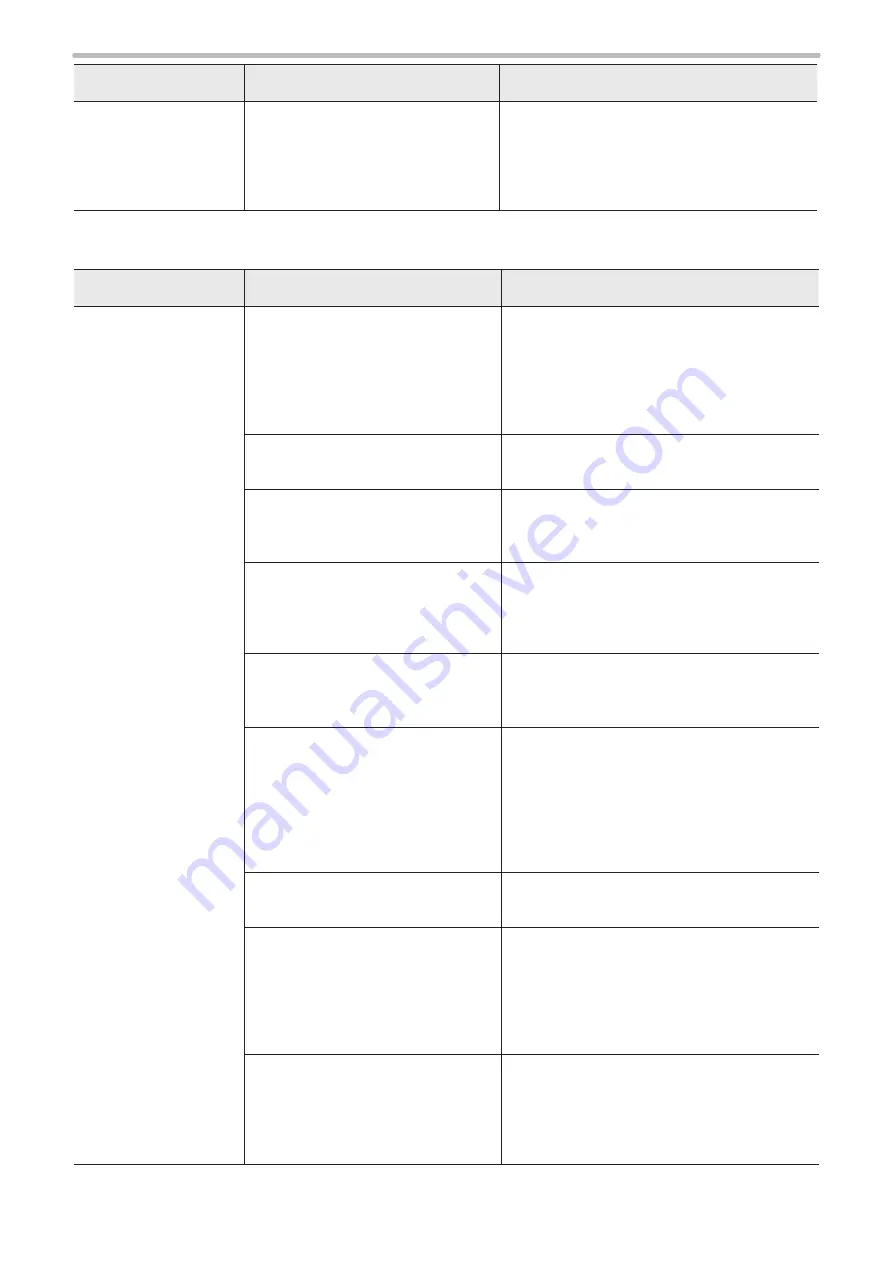
166
Troubles
Causes
Measures
Marking position is
deviated from the
expected setting position.
• The setting of the laser head
direction is not consistent with the
actual install direction.
• System offset values are input on
the system settings screen.
Check the setting direction of the laser head,
X-axis/ Y-axis offset or rotation offset setting of
the system settings screen.
⿎
Marking quality
Troubles
Causes
Measures
Marking is totally faded/
Marking is partially
faded.
Laser emission port is not clean.
• Clean contaminants off the laser emission
port by following the procedures described in
Setup/Maintenance Guide.
• For LP-RF/LP-RV series:
If contaminants persist, replace the protection
glass of the laser emission port.
Fumes occurring during lasing hinder
laser beam.
• Install dust collector.
• Check that dust collector works well.
Distance to the work piece is not
appropriate.
Adjust distance between bottom surface of laser
marker head and marking surface of the work
piece.
For LP-GS series:
The set Z-position does not match the
height of the actual target work piece.
(The LP-GSxxx-L type is excluded.)
Set the Z-position according to the work piece
height.
Marking surface of work piece is
inclined.
Make adjustment so that bottom surface of laser
marker head and marking surface of the work
piece are parallel with each other.
There are variations in properties of the
work pieces.
• Thickness varies.
• Surface roughness varies (including
those in gloss).
• Material varies (including those in
chemical composition).
Adjust the marking conditions and work distance
according to respective work pieces.
Work piece feeder is not stable.
Adjust work piece feeder so that work piece
position becomes stable.
Performance of laser oscillator
deteriorates due to aging.
• Increase setting value of laser power.
• Decrease scan speed.
If it is not possible to get the same marking quality
as before even with the max. value of the laser
power setting, laser oscillator must be replaced.
Contact our sales office.
For LP-RV series:
The setting value of the pulse duration is
not appropriate.
Adjust the pulse duration according to the material
of the work piece.
For plastic work pieces the pulse duration 4ns or
8ns is a common setting, and for metal, 16ns or
30ns is often selected.
ME-LPGS-SM-8
Summary of Contents for LP-GS Series
Page 17: ...1 Product Overview ME LPGS SM 8 ...
Page 32: ...2 Laser Marker Installation ME LPGS SM 8 ...
Page 48: ...3 Operation Method ME LPGS SM 8 ...
Page 68: ...4 External Control Using I O ME LPGS SM 8 ...
Page 107: ...5 External Control by Communication Commands ME LPGS SM 8 ...
Page 116: ...6 Link Control with External Devices ME LPGS SM 8 ...
Page 141: ...7 Maintenance ME LPGS SM 8 ...
Page 161: ...161 MEMO ME LPGS SM 8 ...
Page 162: ...Troubleshooting ME LPGS SM 8 ...
Page 186: ...Index ME LPGS SM 8 ...
Page 189: ......
Page 190: ... Panasonic Industrial Devices SUNX Co Ltd 2014 2019 April 2019 ...