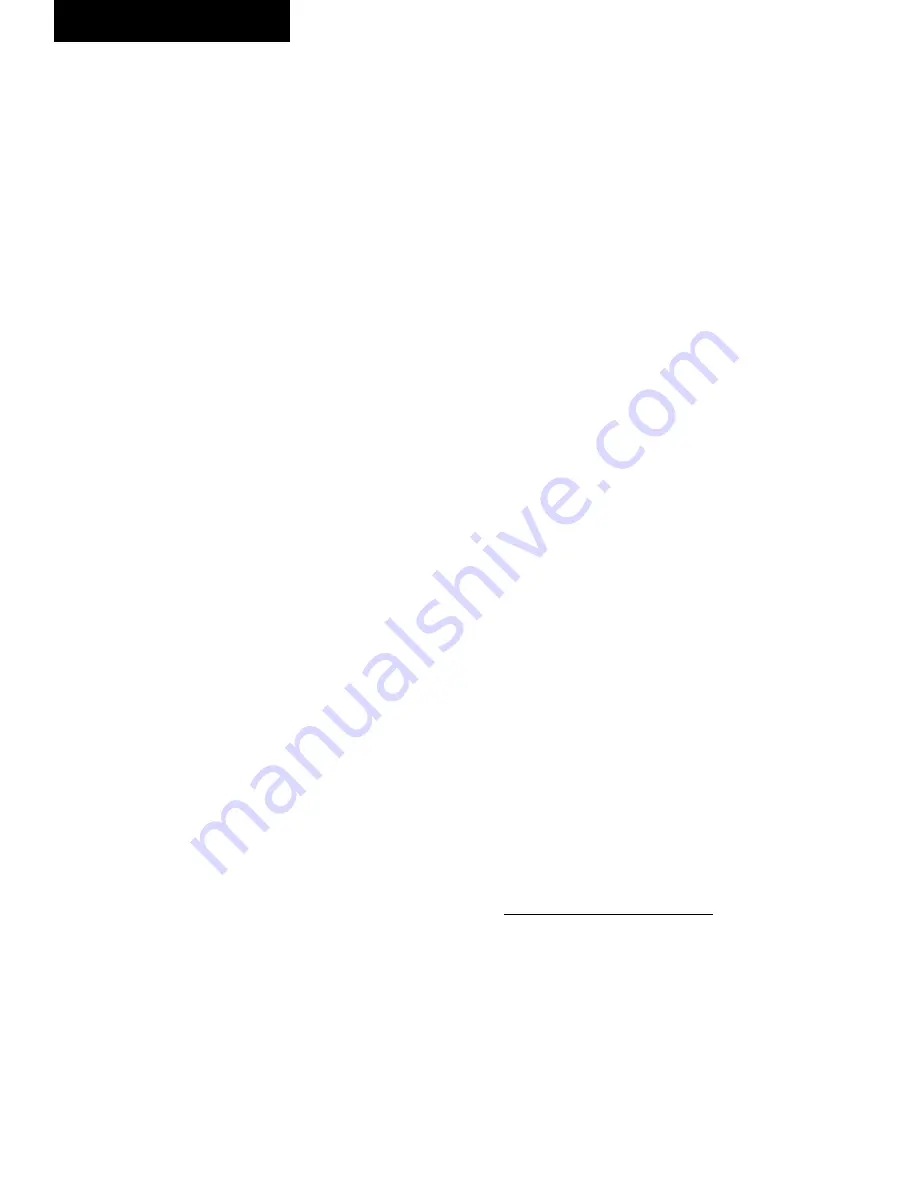
JOHNSON CONTROLS
160
FORM 160.54-O1
optiView Control Center
the difference between the output of the Sump Oil Pres-
sure Transducer (system low pressure) and the output of
the Pump Oil Pressure Transducer (system high pressure).
The chiller can be started after the differential oil pressure
decreases to less than 90.0 PSID and the COMPRESSOR
switch is placed in the Stop-reset (O) position.
“
OIL – PUMP PRESSURE TRAnSDUCER OUT
OF RAngE
”
The Pump Oil Pressure Transducer (system high pres-
sure) is indicating a pressure that is less than 0.0 PSIG
or greater than 315.0 PSIG. This is outside the normal
operating range of the transducer. This generally indicates
a defective transducer. The chiller can be started after the
transducer is indicating a pressure that is within range and
the
COMPRESSOR
switch is placed in the Stop-reset
(O) position.
“
OIL – SUMP PRESSURE TRAnSDUCER OUT
OF RAngE
”
The Sump Oil Pressure Transducer (system low pressure)
is indicating a pressure that is outside the normal operating
range of the transducer as follows: R134a - <0.0 PSIG or
>315.0 PSIG, R22 - <23.2 PSIG or >271.8 PSIG. This
generally indicates a defective transducer. The chiller can
be started after the transducer is indicating a pressure that
is within range and the COMPRESSOR switch is placed
in the Stop-reset (O) position.
