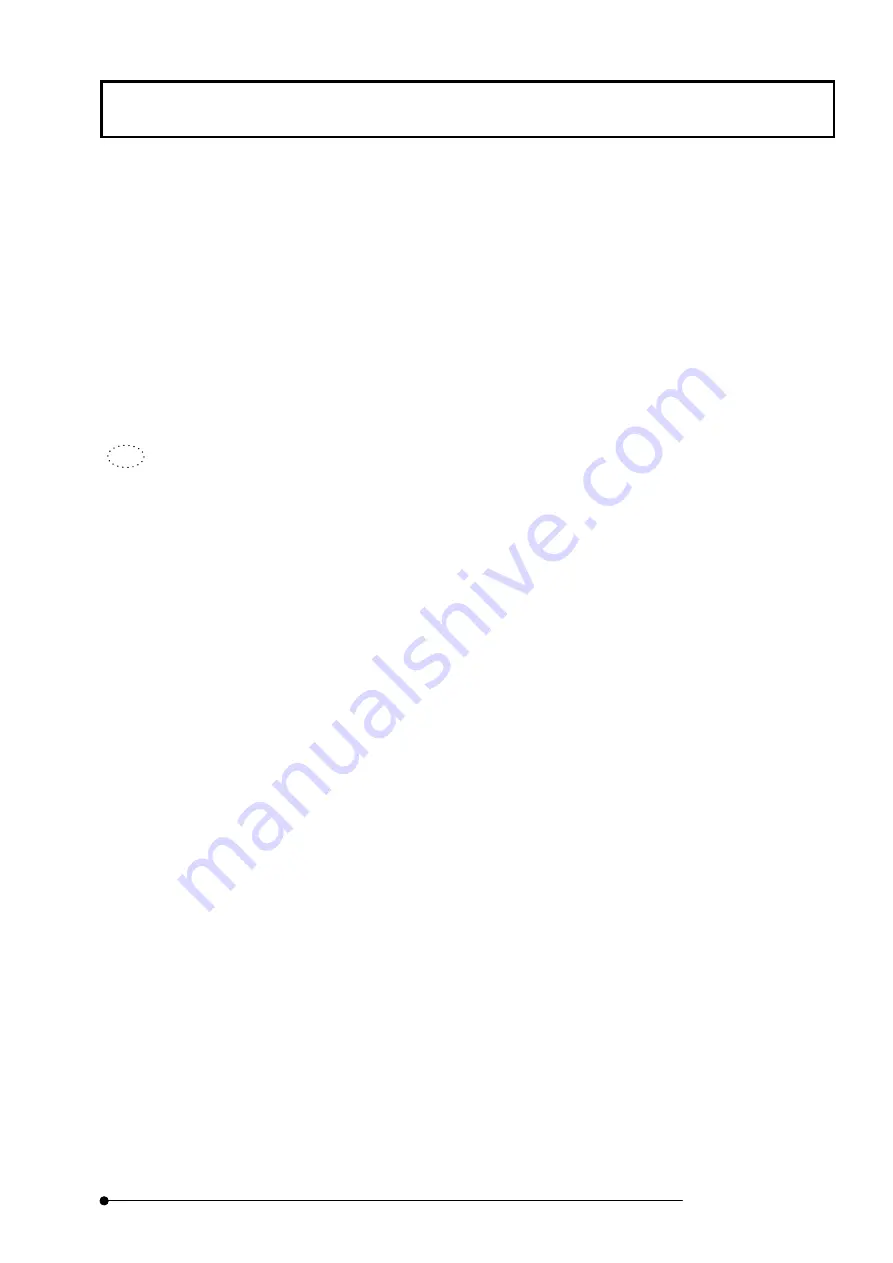
Operation Manual
Inspections
3-9
*
By setting the vacuum stage to the wafer transfer position during Back Macro inspection, the Back Macro
inspection is terminated before the inspection time is completed. Microscope inspection is given preference
and the wafer is transferred onto the vacuum table.
*
If Microscope inspection is not required, press the [Unload] button. The first wafer is unloaded into the
cassette and the second wafer is transferred to the Back Macro inspection position.
7.
Subsequent wafers are transferred automatically and sequentially.
8.
After the last wafer is unloaded into the cassette, the operating units return to their initial positions and the
loader stops.
9.
Replace the cassette with the next one, and repeat the procedure from step 1.
Ref.
*
If [2nd Back Macro] is selected for the inspection sequence, refer to
[3-2-4 Back Macro Insp 2nd
Back Macro Inspection]
.
Page
Summary of Contents for AL120-6 Series
Page 2: ...This page intentionally left blank ...
Page 9: ...Operation Maintenance Manual Introduction Safety Precautions i 7 Page AL120 86 Series Unit mm ...
Page 16: ...Introduction Conformity Standards Operation Maintenance Manual i 14 Page ...
Page 17: ...Operation Maintenance Manual Introduction Conformity Standards i 15 Page ...
Page 21: ...Operation Manual Table of Contents C 3 Page 4 When a Wafer is on the Vacuum Stage 5 10 ...
Page 22: ...Operation Manual Table of Contents C 4 This page intentionally left blank Page ...
Page 58: ...Inspections Operation Manual 3 14 This page intentionally left blank Page ...