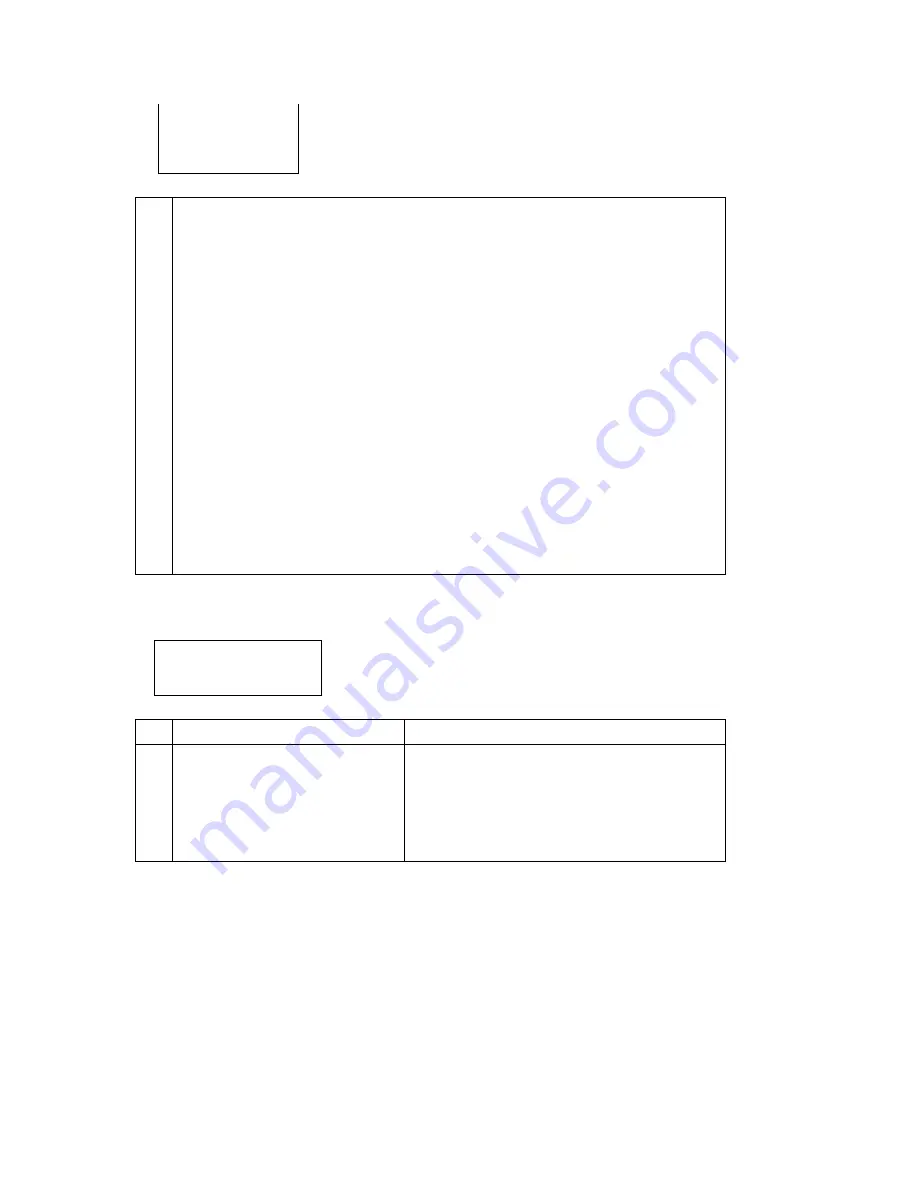
(
27
)
Card Jam error in Encoder
Card JAM. Encode
Area 09 Er -
Ad
Er Ad Symptom
Check/Repair
78
**
Card jam error in the
Area09
(
SN15
)
while the
card is transported in
Encoder .
(
1
)
Check that the card is staying in the
problem area. If no card, replace
following
things.
(
2a
)
Check there is something of which
obstruct
the card transportation around the
stacked
card.
After removing stacked card, then check
roller working in the Encoder.
If it does not work correctly , replace the
Encoder.
(
28
)
IC R/W Access Error
IC R/W Control
Error Er- Ad
Er Ad Symptom
Check / Repair
7E
01
Printer received the
command
to quit the access to internal
IC R/W
(
Non contact type
)
A printer is no problem.
See an operation manual of application
software
or contact the administrator of the total
system.