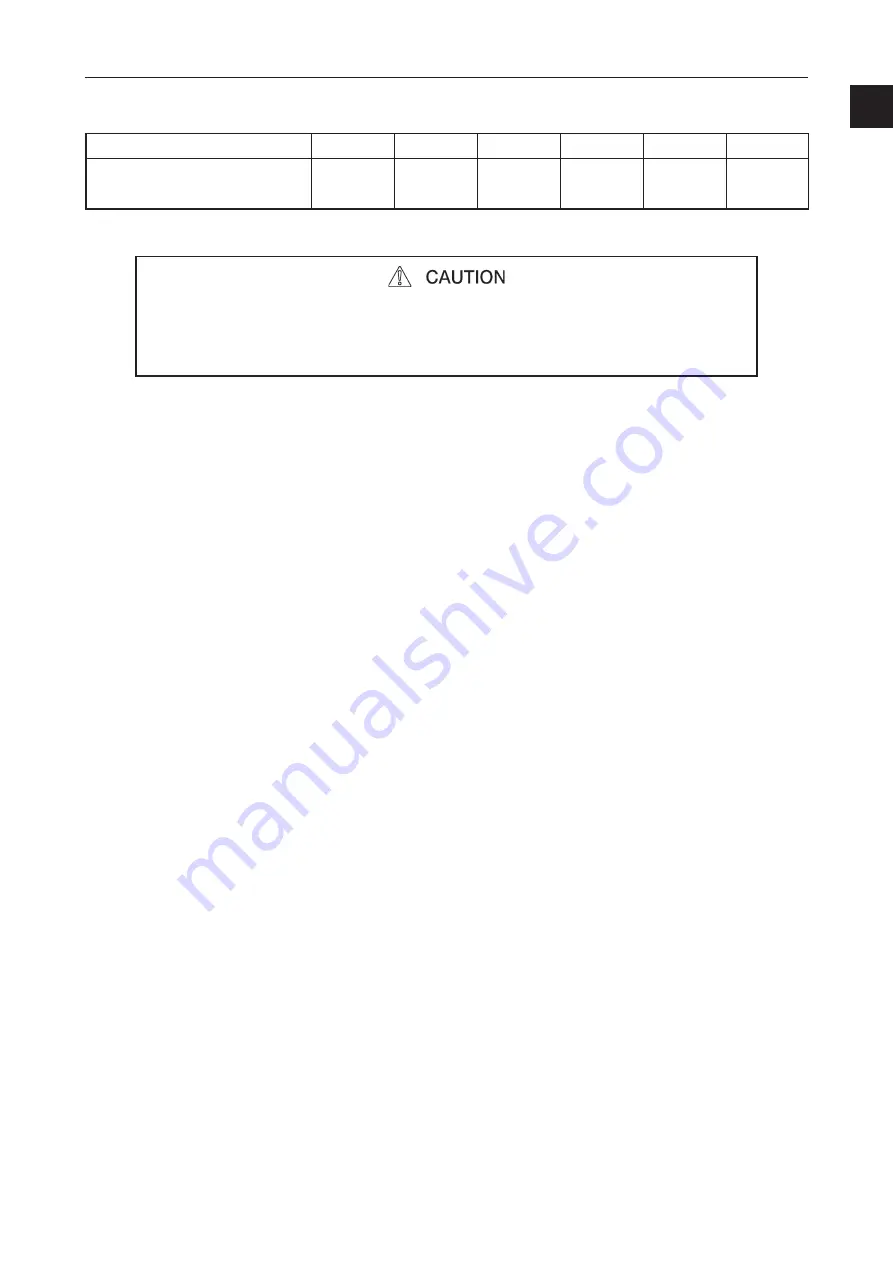
Tightening torque table
1. Tightening torque table
- 279 -
(13) Attachment for hydraulic and pneumatic equipments
Units: N
・
m (kgf
・
m)
Screw size
M6
M8
M10
M12
M14
M20
Tightening torque
10
(1)
23
(2.3)
59
(6)
78
(8)
167
(17)
275
(28)
(01E0-0522-0E)
・
After the first 50 hours of use of a new machine and every month thereafter inspect and
retighten the bolts.
・
When tightening, clean off any corrosion, earth and debris.
(01E0-0523-0E)
Summary of Contents for REDGZM HD514MR-7
Page 2: ...218621 背厚 13 mm 中 ...
Page 9: ... 7 8 Specifications 8 2 General data 01E0 0023 0E ...
Page 12: ... 10 MEMO ...
Page 56: ... 40 2 Part names and terms 2 2 2 Inside the cab 01E0 0050 1E ...
Page 57: ... 41 Part names and terms 2 Part names and terms ...
Page 58: ... 42 2 Part names and terms 2 2 3 Outside the cab 01E0 0051 1E ...
Page 148: ... 132 8 Lifting a load 2 HD514MR LC 7 ...
Page 183: ... 166 2 Inspection and servicing table 1 Part names for inspection and servicing ...
Page 184: ... 167 Inspection and servicing table 2 Inspection and servicing table ...
Page 185: ... 168 2 Inspection and servicing table ...
Page 200: ... 183 3 Lubrication Lubrication 3 5 Oiling chart 01E0 0293 0E ...
Page 261: ... 244 244 MEMO ...
Page 290: ... 272 MEMO ...
Page 315: ... 296 296 5 Electrical circuit diagram 5 Electrical circuit diagram 01EE 0609 0E ...
Page 316: ... 297 297 5 Electrical circuit diagram Electrical circuit diagram ...
Page 317: ... 298 298 MEMO ...
Page 325: ...899 92186210 ...