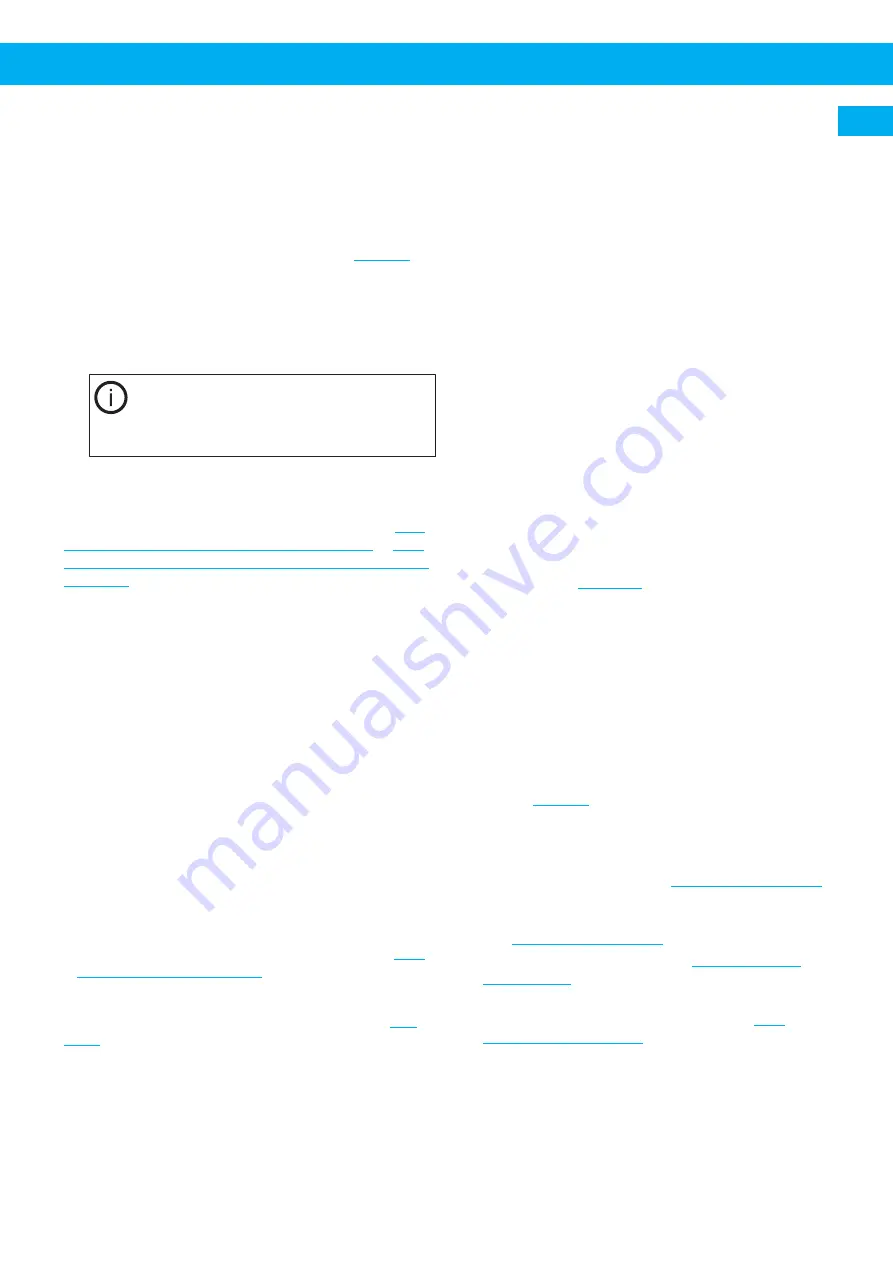
VAC 20
2
Remove the motor side panel for easy access to
the screws that anchor the motor.
3
Replace worn or damaged belts and pulleys.
4
Check the tension of the belt transmission and ad-
just if required.
