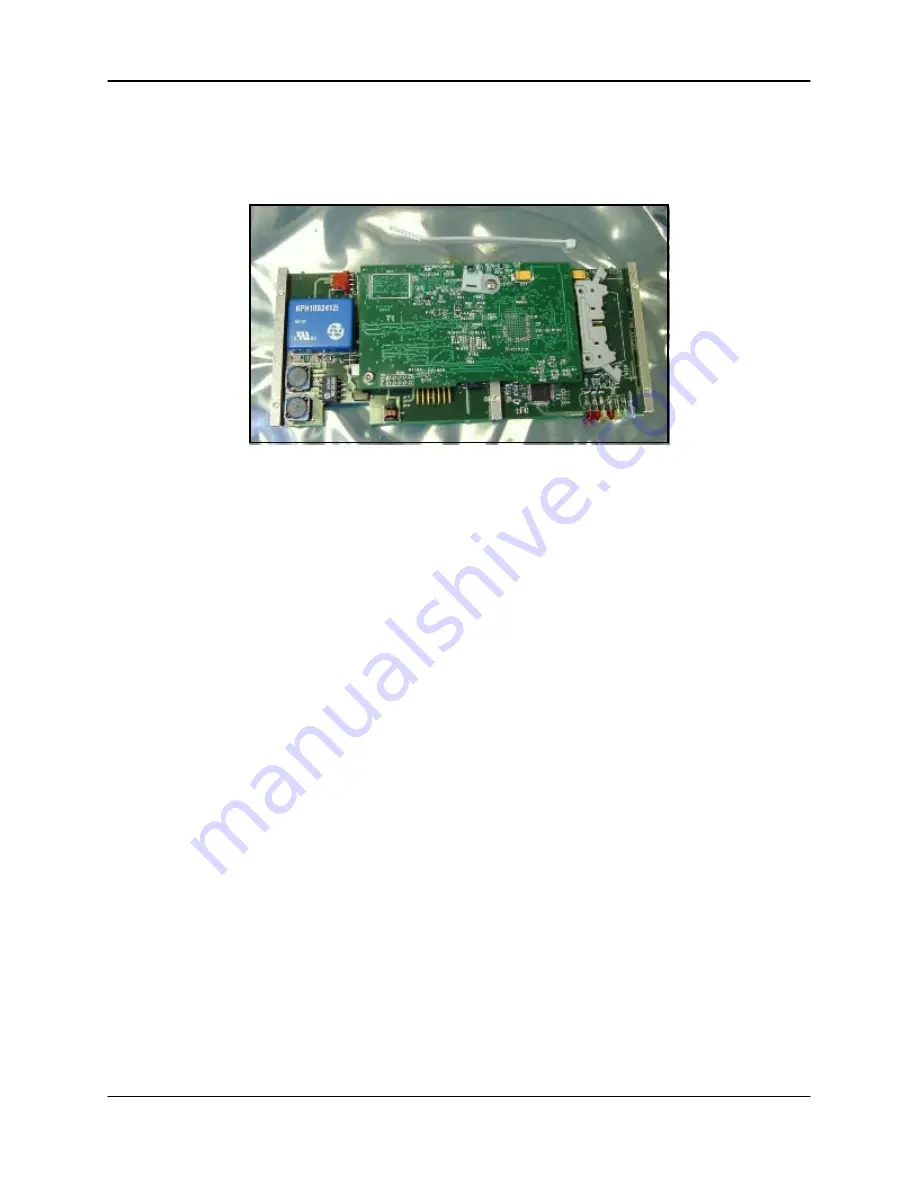
Pressure Systems, Inc. Model 9116 User’s Manual
Page 107
www.PressureSystems.com
(3) Remove the three (3) 2-56 Phillips head screws securing the PC-322/323
assembly mounting brackets to the top plate. These screws will be in line with the
PC-322/323 LEDs that protrude through the top plate. Carefully lift the board out
of the top panel. Remove the wiring harness from P1. See
Figure 5.3
.
Figure 5.3
PC-322/323 Assembly
(4) Install the wiring harness from the circular connector attached to the top plate onto P1 on
the new PC-322/323 assembly.
(5) Place the new PC-322/323 assembly so that its connectors and LEDs protrude through the
top panel, dressing the wiring harness from P1 so that no more than one layer of the
harness will be trapped between the board assembly and the valve assembly.
Loosely
install the three (3) 2-56 screws to secure the PC-322/323 assembly mounting brackets to
the top panel. (To ease reassembly, they will be tightened after installing the electronics
back into the module case.)
(6) Reinstall any previously installed wiring harnesses on connectors P3 and P6 of the PC-
322/323 assembly .
Ensure proper pin 1 orientation when installing these connectors
.
(Pin 1 of the ribbon cable has a red stripe while pin one of P1 will contain a square
solder pad on the PC-327.)
(7) Install the wiring harnesses so they are dressed away from, and will not be pinched or
punctured when the alignment posts enter the holes in the assembly mounting brackets.
Install the module electronics into the extrusion case, ensuring the alignment posts in the
module’s bottom panel align with the holes in the PC-322/323 assembly mounting brackets.
Ensure that there are no conductors from the P1 harness pinched between the top plate
and the extrusion. Ensure that the top plate gasket is properly installed. Install the screws
that secure the top panel to the housing. Tighten the three (3) screws attached to the PC-
322/323 assembly mounting brackets.
(8) Test your scanner to ensure proper operation.