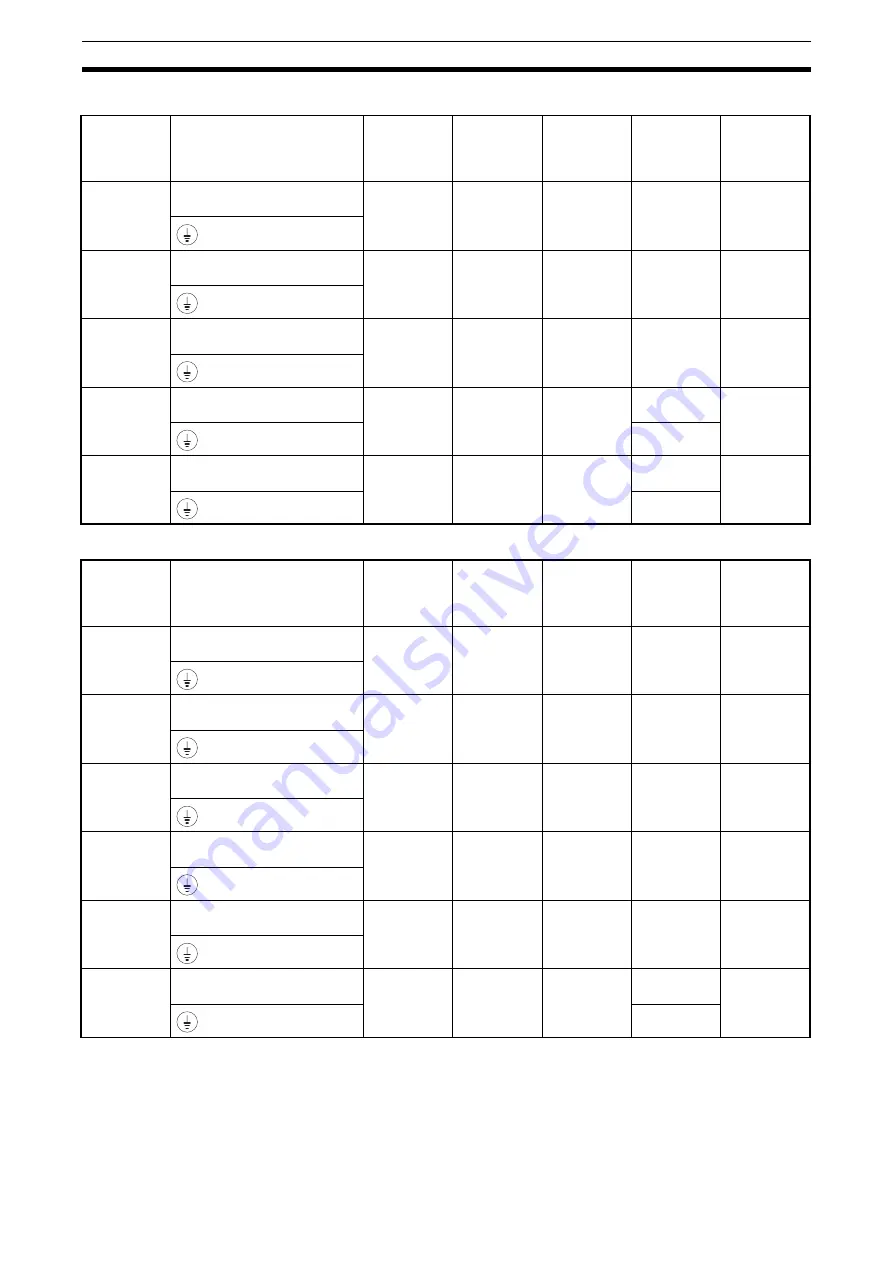
18
Wiring
Chapter 2-2
Single-phase 200-V AC Model
3-phase 400-V AC Model
Model
CIMR-J7AZ-
Terminal symbol
Terminal
screw
Terminal
torque
(N
•
m)
Wire size
(mm
2
)
Re-
commended
wire size
(mm
2
)
Circuit
breaker
capacity
(A)
B0P1
R/L1, S/L2, T/L3, –, +1, +2,
U/T1, V/T2, W/T3
M3.5
0.8 to 1.0
0.75 to 2
2
5
B0P2
R/L1, S/L2, T/L3, –, +1, +2,
U/T1, V/T2, W/T3
M3.5
0.8 to 1.0
0.75 to 2
2
5
B0P4
R/L1, S/L2, T/L3, –, +1, +2,
U/T1, V/T2, W/T3
M3.5
0.8 to 1.0
0.75 to 2
2
10
B0P7
R/L1, S/L2, T/L3, –, +1, +2,
U/T1, V/T2, W/T3
M3.5
0.8 to 1.0
2 to 5.5
3.5
20
2
B1P5
R/L1, S/L2, T/L3, –, +1, +2,
U/T1, V/T2, W/T3
M3.5
0.8 to 1.0
2 to 5.5
5.5
20
2
Model
CIMR-J7AZ-
Terminal symbol
Terminal
screw
Terminal
torque
(N
•
m)
Wire size
(mm
2
)
Re-
commended
wire size
(mm
2
)
Circuit
breaker
capacity
(A)
40P2
R/L1, S/L2, T/L3, –, +1, +2,
U/T1, V/T2, W/T3
M3.5
0.8 to 1.0
2 to 5.5
2
5
40P4
R/L1, S/L2, T/L3, –, +1, +2,
U/T1, V/T2, W/T3
M3.5
0.8 to 1.0
2 to 5.5
2
5
40P7
R/L1, S/L2, T/L3, –, +1, +2,
U/T1, V/T2, W/T3
M3.5
0.8 to 1.0
2 to 5.5
2
5
41P5
R/L1, S/L2, T/L3, –, +1, +2,
U/T1, V/T2, W/T3
M3.5
0.8 to 1.0
2 to 5.5
2
10
42P2
R/L1, S/L2, T/L3, –, +1, +2,
U/T1, V/T2, W/T3
M4
1.2 to 5.5
2 to 5.5
2
10
44P0
R/L1, S/L2, T/L3, –, +1, +2,
U/T1, V/T2, W/T3
M4
1.2 to 1.5
2 to 5.5
2
20
3.5
Summary of Contents for J7 series
Page 12: ...XII...
Page 15: ...1 CHAPTER 1 Overview 1 1 Function 2 1 2 Nomenclature 3...
Page 54: ...40 Outline of Operation Chapter 3 2...
Page 102: ...88 Other Functions Chapter 6 7...
Page 158: ...144 Option Specifications Chapter 9 3...
Page 159: ...145 CHAPTER 10 List of Parameters List of Parameters 146...
Page 172: ...158 List of Parameters Chapter 10...
Page 173: ...159 CHAPTER 11 Using the Inverter for a Motor Using the Inverter for a Motor 160...