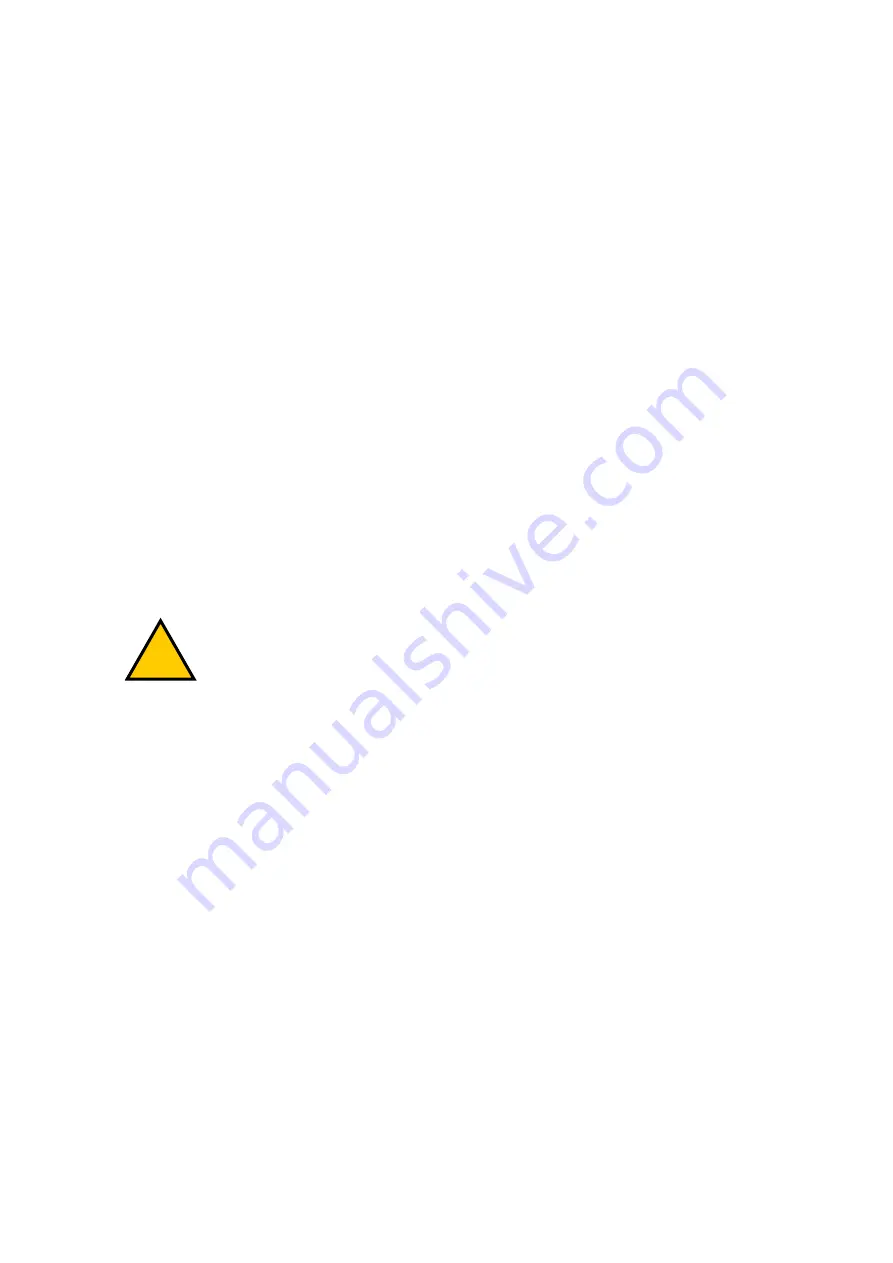
50
Viper 650 and 850 Robot with EtherCAT
21861-000 Rev A
Using a User-Supplied Control Panel
You can create a user-supplied control panel that performs the same functions as the optional
Front Panel. The optional Front Panel contains only switches and lights (no active com-
ponents).
Additional Information
: Refer to Front Panel Schematic on page 38 for internal
wiring information.
IMPORTANT:
Underwriters Laboratory evaluated the system with an OMRON
Front Panel. If you provide a substitute, the system may no longer be UL com-
pliant.
IMPORTANT:
Though the XMCP and XFP connectors can be interchanged
without electrical damage, neither the Front Panel nor the pendant will work
properly unless they are plugged into the correct connector.
Remote Pendant Usage
You can build an extension cable to place the pendant in a remote location. The extension
cable must conform to the following specifications:
l
Wire Size: must be 26 AWG (0.13 mm
2
) or larger.
l
Connectors: must be 15-pin, standard D-sub male and female.
l
Maximum cable length is 10 meters.
!
CAUTION: EQUIPMENT DAMAGE HAZARD
Do not modify the cable that is attached to the pendant. This could cause
unpredictable behavior from the robot system.
3.7 Setting the EtherCAT Node ID
The EtherCAT Node ID (address) can be set with two methods.
Use Hardware Switches on the eCS-ECAT
Use the hardware switches on the eCS-ECAT interface panel to set an explicit EtherCAT node
ID for the robot. Refer to Setting the EtherCAT Node ID Using Hardware Switches on page 51
for more information.
Use Sysmac Studio Software
When the EtherCAT node ID is set with Sysmac Studio, it is retained in non-volatile memory
and will persist after subsequent power cycles.
Additional Information
: Refer to the
Sysmac Studio Version 1 Operation Manual
(Cat. No. W504)
for more information about setting the EtherCAT node ID with
software.
IMPORTANT:
When using Sysmac Studio to set the EtherCAT node ID, ensure
the switches are set to the default 0 positions as shown in the figure below. If the
switches are set to a non-zero value, the switch positions will dictate the
EtherCAT node ID and software adjustment of this value is not possible.