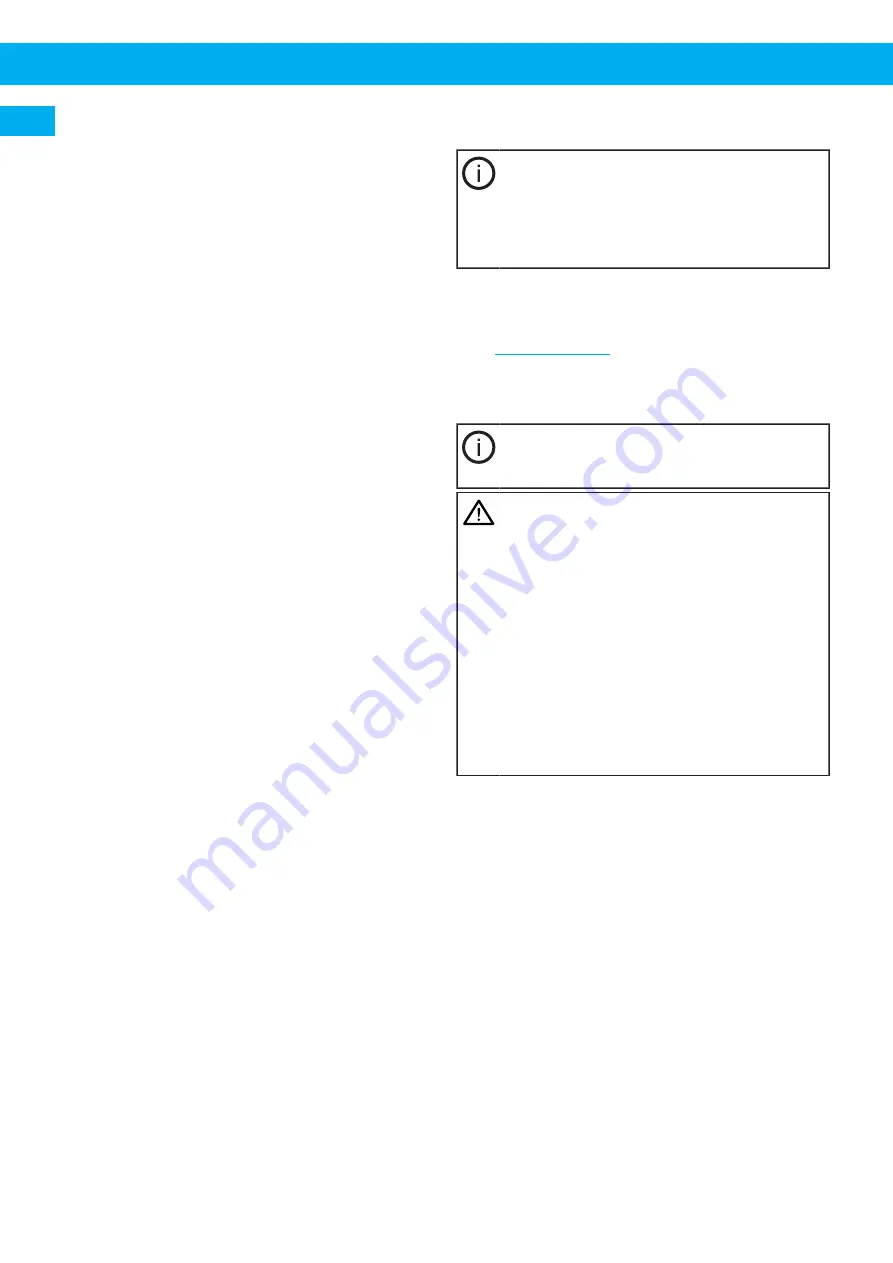
VAC 20
EN
Switching to D mode before the motor has reached
full speed can damage the start and control unit. This
is particularly important when an automatic start and
stop is installed. Too long in Y mode results in an un-
necessary delay before the unit delivers full vacuum.
At initial start-up check the Y/D time setting by doing
the following:
• Make sure the motor sound is constant and high
pitched, indicating full motor power, before the mo-
tor switches to D mode.
