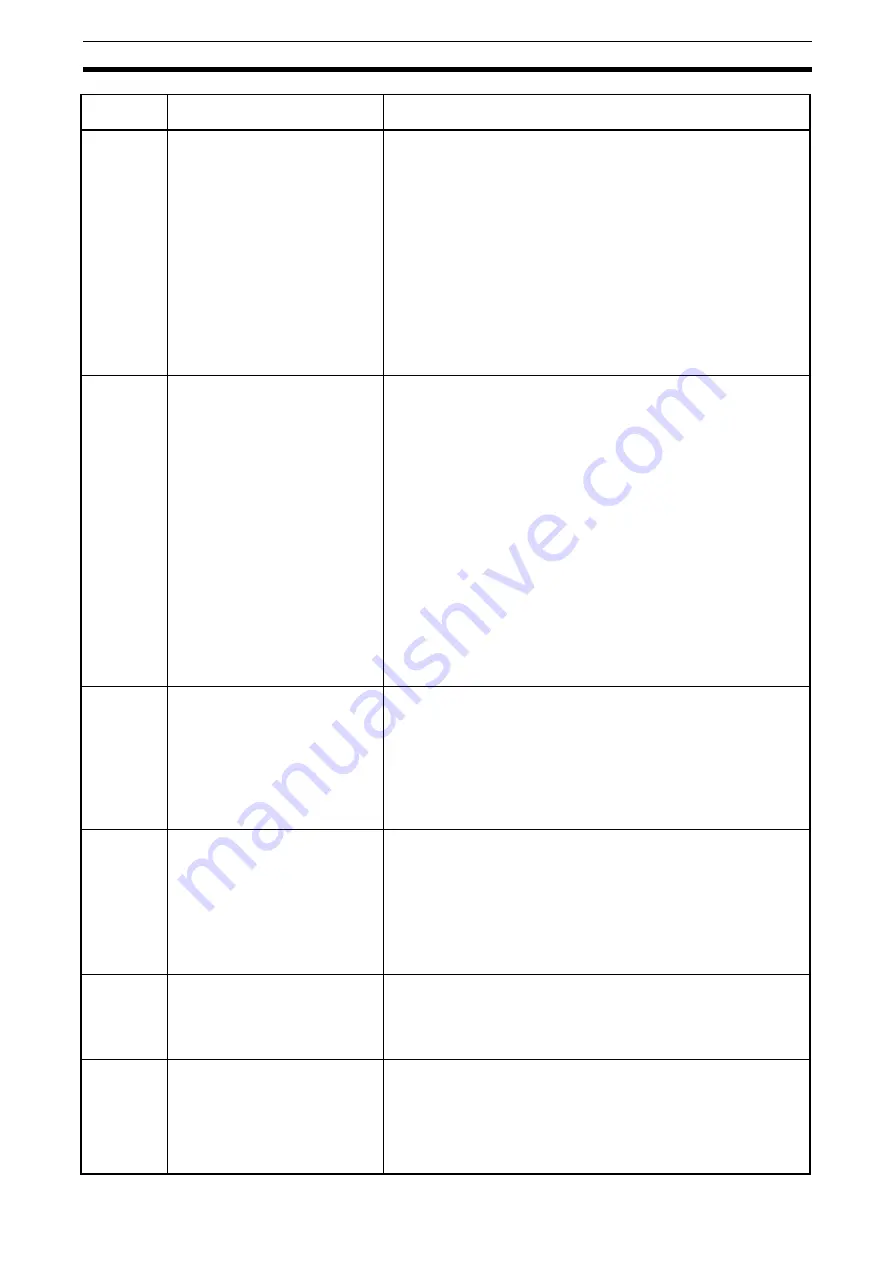
119
Protective and Diagnostic Functions
Chapter 8-1
%h
Radiation fin overheated (OH)
The temperature of the radiation
fins of the Inverter has reached
110°C ± 10°C.
• The ambient temperature is too high.
→
Ventilate the Inverter or install a cooling unit.
• The load is excessive.
→
Reduce the load.
→
Decrease the Inverter capacity.
• The V/f setting is incorrect.
→
Reduce the V/f set voltage.
• The acceleration/deceleration time is too short.
→
Increase the acceleration/deceleration time.
• The ventilation is obstructed.
→
Change the location of the Inverter to meet the
installation conditions.
• The cooling fan of the Inverter does not work.
→
Replace the cooling fan.
%l1
Motor overload (OL1)
The electric thermal relay actuated
the motor overload protective
function.
• The load is excessive.
→
Reduce the load.
→
Decrease the Inverter capacity.
• The V/f setting is incorrect.
→
Reduce the V/f set voltage.
• The value in n11 for maximum voltage frequency is low.
→
Check the motor nameplate and set n11 to the rated frequency.
• The acceleration/deceleration time is too short.
→
Increase the acceleration/deceleration time.
• The value in n32 for rated motor current is incorrect.
→
Check the motor nameplate and set n32 to the rated current.
• The Inverter is driving more than one motor.
→
Disable the motor overload detection function and install an
electronic thermal relay for each of the motors. The motor
overload detection function is disabled by setting n32 to 0.0 or
n33 to 2.
• The motor protective time setting in n34 is short.
→
Set n34 to 8 (the default value).
%l2
Inverter overload (OL2)
The electronic thermal relay has
actuated the Inverter overload
protective function.
• The load is excessive.
→
Reduce the load.
• The V/f setting is incorrect.
→
Reduce the V/f set voltage.
• The acceleration/deceleration time is too short.
→
Increase the acceleration/deceleration time.
• The Inverter capacity is insufficient.
→
Use an Inverter model with a higher capacity.
%l3
Overtorque detection (OL3)
There has been a current or torque
the same as or greater than the
setting in n60 for overtorque
detection level and that in n61 for
overtorque detection time. A fault
has been detected with n59 for
overtorque detection function
selection set to 2 or 4.
• The mechanical system is locked or has a failure.
→
Check the mechanical system and correct the cause of
overtorque.
• The parameter settings were incorrect.
→
Adjust the n60 and n61 parameters according to the
mechanical system. Increase the set values in n60 and n61.
gf
Ground fault (GF)
The ground fault current at the
output of the Inverter has
exceeded the rated output current
of the Inverter.
• A ground fault has occurred at the Inverter output.
→
Check the connections between the Inverter and motor and reset
the fault after correcting its cause.
ef
_
External fault
_
(EF
_
)
An external fault has been input
from a multi-function input. A multi-
function input 1, 2, 3, or 4 set to 3
or 4 has operated. The EF number
indicates the number of the
corresponding input (S2 to S5).
• An external fault was input from a multi-function input.
→
Remove the cause of the external fault.
• The sequence is incorrect.
→
Check and change the external fault input sequence including
the input timing and NO or NC contact.
Fault
display
Fault name and meaning
Probable cause and remedy
Summary of Contents for J7 series
Page 12: ...XII...
Page 15: ...1 CHAPTER 1 Overview 1 1 Function 2 1 2 Nomenclature 3...
Page 54: ...40 Outline of Operation Chapter 3 2...
Page 102: ...88 Other Functions Chapter 6 7...
Page 158: ...144 Option Specifications Chapter 9 3...
Page 159: ...145 CHAPTER 10 List of Parameters List of Parameters 146...
Page 172: ...158 List of Parameters Chapter 10...
Page 173: ...159 CHAPTER 11 Using the Inverter for a Motor Using the Inverter for a Motor 160...