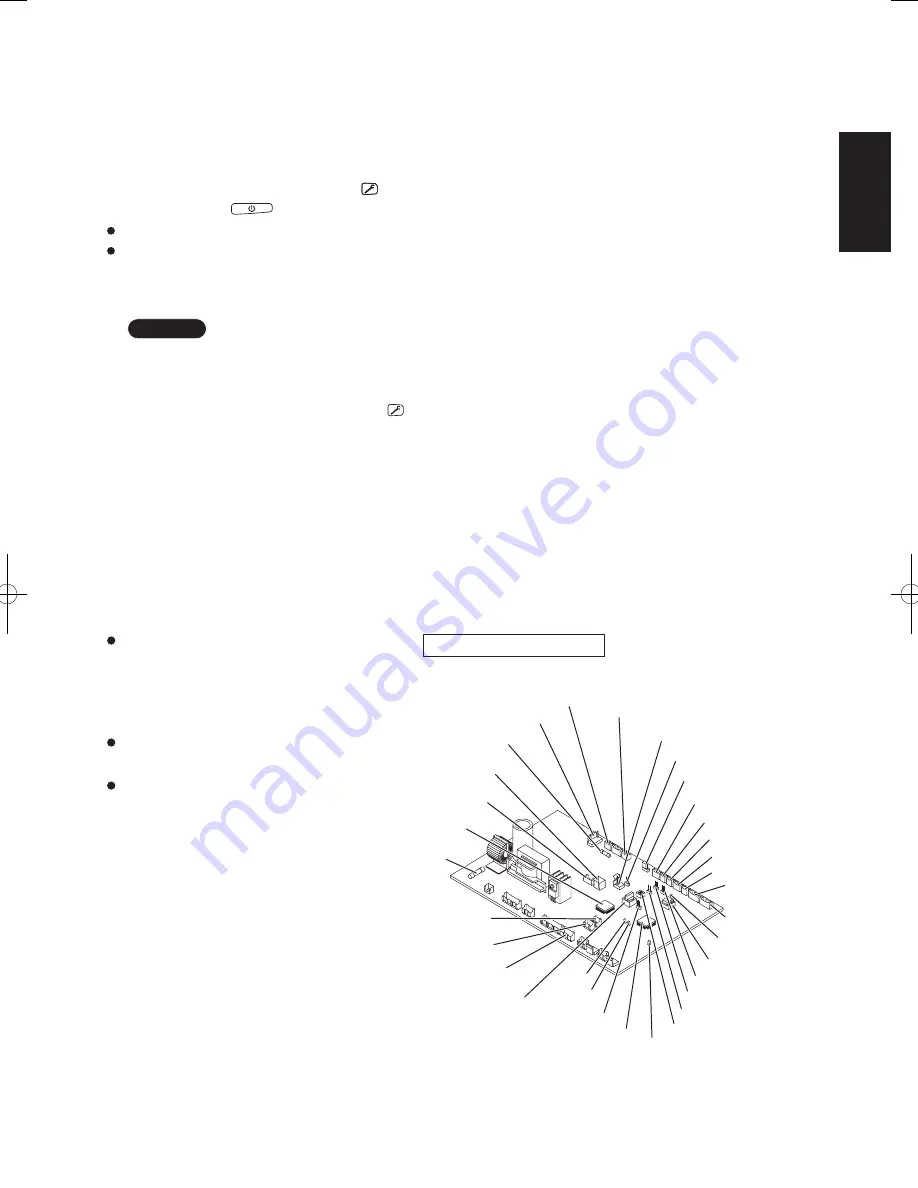
2
2
2-3
2-4. Items to Check Before the Test Run
(1) Turn the remote power switch ON at least 12 hours in advance in order to energize the crankcase heater.
(2)
(2)
Fully open the closed valves on the liquid-tube and gas-tube sides.
2-5. Test Run Using the Remote Controller
(1) Press and hold the remote controller
button for 4 seconds or longer.
Then press the
button.
“TEST” appears in the LCD display during the test run.
Temperature control is not possible when test run mode is engaged.
(This mode places a large load on the devices. Use it only when performing the test run.)
Use either Heating or Cooling mode to perform the test run.
