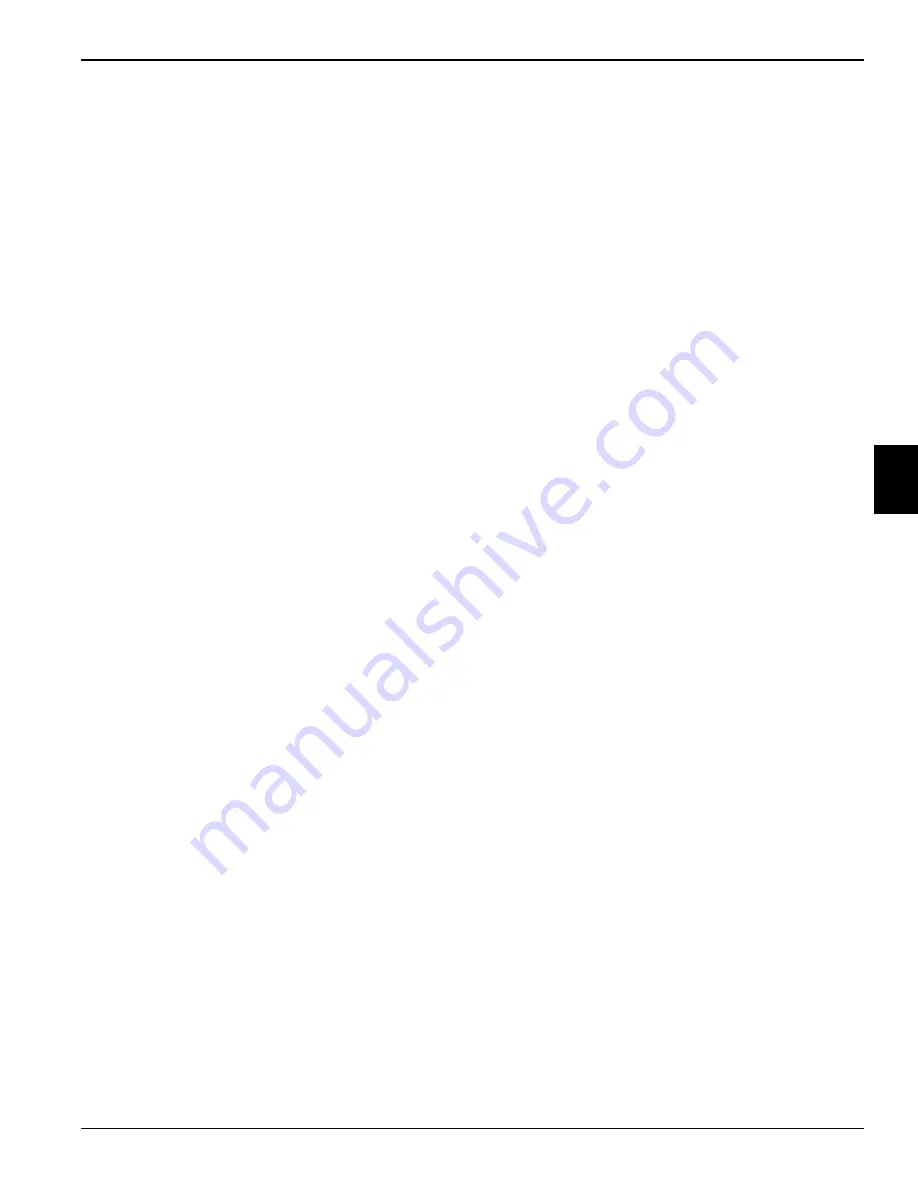
ELECTRICAL
4222983 Second Edition
4-55
4
Traction Circuit—Theory of Operation
Power Circuit
Unswitched 48V power is available from stud 3 through
150A fuse (F8) and 0.02 ohm resistor (R6) to key switch
terminal A and liquid crystal display (LCD) terminal
J11-8.
When the key switch is turned to the run position, 48 volts
is provided from key switch terminal B to liquid crystal
display (LCD) ignition terminal J11-5, powering up the
LCD.
With the LCD powered up, a ground is provided from the
LCD switched power contactor output terminal J11-10 to
the power distribution unit (PDU) terminal J1-4. With a
ground provided to J1-4, the 12 and 48 volt switched
power contactors are energized.
With the PDU 12 volt switched power contactor
energized, 12 volts is provided through 0.02 ohm resistor
(R12) to the main control unit (MCU) 12 volt power input
terminal J2-8. PDU terminal J1-5 also provides 12 volts
to splice E and then from splice E, 12 volts is provided to
MCU 12 volt power input terminal J2-6. With the PDU 48
volt switched power contactor energized, 48 volts is
provided to circuit breaker (F4) and MCU 48 volt power
input terminal J2-7, powering up the MCU.
