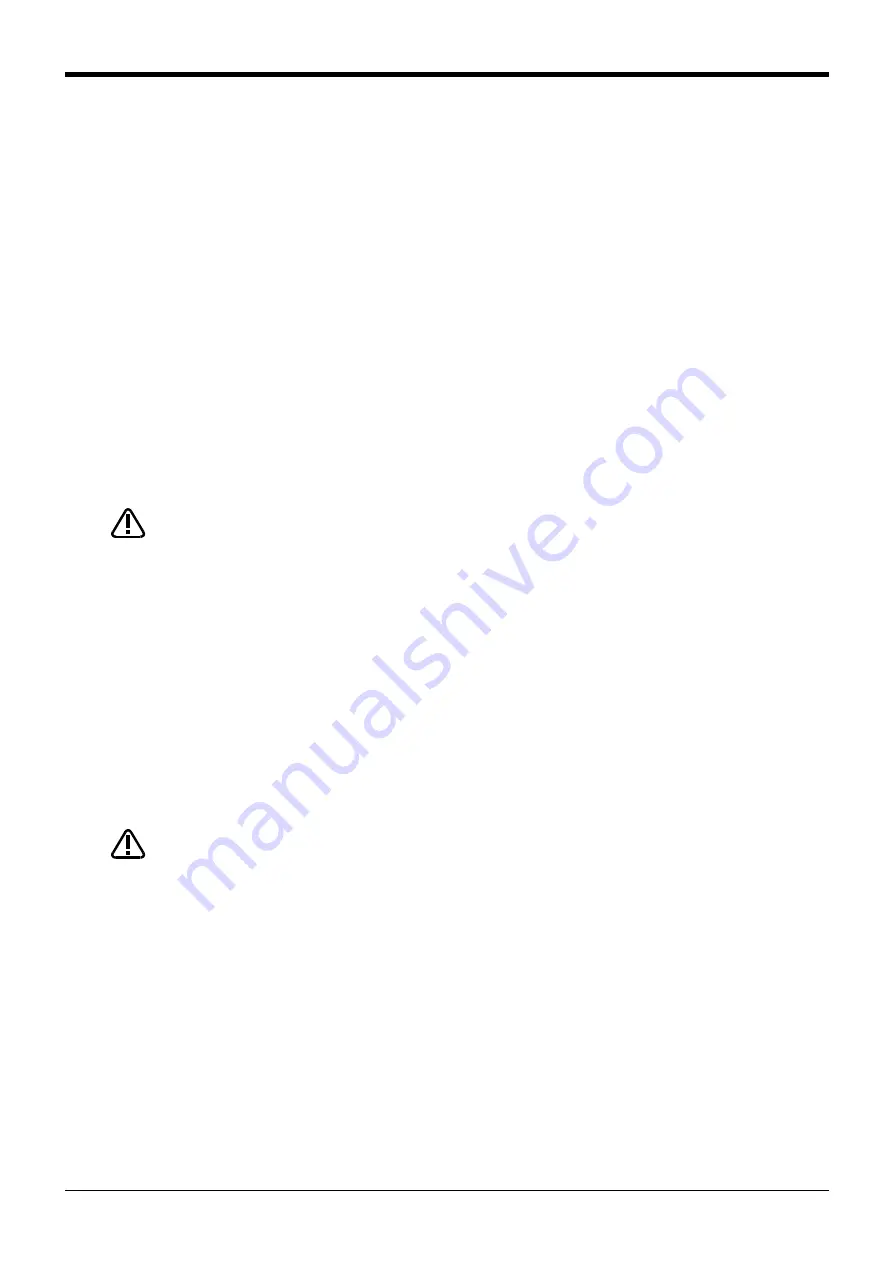
3Installing the option devices
Hand internal wiring and piping set 3-66
3.5 Hand internal wiring and piping set
Remove the No. 2 arm cover U and fix this option to the plate on the No. 2 arm.
Turn the controller’s power OFF before this operation. Refer to
Page 81, "5.3.2 Installing/removing the cover"
for
removing/ installing the cover.
(1) Installation procedure
The installation procedure is shown below.
Refer to the installation diagram shown from the next section, and perform the installation correctly. Installation
diagram of RH-3FH series is shown in
, and RH-6FH series is shown in
, RH-12FH/20FH series is
1) Move the J3 axis to the top end with a jog operation and shut off the controller's power supply. This is
necessary for space standard settings when feeding the air hose and hand input cable through the inside of
the shaft.
2) Remove the screws fixing the No. 2 arm cover U, and remove the No. 2 arm cover U.
3) Pass the tool (hand) side of the secondary piping air hoses and hand input cables through the shaft. Make
sure that the air hoses and the cables are not twisted or crossed.
4) Fix the air hoses and the cables with a cable tie so as to position the end of the expanding sleeve 10mm
away from the opening of the shaft.
5) The highest point of the curved section of the air hoses and cables should be matched up with the top of
the fixing plate.
If the air hoses and the cables are not long enough or too long, when the robot oper
-
ates, excessive bending and friction with the shaft upper end or the cover may result
in a break or abnormal operations of the tool (hand).
6) In the state of the steps
, fix the air hoses and the cables to the (a) and (b) portions of the plate
with cable ties. For the (a) portion, wrap the air hoses and the cables with cushion rubber before fixing.
7) Cut the secondary piping air hoses in appropriate length, and connect the air hoses to the solenoid valve.
The diagram shows the connection to the optional solenoid valve as an example. The air hoses can also be
pulled out from the rear of the No. 2 arm by using another option: an external wiring and piping box. For the
details, refer to
Page 71, "3.6 External Wiring and Piping Box"
For the connection to the optional solenoid valve, connect the air hoses to the A and B ports of the sole
-
noid valve.
8) When using the hand input cable connect the connectors (HC1, HC2) of optional hand input cable to
connectors (HC1, HC2) of robot side. Connect with the same names. The connectors of robot side and
cables are tied up by cable tie at (c) portion. Cut the cable tie and pull them out.
The connected connectors are stored to the (c) portion.
When the hand input cable is not used tie up the connector and fix to the plate by cable tie.
Do not remove the cable ties which fixing connectors.
Fix the plate on the No. 2 arm, other cables and air hoses with cable ties. In this way,
the internal cables and connectors do not touch the plate edge and others, or break
due to the vibration during the robot operation.
9) Carry out piping and wiring on the tool side.
Fix the air hoses and the cables, which are pulled out from the shaft lower end, to the hand side. Check
again that the highest point of the curved section of the air hoses and the cables reaches the height of the
fixing plate upper end, and then fix the air hoses and the cables at the outlet of the shaft. In the case of
oil-mist and clean specification models, to avoid mists entering and ensure the cleanliness level, use liquid
gasket and others to seal the outlet on the shaft tip where the air hoses and the cables are pulled out.
10) Apply silicon grease to the contact surface between the air hoses of the fixing plate and the cables, the
cable sliding portion from the shaft upper end to the fixed portion, and the opening on the shaft upper end.
11) Power on the controller, perform the jog operation for the J3 and J4 axes, and check that the air hoses
and the cables do not interfere with other components.
CAUTION
CAUTION