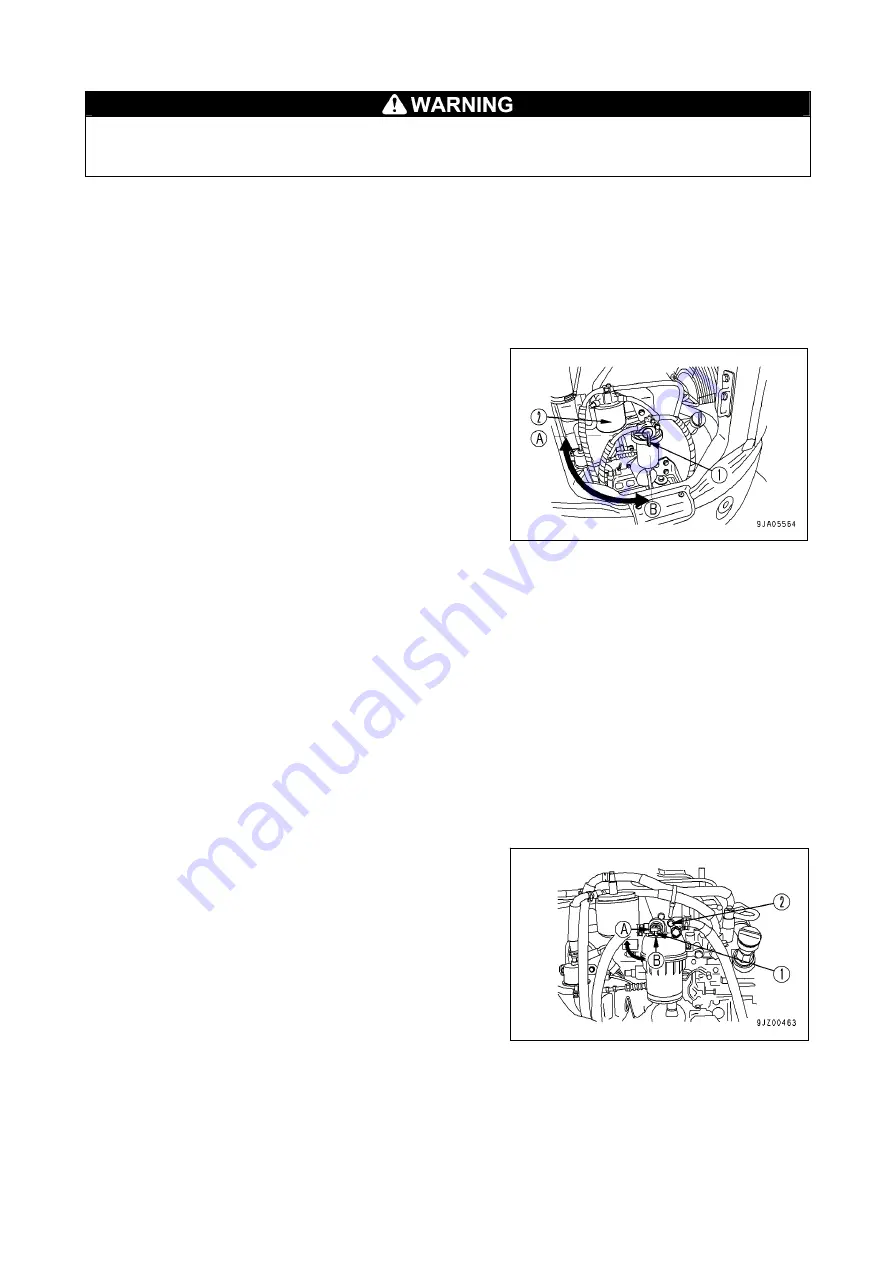
231
[2] REPLACEMENT OF MAIN FUEL FILTER
• Various parts are at elevated temperatures immediately after stopping the engine operation.
Always drain the coolant after the engine has cooled down.
• Keep away from flame.
• Have a filter wrench available.
• Have a waste cloth prepared.
1. Open the engine bonnet.
2. Place the waste cloth below the filter cartridge.
3. Turn the handle (1) of the water separator to the closed
position (A).
4. Using a filter wrench, turn the filter cartridge (2) to the
left to remove it. If fuel is spilt, wipe cleanly with the
waste cloth.
5. Clean the filter, fill the new filter cartridge with clean fuel,
lightly apply fuel on the packing, and mount the
cartridge on the filter base.
6. When installing, tighten about one rotation with a filter
wrench after turning it to the right and the packing
surface touches the sealing surface of the filter base.
Tightening torque: 19.6 – 23.5 N·m (2.0 – 2.4 kg·m)
7. Turn the handle (1) of the water separator to the open
position (B).
8. After replacing the filter cartridge, vent the air.
Refer to the “Procedure for Air Bleeding” section and
vent the air.
PROCEDURE FOR AIR BLEEDING
1. Fill up the fuel tank with fuel until full.
2. Turn the handle (1) of the water separator to the open
position (B).
3. Loosen the air venting bolts (2) of the water separator
by turning 2 to 3 times.
4. Tighten the air bleed bolt (2) when bubble-free fuel
comes out from the air bleed bolt (2).
Summary of Contents for CC423S-1
Page 2: ......
Page 8: ...vi This Page Intentionally Left Blank...
Page 22: ...14 This Page Intentionally Left Blank...
Page 56: ...48 SAFETY LABEL LOCATIONS 2 2...
Page 59: ...51 24 Machine Mass 542 4773100 28 Working Radius Rated Total Load Chart 542 3582200...
Page 60: ...52 30 Safe Operation 557 3494500 31 Operating the Moment Limiter 542 2250000...
Page 194: ...186 This Page Intentionally Left Blank...
Page 232: ...224...
Page 248: ...240 This Page Intentionally Left Blank...
Page 251: ...243 2 SPECIFICATION DIMENSIONAL DRAWING...
Page 255: ...247 4 WORKING RADIUS LIFTING HEIGHT 4 Fall Wire Rope...
Page 256: ...248 This Page Intentionally Left Blank...
Page 262: ...254 3 MONITOR INDICATION 1 Searcher hook selector switch 2 Searcher hook position display...
Page 276: ......
Page 277: ......
Page 278: ......