The LCD converts the 48 volts supplied to LCD terminal
J11-8 to 12 volts. The 12 volts is used as the source
voltage for the control panel switches and seat switch.
LCD +12V power supply terminal J11-6 provides 12 volts
to splice G. Splice G provides 12 volts to seat switch
terminal J41-1.
Forty-eight volts is provided from 48 volt switched power
contactor through 0.08 ohm resistor (R1) to PDU terminal
(J1-2) and splice B. Splice B provides 48 volts to traction
control unit 48V input terminal J44-1, powering up the
traction control unit (TCU). With traction control unit
(TCU) powered up, the TCU 5V supply terminal J44-3
provides 5 volts to traction motor 5V power input terminal
J74-D.
Forty-eight volts is provided from the PDU 48 volt power
bus to the 48 volt traction contactor. The 300A fuse (F9)
provides protection to the traction circuit.
Traction Circuit
The operator must be on the seat before the main control
unit (MCU) allows the traction control unit (TCU) to
operate the traction motor when the traction pedal is
depressed. With the operator on the seat, voltage is
provided from seat switch terminal J41-2 to MCU seat
switch input terminal J4-10, activating the input.
With the seat switch input activated, MCU traction
contactor output terminal J3-6 provides a ground to PDU
48 volt traction contactor terminal J1-3, energizing the
contactor. With the 48 volt traction contactor energized,
voltage is provided to TCU J43-B+ terminal, the TCU
converts the DC voltage to AC voltage to drive the
traction motor.
After the 48 volt traction contactor is energized by the
MCU, the TCU performs a brake test. With the brake
applied, the TCU momentarily activates the traction
motor. If the TCU detects movement, the TCU will not
allow the traction motor to operate and communicates
this condition to the MCU. The MCU de-energizes the 48
volt traction contactor and instructs the LCD to display a
traction fault.
As the forward traction pedal is depressed, the forward
switch closes and the traction pedal forward signal
terminal J48-5 provides a 48 volt signal to the TCU
forward input terminal J44-12, activating the input. With
the input activated, the TCU will turn the traction motor in
the forward direction.
As the reverse traction pedal is depressed, the reverse
switch closes and traction pedal reverse signal terminal
J48-4 provides a 48 volt signal to the TCU reverse input
terminal J44-20, activating the input. With the input
activated, the TCU will turn the traction motor in the
reverse direction.
When the TCU forward or reverse inputs, are activated,
the TCU brake output terminal J44-2 provides a ground
to the brake pedal switch terminal J73-NC2. With the
brake switch plunger in the released position, brake
switch terminal J73-NC1 provides ground to splice O.
Splice O provides ground to brake coil terminal J47-B,
energizing the brake coil. Ground is also provided from
splice O to MCU brake input terminal J3-12, activating
the input. Diode V6 conducts to ground the reverse
voltage generated when the brake coil is de-energized.
As the traction pedal is moved in the forward or reverse
direction, a signal is provided to the TCU relative to the
position of the pedal. The TCU uses this signal to control
the speed of the traction motor. Traction pedal position
sensor output terminal J48-3 connects to TCU traction
pedal sensor input terminal J44-9.
As the brake pedal is depressed, a voltage is provided
from brake pedal position sensor signal output terminal
J49-C to the TCU brake sensor input terminal J44-7. The
TCU begins to slow the traction motor. When the brake
pedal is fully depressed, the normally closed brake switch
contacts open, de-energizing the brake coil. With the
brake coil de-energized, a spring fully applies the brake.
Summary of Contents for Eclipse 322
Page 1: ...Eclipse 322 Riding Greens Mower Technical Repair Manual 62801 62803 62805 Second Edition...
Page 2: ......
Page 4: ......
Page 8: ......
Page 13: ...SAFETY 4222983 Second Edition 1 5 1 9 41 8 1 8 64 8 4127335 10 4181865 11...
Page 20: ...1 12 4222983 Second Edition SAFETY 1 Page Intentionally Blank...
Page 110: ...4 36 4222983 Second Edition ELECTRICAL 4 Page Intentionally Blank...
Page 128: ...4 54 4222983 Second Edition ELECTRICAL 4 Page Intentionally Blank...
Page 241: ...ELECTRICAL 4222983 Second Edition 4 167 4 Page Intentionally Blank...
Page 242: ...4 168 4222983 Second Edition ELECTRICAL 4...
Page 266: ...5 24 4222983 Second Edition CHASSIS 5 Page Intentionally Blank...
Page 332: ...IX 14 4222983 First Edition INDEX IX...
Page 333: ......
Page 335: ......
Page 336: ......