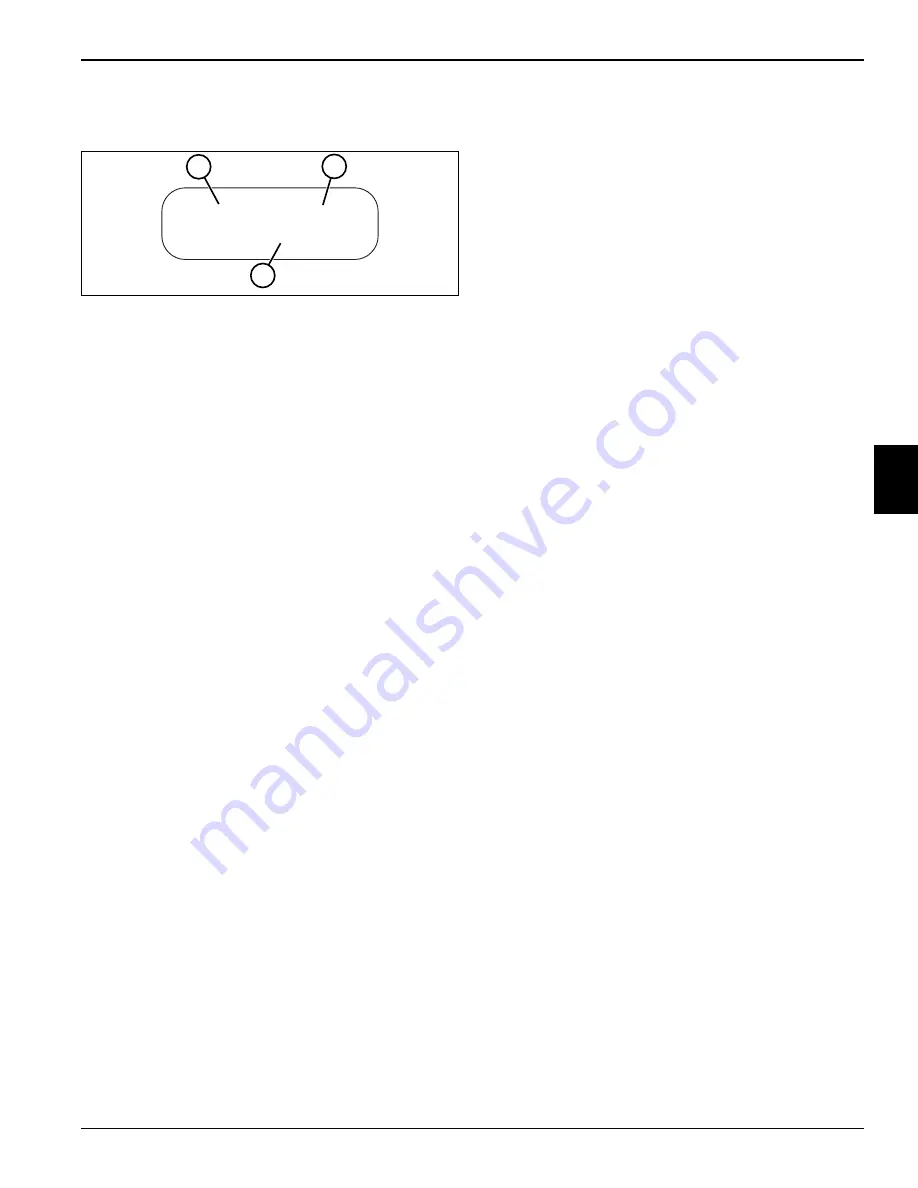
ELECTRICAL
4222983 Second Edition
4-77
4
Reel Motor Temperature
See Figure 4-53.
Figure 4-53
Cycle through the LCD menu until the reel motor
temperature screen is displayed. The display will indicate
the temperature of each reel motor.
If one of the reel motors goes above 266° F (130° C), the
following will occur:
• The LCD sounds the alarm and turns on the fault
LED.
• Diagnostic fault code is displayed for the faulty reel.
(See “DTC: Left Reel Temperature” on page 4-96.)
