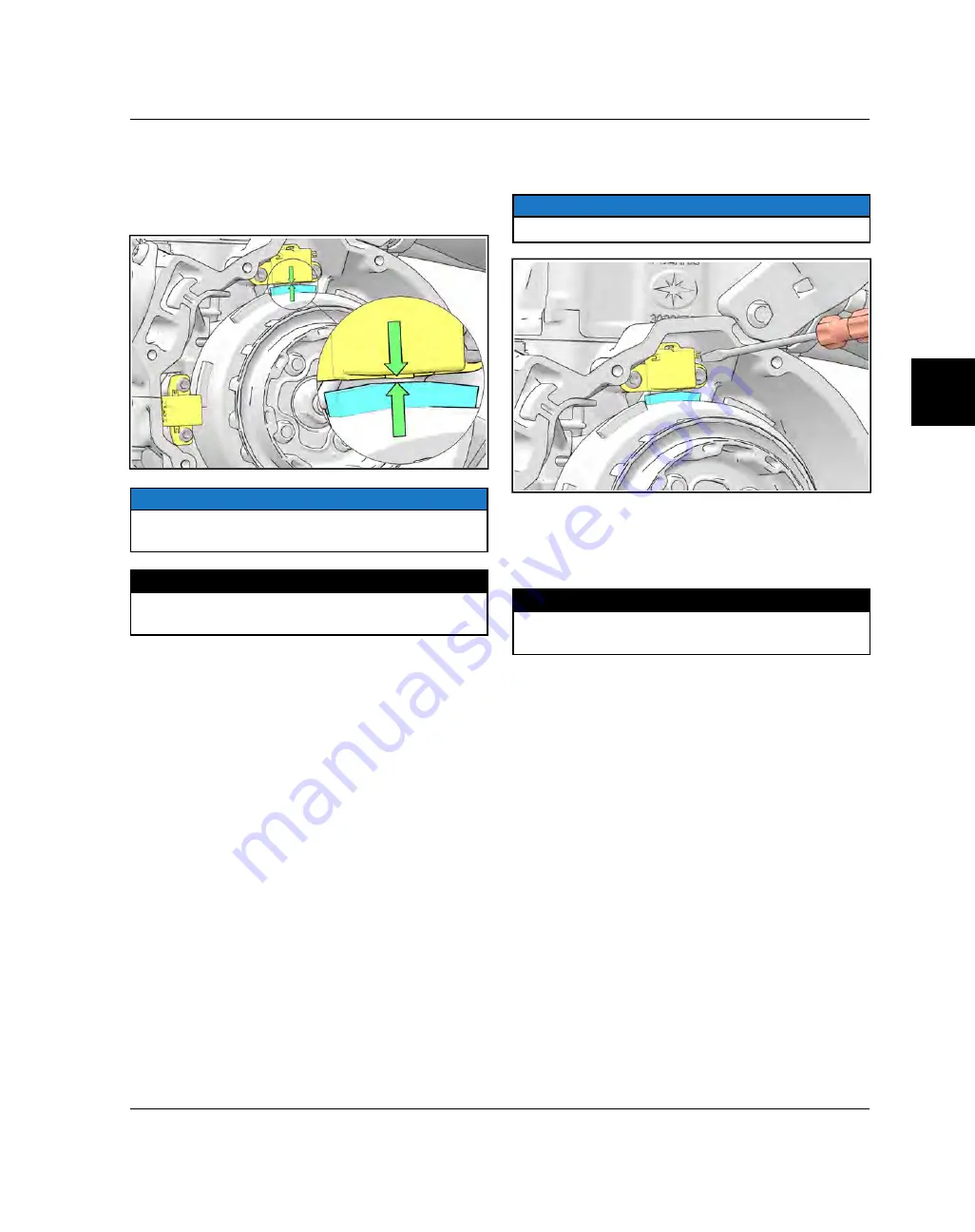
9850060 R02 - 2020-2021 850 AXYS™ Long Track Snowmobile Service Manual
© Copyright Polaris Inc.
4.9
CRANKSHAFT POSITION SENSOR AIR
GAPS
Hard engine starting, erratic reverse operation, and poor
engine performance can occur if the CPS air gap(s) are
outside specification.
NOTICE
The sensor bases are not slotted. Only minor deflection
adjustments can be made.
MEASUREMENT
Crankshaft Position Sensor Air Gap:
.020 - .030 in (0.5 - 0.8 mm)
AIR GAP INSPECTION/ADJUSTMENT
1. Rotate the crankshaft/flywheel so that an encoder rib
is positioned directly underneath the sensor being
measured.
2. Insert the blade of a .030" feeler gauge between the
rib and sensor face. If there is no drag felt on the
feeler gauge, the CPS must be adjusted.
3. To adjust a CPS, use an 8 inch pry bar to carefully
deflect the sensor.
4. Place the tip of the small pry bar between the back of
the sensor and crankcase. insert a .012" feeler gauge
between the sensor face and encoder rib.
NOTICE
Do not pry on the individual sensor wires.
5. Gently pry the sensor toward the encoder rip until the
gauge begins to bind between the components.
6. Re-measure the air gap. The gap should be between
the specification listed below.
MEASUREMENT
Crankshaft Position Sensor Air Gap:
.020 - .030 in (0.5 - 0.8 mm)
Summary of Contents for 850 PRO-RMK 155 2.6" QD 2021
Page 6: ......
Page 738: ......
Page 739: ......
Page 741: ...850 Long Track Jumper Console Switches 2413927 ...