The outdoor unit will not operate for approximately 3 minutes
after the power is turned ON or after it stops operating.
(3) If normal operation is not possible, a code appears on the remote controller LCD display.
Refer to “2-7. Table of Self-Diagnostic Functions and Corrections”, and correct the problem.
After the test run is completed, press the
(4)
button again.
Check that “TEST” disappears from the LCD display.
(This remote controller includes a function that cancels test run mode after a 60-minute timer has elapsed,
in order to prevent continuous test run operation.)
(5) For the test run of an inverter outdoor unit, operate the compressors for a minimum of 10 minutes
(in order to check for open phase).
* When performing a test run using a wired remote controller, operation is possible without attaching the
cassette-type ceiling panel. (“P09” will not be displayed.)
2-6. Precautions
Request that the customer be present
when the test run is performed.
At this time, explain the operation manual
and have the customer perform the actual
steps.
Be sure to pass the manuals and warranty
certificate to the customer.
Check that the 220 – 240 V AC power is
not connected to the inter-unit control
wiring connector terminal.
* If 220 – 240 V AC is accidentally applied,
the indoor or outdoor unit control PCB
fuse will blow in order to protect the PCB.
Correct the wiring connections, then
disconnect the 2P connectors that are
connected to the PCB, and replace them
with 2P connectors.
If operation is still not possible after
changing the brown connectors,
try cutting the varistor.
(Be sure to turn the power OFF before
performing this work.)
Fig. 2-4
NOTE
Outdoor unit control PCB
8 – 10 HP
LED1
FUSE (0.5A, F500)
OC (CN500, BLU)
MOV2
(CN301, BLK)
MOV1
(CN300, WHT)
EMG (CN502, BRN)
SILENT (CN037, WHT)
PUMP DOWN (CN048)
TEMINAL (CN205, BLK)
R.C.ADD. Rotary switch
C2 (CN020, WHT)
C1 (CN021, WHT)
TEST (CN033, RED)
TD (CN024, BLK)
TO (CN023, BLK)
TS (CN022, RED)
63PH (CN027, WHT)
EXCT
(CN030, RED)
RC P
(CN039, RED)
IC002
CTL2
(CN202, GRN)
CTL1
(CN203, GRN)
FUSE
(6.3A, F101)
N . P . C H E C K
(CN046, RED)
LED2
MODE (CN038)
D115
(POWER LED)
IC001
R.C.ADD. DIP switch
A.ADD (CN047)
C-CHK (CN035)
EEPROM
LED (D041
EEPROM LED)
SM830194-04_Single_BigPAC.indb 3
2014/11/04 13:45:13
Summary of Contents for S-200PE1E8
Page 88: ...1 82 MEMO ...
Page 112: ...3 2 3 3 1 Outdoor Units Electric Wiring Diagram U 200PE1E8 U 250PE1E8 ...
Page 113: ...3 3 3 Schematic Diagram U 200PE1E8 U 250PE1E8 ...
Page 115: ...3 5 3 3 2 Indoor Units High Static Pressure Ducted Type S 200PE1E8A Electric Wiring Diagram ...
Page 116: ...3 6 3 3 2 Indoor Units High Static Pressure Ducted Type S 200PE1E8A Schematic Diagram ...
Page 117: ...3 7 3 3 2 Indoor Units High Static Pressure Ducted Type S 200PE1E8 Electric Wiring Diagram ...
Page 118: ...3 8 3 3 2 Indoor Units High Static Pressure Ducted Type S 200PE1E8 Schematic Diagram ...
Page 119: ...3 9 3 3 2 Indoor Units High Static Pressure Ducted Type S 250PE1E8 Electric Wiring Diagram ...
Page 120: ...3 10 3 3 2 Indoor Units High Static Pressure Ducted Type S 250PE1E8 Schematic Diagram ...
Page 129: ...4 9 4 4 3 Outdoor Unit Filter PCB FIL C906VH8 ...
Page 130: ...4 10 4 4 4 Outdoor Unit HIC Board HIC C906VH8 ...
Page 136: ... MEMO 4 16 ...
Page 154: ... MEMO 5 18 ...
Page 164: ... MEMO 6 10 ...
Page 180: ... MEMO 7 16 ...
Page 197: ...201411 ...