(See “DTC: Center Reel Temperature” on
page 4-96.) (See “DTC: Right Reel Temperature” on
page 4-97.)
Fault: Check Reel
1.
Fault: RCU did not recognize reel motor speed
(RPM) within range (FOC/Max Reel Speed)
2.
Possible root cause(s) and troubleshooting
procedure:
a. Verify output light at RCU
b.
Mechanical overload
i.
Tight reel to bedknife
ii.
Bad reel bearings, bearing end play, thick
heavy grease or excessive lack of lubrication
iii. Heavy grass, debris, or divots
c.
Poor connection at motor – Turck connector style
i.
Check threaded sleeve for a proper and
secure connection
ii.
Jiggle connector with clam shell removed
while the reel and motor are running.
d.
Faulty or damaged harness (main, motor, motor
controller)
i.
Visual inspection
ii.
Measure continuity: DMV-Ohms should be
less than 0.5 Ohms and no crossover
between circuits.
iii. Check wiring routing and securing as
specified in dealer’s manual.
e.
Motor is faulty
i.
Swap motor with known good motor
f.
Motor controller is faulty (Split-motor design
ONLY)
i.
Swap motor controller with known good
motor controller
g.
Jumper cable or Molex connector between motor
and motor controller is faulty or pinched
(Split-motor design ONLY)
i.
Visual inspection
ii.
Measure continuity: DMV-Ohms should be
less than 0.5 Ohms and no crossover
between circuits.
iii. Check wiring routing and securing as
specified in dealer’s manual.
h.
Harness between RCU and motor controller
(Split-motor design ONLY)
i.
Visual inspection
ii.
Measure continuity: DMV-Ohms should be
less than 0.5 Ohms and no crossover
between circuits.
i.
Actuator signal harness issue (Unlikely)
i.
Attempt to raise cutting unit while fault is
present. If reel cannot be raised, see “Check
Actuator” troubleshooting procedure.
j.
RCU faulty (Very Unlikely)
i.
Swap RCU outputs (J6, J7 or J8) to
determine if problem moves. Leave all three
reel switches engaged
1.
If problem moves, check harness or
component. If problem does not move,
RCU is faulty
2.
If not, start over at Step 1
3.
Fixes:
a.
For issue 2.b: Reduce or remove the mechanical
overload or obstruction.
b.
For issue 2.c.i: Tighten threaded sleeve.
c.
For issue 2.c.ii: Replace molded Turck connector
harness.
d.
For issue 2.d: Repair or replace harness and
route as specified in dealer manual.
e.
For issue 2.e: Replace motor. If issue is
corrected, reinstall old motor to verify fault
returns.
f.
For issue 2.f: Replace motor controller. If issue is
corrected, reinstall old motor controller to verify
fault returns.
1
Left Reel Motor Temp
3
Center Reel Motor Temp
2
Right Reel Motor Temp
80 REEL 80
TEMP 80 F
TN2774
1
3
2
Summary of Contents for Eclipse 322
Page 1: ...Eclipse 322 Riding Greens Mower Technical Repair Manual 62801 62803 62805 Second Edition...
Page 2: ......
Page 4: ......
Page 8: ......
Page 13: ...SAFETY 4222983 Second Edition 1 5 1 9 41 8 1 8 64 8 4127335 10 4181865 11...
Page 20: ...1 12 4222983 Second Edition SAFETY 1 Page Intentionally Blank...
Page 110: ...4 36 4222983 Second Edition ELECTRICAL 4 Page Intentionally Blank...
Page 128: ...4 54 4222983 Second Edition ELECTRICAL 4 Page Intentionally Blank...
Page 241: ...ELECTRICAL 4222983 Second Edition 4 167 4 Page Intentionally Blank...
Page 242: ...4 168 4222983 Second Edition ELECTRICAL 4...
Page 266: ...5 24 4222983 Second Edition CHASSIS 5 Page Intentionally Blank...
Page 332: ...IX 14 4222983 First Edition INDEX IX...
Page 333: ......
Page 335: ......
Page 336: ......