“
OIL - DIFFEREnTIAL PRESSURE
CALIBRATIOn
”
The Sump and Pump oil pressure Transducers indicated a
differential oil pressure of greater than 15.0 PSID during
the oil pressure transducer Auto-Zeroing period that begins
10 seconds into “System Pre-lube” and lasts for 3 seconds.
This is indicative of a defective Sump or Pump Transducer,
since the oil pump is not running during this period and the
actual differential oil pressure is 0 PSID. The transducers
are sensing the same pressure during this period and their
outputs should be similar. The chiller can be started after
the COMPRESSOR switch is placed in the stop-reset
(O) position.
“
OIL – VARIABLE SPEED PUMP – SETPOInT
nOT ACHIEVED
”
This is only applicable to chillers equipped with the
Oil Pump Variable Speed Drive. One of the following
conditions have occurred while in “System Prelube”,
“System Run” or “System Coastdown”. The chiller can
be started after the
C
OMPRESSOR switch is placed
in the Stop-reset (O) position. With software version
C.OPT.01.18.307 (or later), this safety shutdown is not
performed when the Refrigerant Selection (microboard
SW1-1) is set to “R22”.
1. The differential oil pressure was less than 35.0 PSID;
(less than 25 PSID for “P” compressors equipped
with software version C.01.10A.xxx (and earlier)
or C.OPT.01.10A.xxx (and earlier) for 5 continuous
seconds during the last 10 seconds of the “System
Prelube” period or during the first 15 seconds of
“System Run”.
-OR-
2. Anytime after the first 30 seconds of “System run”,
the differential oil pressure was less than the Oil
Pressure Setpoint with the speed command from the
Microboard at 60 Hz for 5 continuous seconds.
“
COnTROL PAnEL – POWER FAILURE
”
A Control Power failure has occurred. If the power fail-
ure duration was less than the duration of the applicable
“Coastdown” period (2.5 minutes standard; 15 minutes steam
turbine), the remainder of the “Coastdown” is performed
upon restoration of power. The chiller can be started after the
COMPRESSOR switch is placed in the Stop-reset (O)
position. This message can indicate a Cycling (auto-
restart after power failure) or Safety (manual restart
after power failure) shutdown, depending upon Control
Center configuration. It indicates a Cycling shutdown
when displayed in orange characters; Safety shutdown
when displayed in red characters. The Control center is
configured for auto-restart or manual restart after power
failure by a qualified Service technician following in
-
structions in YORK Service Manual 160.54-M1.
“
MOTOR OR STARTER – CURREnT
IMBALAnCE
”
The three phase compressor motor current imbalance
was greater than 30% continuously for 45 seconds.
The imbalance is not checked until the chiller has been
running for at least 45 seconds and the average of the
three phases of motor current is greater than 80% of the
programmed 100% chiller Full Load Amps. The average
is calculated as: Iave = (Ia+Ib+Ic) / 3. The imbalance
is calculated as:
(Ia-Iave) + (Ib-Iave) + (Ic-Iave)
x
100
2(Iave)
The Style B Solid State Starter and Variable Speed
Drive detects the unbalance condition and advise the
Optiview Control Center Microboard via serial commu-
nications. The Style A Solid State Starter and Variable
Speed Drives returns the 3-phase motor current values
to the Optiview Control Center Microboard where the
unbalance calculation is performed. This safety shut-
down is not performed on Electro-mechanical starter
applications.
Summary of Contents for YORK YK MaxE
Page 10: ...JOHNSON CONTROLS 10 FORM 160 54 O1 OptiView Control Center THIS PAGE INTENTIONALLY LEFT BLANK...
Page 17: ...FORM 160 54 O1 17 JOHNSON CONTROLS 2 THIS PAGE INTENTIONALLY LEFT BLANK...
Page 59: ...FORM 160 54 O1 59 JOHNSON CONTROLS 2 THIS PAGE INTENTIONALLY LEFT BLANK...
Page 65: ...FORM 160 54 O1 65 JOHNSON CONTROLS 2 THIS PAGE INTENTIONALLY LEFT BLANK...
Page 79: ...FORM 160 54 O1 79 JOHNSON CONTROLS 2 THIS PAGE INTENTIONALLY LEFT BLANK...
Page 91: ...FORM 160 54 O1 91 JOHNSON CONTROLS 2 THIS PAGE INTENTIONALLY LEFT BLANK...
Page 105: ...FORM 160 54 O1 105 JOHNSON CONTROLS 2 THIS PAGE INTENTIONALLY LEFT BLANK...
Page 113: ...FORM 160 54 O1 113 JOHNSON CONTROLS 2 THIS PAGE INTENTIONALLY LEFT BLANK...
Page 123: ...FORM 160 54 O1 123 JOHNSON CONTROLS 2 THIS PAGE INTENTIONALLY LEFT BLANK...
Page 133: ...FORM 160 54 O1 133 JOHNSON CONTROLS 2 THIS PAGE INTENTIONALLY LEFT BLANK...
Page 166: ...JOHNSON CONTROLS 166 FORM 160 54 O1 Printers...