• The following figures can serve as a guide for all
VAC models and give the force F necessary to
apply to one of the belts as shown in
for
10 mm slack:
• New belts: F = 24 N (5.4 lbf)
• Used belts: F = 20 N (4.5 lbf)
5
Put back the motor side panel.
6
Put back the belt guard.
NOTE!
New belts are liable to stretch slightly with-
in the first hours of use and are to be more
tightly tensioned than used belts.
8.3 Anti-surge control
Every 500 hours check that the unit does not pump
and that the valve ‘floats’ at varying airflow. See
tion 7.2.4 Adjusting anti-surge control by PLC
tion 7.2.5 Adjusting anti-surge control by optional ad-
aption kit
8.4 Start-up valve
Perform the following start-up valve inspection every
500 hours of operation:
• Check that the spring holds the valve closed when
the unit is standing still.
• Check that the spring holds the valve closed when
the motor is in Y-mode.
• Check that the valve is open when the motor is in D-
mode.
8.5 Flow restrictor FR 160
Perform the following flow restrictor inspection every
500 hours of operation:
• Check that the flow restrictor is activated when the
motor current tends to exceed the nominal current.
Observe the damper arm at varying airflows. The
variation must cover the range where the restrictor
is activated. If adjustments are necessary, see
8.5.1 Adjusting FR 160
Perform the following to adjust the FR 160, see
1
Remove the protection cap, Item 5, covering the
spring.
For fine adjustments: Loosen the screws, Item 7,
to release the disc, Item 8.
• Turn the disc clockwise to increase the airflow
and motor load.
• Turn the disc anti-clockwise to decrease the air-
flow and motor load.
For coarse adjustments: Move the free end of the
spring to the nearest hole on the disc.
2
Measure the motor amperage to check the result-
ing adjustment. This is usually made with a clamp
ampere meter around one of the three incoming
phases to the motor start and control unit.
• A correct adjustment limits the motor current to
a reading matching the nominal current stated
on the machine tag. A certain over current,
~10%, is accepted just before the restrictor
goes into operation.
3
Lock the disc.
4
Refit the protective cap covering the spring.
8.5.2 Flow restrictor oil
There is a risk that the restrictor starts self-oscillating
when the oil level is low. This can cause damage to the
restrictor and the fan.
Perform the following flow restrictor oil level check
every 500 hours of operation:
• Turn the restrictor shaft rapidly by hand all the way
to the outer end position when the vacuum unit
stands still, see
.
• If the resistance is uneven: Check the oil level with
a suitable probe. Top up the oil to a level 70-80
mm over the piston surface if necessary. Use auto-
matic transmission fluid.
• If the resistance is even: The oil level is correct.
8.6 Fan bearings temperature
Perform the following fan bearings temperature con-
trol inspection every 500 hours of operation:
• Check the bearing temperature on the two fan bear-
. Normal temperature range is 50–
90°C (122–194°F).
• If the temperature is above 95°C (203°F) ensure
the following:
• The ambient air is cool. See
for information.
• The openings for cooling and ventilation are free.
See
• The belt is properly fitted. See
for information about maintenance
of belts.
• The bearings are in good condition. See
on how to replace dam-
aged or worn bearings.
8.7 Fan bearings
Change the fan bearings within 15,000 hours of op-
eration, or sooner if there is reason to suspect dam-
aged bearings. See mounting instruction MI12-002 for
more information.
EN
23
Summary of Contents for 40103102
Page 8: ...VAC 20 Figures 1 2 3 4 5 6 7 8 1 1 2 1 2 3 3 8 7 6 4 3 2 1 5 4 8 ...
Page 9: ...VAC 20 1 2 3 4 7 11 10 5 6 8 9 5 9 ...
Page 12: ...VAC 20 9 X U1 V1 W1 W2 U2 V2 X 10 35 ml ATF 70 85 mm 11 10mm 0 39 12 1 2 3 4 5 6 7 13 12 ...
Page 13: ...VAC 20 14 13 ...
Page 224: ...VAC 20 PL Opis Symbol Wynik Uwagi Wymiana silnika Punkt 8 8 Łożyska silnika 224 ...
Page 290: ...www nederman com ...