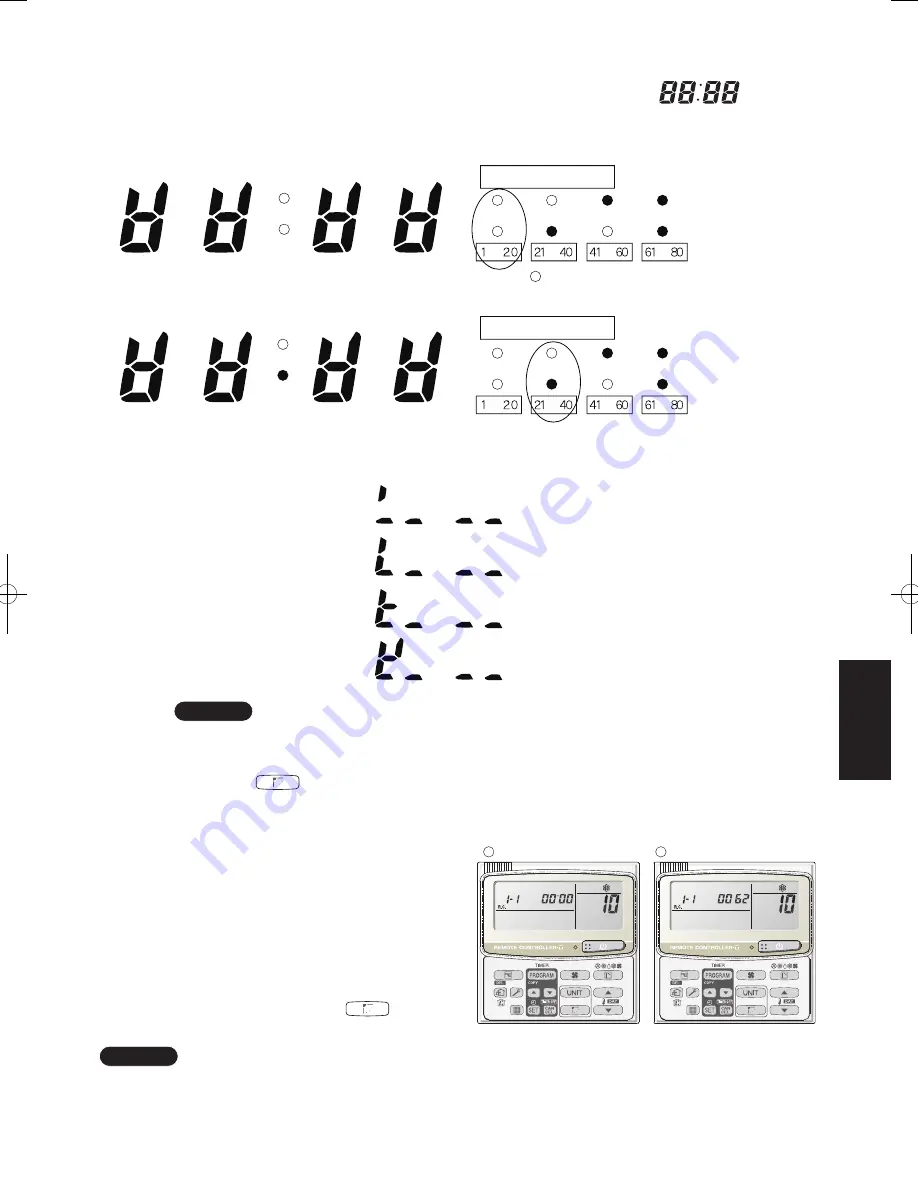
6-5
6
6
—
—
—
—
—
—
—
—
1
2
7
12
17
3
13
18
8
4
14
19
9
5
10
15
20
6
11
16
21
22
27
32
37
23
33
38
28
24
34
39
29
25
30
35
40
26
31
36
*2:
7-segment, 4-digit display for remote controller timer display
The connected unit Nos. are displayed as shown below, using the 7-segment 4-digit (
) display and
the colon.
NOTE
The colon display (Unit Nos. 1 – 20, 21 – 40) changes automatically every 10 seconds.
(The display does not change if higher unit numbers do not exist.)
Pressing the
button switches the display immediately to the next higher level, even if 10 seconds
have not passed.
(A) and (B) are displayed alternately.
B
A
10: <Total compressor operating time>
*3:
The total compressor operating time is displayed
(in 1-hour units) using 8 digits.
• When the first 4 digits are displayed, the top
point of the colon is lit.
• When the last 4 digits are displayed, the colon
points are not lit.
• The display of the first 4 and last 4 digits
changes automatically every 10 seconds. It can
also be changed by pressing the
button.
NOTE
With the outdoor unit maintenance remote controller (when connected to the outdoor unit), the unit remote controller
check functions will not operate.
10: <Total compressor operating time>
(A) and (B) are displayed alternately.
Display for unit Nos. 1 – 20
Display for unit Nos. 21 – 40
The meaning of the colon display changes in the same way, allowing unit Nos. up to 80 to be displayed.
Sample displays of the unit Nos. of connected indoor units
Not lit
Lit
Not lit
Lit
Not lit
Lit
Not lit
Lit
Meaning of display colon
is not displayed.
Meaning of display colon
Not lit
Lit
Not lit
Lit
Not lit
Lit
Not lit
Lit
• Display of unit No. 1
• Display of unit Nos. 1 and 2
• Display of unit Nos. 1, 2, and 3
• Display of unit Nos. 1, 2, 3, and 4
SM830194-04_Single_BigPAC.indb 5
2014/10/31 13:21:22
Summary of Contents for S-200PE1E8
Page 88: ...1 82 MEMO ...
Page 112: ...3 2 3 3 1 Outdoor Units Electric Wiring Diagram U 200PE1E8 U 250PE1E8 ...
Page 113: ...3 3 3 Schematic Diagram U 200PE1E8 U 250PE1E8 ...
Page 115: ...3 5 3 3 2 Indoor Units High Static Pressure Ducted Type S 200PE1E8A Electric Wiring Diagram ...
Page 116: ...3 6 3 3 2 Indoor Units High Static Pressure Ducted Type S 200PE1E8A Schematic Diagram ...
Page 117: ...3 7 3 3 2 Indoor Units High Static Pressure Ducted Type S 200PE1E8 Electric Wiring Diagram ...
Page 118: ...3 8 3 3 2 Indoor Units High Static Pressure Ducted Type S 200PE1E8 Schematic Diagram ...
Page 119: ...3 9 3 3 2 Indoor Units High Static Pressure Ducted Type S 250PE1E8 Electric Wiring Diagram ...
Page 120: ...3 10 3 3 2 Indoor Units High Static Pressure Ducted Type S 250PE1E8 Schematic Diagram ...
Page 129: ...4 9 4 4 3 Outdoor Unit Filter PCB FIL C906VH8 ...
Page 130: ...4 10 4 4 4 Outdoor Unit HIC Board HIC C906VH8 ...
Page 136: ... MEMO 4 16 ...
Page 154: ... MEMO 5 18 ...
Page 164: ... MEMO 6 10 ...
Page 180: ... MEMO 7 16 ...
Page 197: ...201411 ...