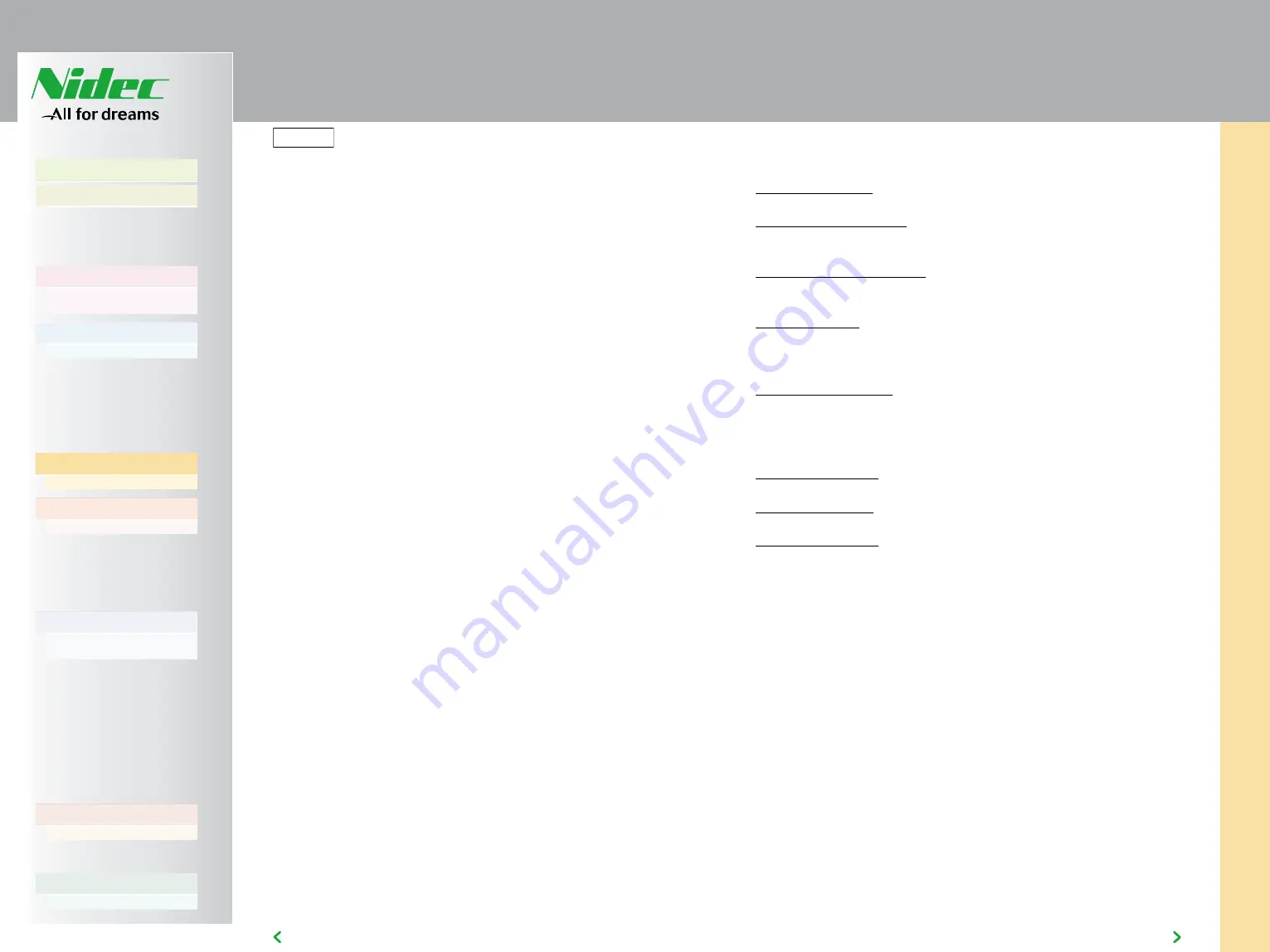
Summary
Preface
P. 6
Chapter 2
P. 17
Technical data
Chapter 5
P. 76
Reception, storage
and installation
Chapter 4
P. 54
General information
Chapter 3
P. 47
Application notes
Chapter 6
P. 115
Options
Chapter 7
P. 129
Preventive maintenance
Chapter 1
P. 15
Overview
and installation diagram
Answer Drives 1000
50
3
3.3 DRIVE SELECTION
• The AD1000 size choice has to be based on the drive rated current,
rather than on its power.
The drive output current must be greater than the rated current of the
controlled motor.
• The motor rated voltage must be greater than 1/2 of the input voltage
and the motor rated current must be 1/3 greater than the output current
of the AD1000.
• If a single drive feeds several motors, it is necessary to choose a
AD1000 with a 10% greater output current compared to the sum of the
motor currents. Provide an independent hardware thermal protection for
each motor; the thermal protection software inside the AD1000 is not
effective for multi-motor applications.
• The vector control cannot be used in applications with multiple motors
in parallel. Use the vector V/f control.
• If the multi-motor application requires to enable and disable some
motors during the drive operation, choose a AD1000 with a current
rated value adequate to handle the sum of the maximum current values
of all motors connected and of the starting current of the motor(s) that
have to be enabled.
• The starting and acceleration torque of a motor controlled by an drive
is limited by the maximum current of the drive. Select an oversized drive
if a high starting torque is required.
3.4 APPLICATION NOTES
• If the application requires a contactor on the motor side, the contactor
should be switched only when the drive is disabled. The contactor must
be interlocked with the drive running logic
• In case of failure of the AD1000, the driving shaft rotates freely; if this is
not permissible, it is necessary to install a mechanical brake.
• With power supply from a generator set, make sure that the generator is
able to counteract the harmonic distortion produced by the drive.
• The AD1000 includes the “dynamic braking” function; its use can cause
high motor temperatures. If this function is used frequently, check that
the motor is adequately dimensioned or contact the manufacturer.
3.5 APPLICATIONS WITH SPECIAL MOTORS
• Motors with brakes. The brake must have an independent power supply.
When the brake is engaged, the drive must be disabled.
• Motors with conical rotor. The brake is controlled by the magnetic field
of the motor; if necessary introduce or adjust the boost; in some cases it
is necessary to use an drive of greater size.
• Motors with double winding. The output current of the drive must be
higher than the rated current of each motor winding. The winding can
be switched with motor off and drive disabled.
• Classified motors. The drive cannot be operated in environments with
danger of explosion or fire. If the motor and the drive must be operated
in this type of environment, they must be provided both in explosion-
proof version.
• Transmission couplings. The lubrication system and the rotation limits
vary from manufacturer to manufacturer; with lubricating oil, frequent
operations at low speeds may cause overheating due to insufficient
lubrication. Check with the manufacturer the possibility of prolonged
operation at these speeds.
• Synchronous motors. It is advisable to provide an output reactance to
compensate for the insufficient inductance in the motor.
• Submersible pumps. The rated current of these motors is higher than the
standard.
• Single-phase motors. The AD1000 is not designed to control
single-phase motors.
3.3 DRIVE SELECTION - 3.4 - 3.5
BACK 1.2
Summary of Contents for AD1A008FBBNH
Page 138: ......