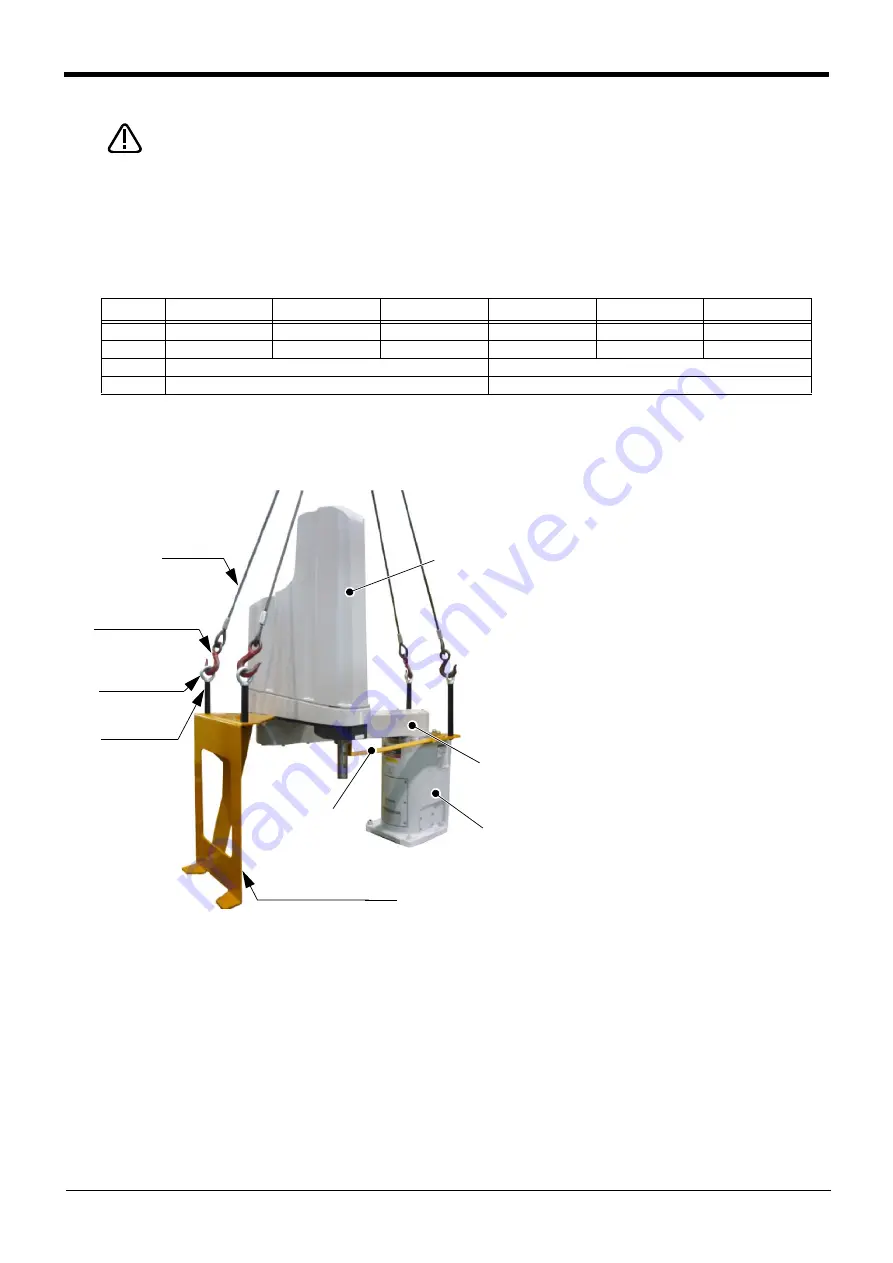
2-9
Installation
2Unpacking to Installation
If it is difficult to follow the transportation procedure shown in this section, take
countermeasures not to allow the joints of the robot arm freely move by fixing the robot
arm in such a way as to take advantage of the screw holes for fixing plates or the like.
Otherwise, applying an excessive power on the joints by external forces may cause a
malfunction.
Do not apply an excessive load to the robot arm while fixing it. Otherwise, the robot arm
may be damaged.
Table 2-2 : Transportation posture
(2) RH-12FH/20FH series
Fig.2-3 : Transportation of robot arm
1) Hook the wires to each of the four eyebolts attached to the transporting jig. (Make sure the bolts are
securely hooked.)
2) Lift with a crane to transport the robot to the designated location.
3) At this time, make sure that the wires, etc., do not interfere with the robot arm or the covers. Always place
the cloth, etc., at interfering places.
4) Be careful not to subject the robot to physical shock during transport.
5) After installing the robot (refer to
Page 11, "2.2.3 Installation procedures"
), remove the wires, the wire
hooks (the robot will stand by itself as shown in
), the self-supporting plate, transporting jig and fix
-
ing plate.
6) Always attach the self-supporting plate, fixing plate, and transporting jig, and follow the above procedures
and methods to transport the robot for secondary transportation, such as when changing the installation
position.
If the arm is directly suspended without using the specified transporting jig, or if it is suspended in the work
Axis
RH-3FH35**
RH-3FH45**
RH-3FH55**
RH-6FH35**
RH-6FH45**
RH-6FH55**
J 1
49.5 deg.
25 deg.
17 deg.
57.5 deg.
28 deg.
19 deg.
J 2
-139.5 deg.
-115 deg.
-107 deg.
-147.5 deg.
-118 deg.
-109 deg.
J 3
290.4mm
290.4mm
J 4
Not fixed
Not fixed
CAUTION
Mass
RH-12FH55** series: Approx. 65kg
RH-12FH70** series: Approx. 67kg
RH-12FH85** series: Approx. 69kg
RH-20FH85** series: Approx. 75kg
RH-20FH100** series: Approx. 77kg
Self-supporting plate
Base
Transport
-
ing jig
Fixing plate
Eye bolt
No.1 arm
Wire hook
Wire
Note 1)
No.2 arm
*The grease for preventing rust is applied at the
tip of the shaft (J3 axis) in general-purpose
environment robot.
Note 1) Use wires that are 1300 mm or more.