com
If the
ping
test of the host computer’s IP passed, while the
ping
of the
Model 9116
module
failed, check the following possible sources for error:
●
Ensure
the
Model 9116
module’s IP has been assigned (as explained in
Section
6.1.2.1
) and that the correct IP was used for the
ping
test.
●
Ensure the IP address of the host computer and the
Model 9116
module are not
duplicated on the network.
●
Ensure the link LEDs are active on the scanner and the Ethernet hub or switch to
which it is attached. Also ensure the link LEDs are active on the host computer’s
Ethernet adapter and the hub or switch to which it is attached.
●
Ensure the Ethernet adapter card installed in the host is properly configured without
conflict. In Windows
®
95 this can be verified by entering the
CONTROL
PANEL
under
SETTINGS
. Under
CONTROL PANEL,
select the
SYSTEM
icon. When the
DEVICE MANAGER
tab is selected, a list of all installed hardware devices will be
displayed. Any possible hardware conflicts will be marked in this list with a yellow
warning symbol next to the device in question.
●
Ensure the Ethernet adapter is configured for 10 Mbit/Sec. Many adapters are
capable of higher speeds that are not compatible with the
Model 9116
modules.
6.2
Zero and Gain Calibration Troubleshooting
Incorrect pneumatic setup or incorrect command usage when executing a module’s Re-zero or
Span calibration command (see
‘Z’
,
‘h’
, and
‘C’
commands in
Chapter 3
) can result in
unexpected module operation. A common source of errors during these operations is incorrect
control of the module’s internal calibration valve and pneumatic inputs.
Pressure connections are described in
Chapter 2
while details of calibration procedures are
described throughout
Chapter 4
. Some common errors and problems are listed below. These
common problems apply primarily to
Model 9116
with its internal transducers and calibration
manifold.
●
The
module’s
supply air
input is either not attached or does not provide enough
pressure (less than 65 psig) to shift the calibration valve. This results in the
calibration valve remaining in its current position even though module commands
have requested movement of the valve.
●
The module’s calibration valve is not placed in the correct position before executing
the Span calibration command (
Calculate & Set Gain
). This command will not
automatically shift the valve to the CAL position before taking data (as the Re-zero
calibration command does). The user must manually control the calibration valve
position using the
Set Operating Options
(
‘w’
) command if the
CAL
and
CAL REF
inputs are to be used.