7.2.3 Initial start-up with pilot signal cable
For units with pilot signal cable also ensure the fol-
lowing at initial start-up:
• The unit only starts directly when one of the follow-
ing occurs:
• A valve is opened at a worksite, causing the mi-
croswitch to close.
• The test start button is pressed on the start and
control unit (if available).
• The unit shuts down when the time set on the timer
relay has elapsed after the valve is closed (up to 30
minutes).
7.2.4 Adjusting anti-surge control by PLC
For adjusting the anti-surge control by the PLC, see
the start- and control units' manual.
Testing the Anti Surge Control
Observe the damper rotation on the valve angle in-
dicator on the front of the damper motor. For inform-
ation on how to monitor the motor current, see the
start- and control units' installation manual.
Stop the vacuum unit. Seal off the ducting completely
on the inlet side or “suction side”. Do not do anything
on the outlet. Start the unit.
Now the airflow through the fan is zero, and the PLC
current control loop senses that the motor current is
below the set point threshold and initiates ASC PLC
opening damper sequence. The damper starts to ro-
tate anti-clockwise “Opening the valve,” and lets in
bypass air into the fan.
The motor current increases gradually, and when the
current is within ± 5% of the setpoint, the damper
motor stops.
Remove the sealing from the ducting to gradually in-
crease the airflow and observe the rise of the motor
current. When the current increases to over 5% of the
motor current setpoint, the ASC PLC closing damper
sequence initiates, and the damper starts to rotate
clockwise “Closing the valve.” This reduces the bypass
air into the fan until the damper is completely closed.
Finally, verify full functionality of the ASC function by
gradually closing and opening the sealing/restriction
of the airflow on the inlet ducting.
7.2.5 Adjusting anti-surge control by op-
tional adaption kit
NOTE!
For VAC controlled by the HV Control Panel,
the testing procedure is the same but the ad-
justments are made in the PLC in the HV Con-
trol Panel. See the HV Control Panel manual for
more information.
See the manual included in the adaption kit.
8 Maintenance
before carrying out mainten-
ance.
It is recommended to install an hour service meter in
the start and control unit.
NOTE!
The intervals in this chapter are based on the
unit being professionally maintained.
WARNING! Risk of personal injury
• Work with electric equipment must be carried
out by a qualified electrician.
• Use proper protective equipment when risk-
ing exposure to the dust.
• Always disconnect the supply voltage before
any servicing, whether mechanical or elec-
trical. Always lock any maintenance switch in
the off position.
• Ensure that no vacuum is present in the sys-
tem during service.
• Make sure the unit is cool before undertaking
an inspection to avoid burn. The unit and its
parts can get very hot.
8.1 General inspection
Perform the following general inspection every 500
hours of operation:
• Inspect the incoming connections. Ensure all cables
and hoses are tightly fitted.
• Check for signs of corrosion or other damage.
• Check that the ventilation inlet and outlet of the
unit are clear.
• Check that the ventilation to the room is clear (if
placed indoors).
• Check for dust or collected material inside the unit.
Dust or collected material may indicate a filter mal-
function.
8.2 Belt transmission
Perform the following belt transmission inspection
every 500 hours of operation:
1
Remove the belt guard.
22
Summary of Contents for 40103102
Page 8: ...VAC 20 Figures 1 2 3 4 5 6 7 8 1 1 2 1 2 3 3 8 7 6 4 3 2 1 5 4 8 ...
Page 9: ...VAC 20 1 2 3 4 7 11 10 5 6 8 9 5 9 ...
Page 12: ...VAC 20 9 X U1 V1 W1 W2 U2 V2 X 10 35 ml ATF 70 85 mm 11 10mm 0 39 12 1 2 3 4 5 6 7 13 12 ...
Page 13: ...VAC 20 14 13 ...
Page 224: ...VAC 20 PL Opis Symbol Wynik Uwagi Wymiana silnika Punkt 8 8 Łożyska silnika 224 ...
Page 290: ...www nederman com ...