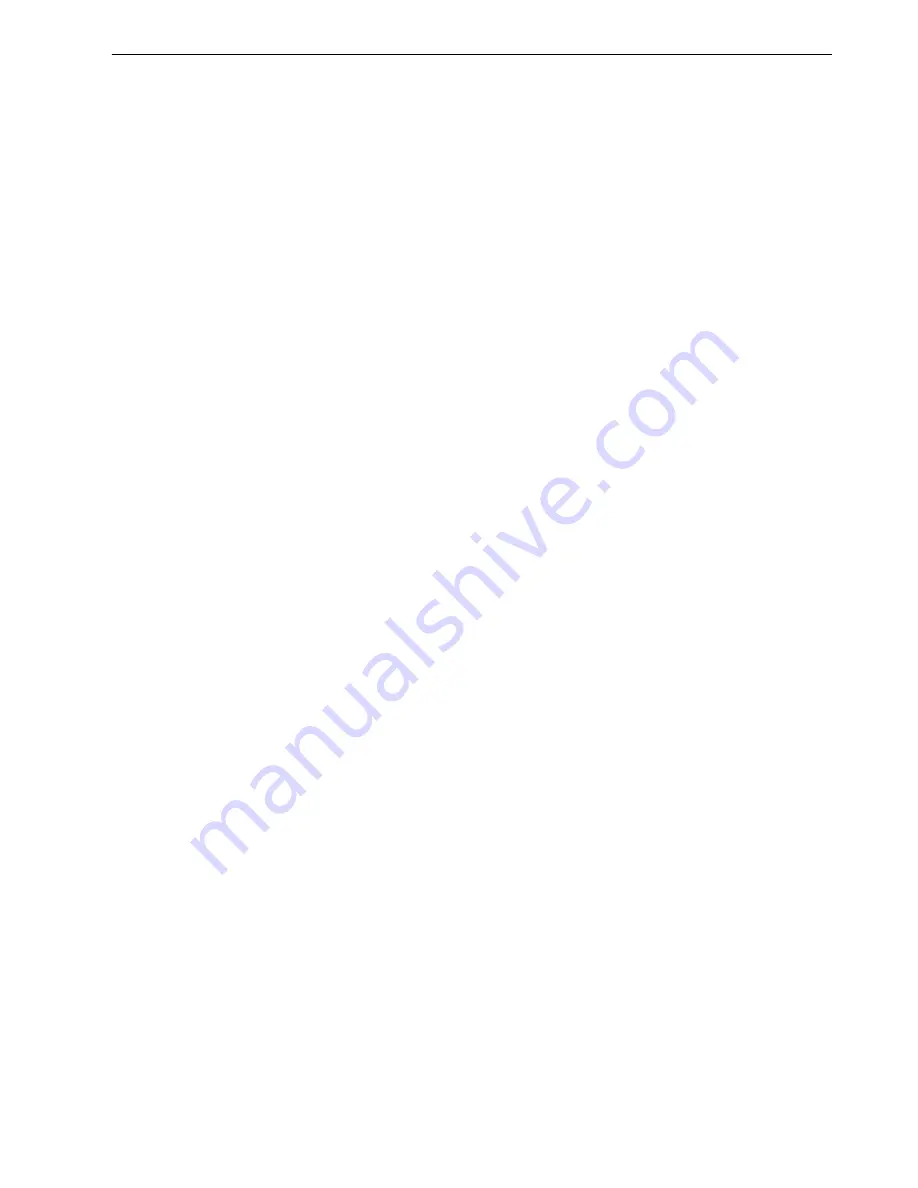
Electrical Maintenance
89
Phase Contactor 2 – PC2
Provides corrected 3 phase power to the system.
This is controlled by the Phase Select Module
(7EB). This is mechanically interlocked with PC1.
Compressor Motor Contactor – CC
This contactor provides the 3 phase power to the
motor overload relay. This is electrically
interlocked with GC through the Aux contacts.
Overload Relay – OL
This is the overload relay for the compressor
motor. There are three different settings
depending on motor size and voltage
configuration:
•
230 VAC 12HP, set OL to 34A
•
460 VAC 12HP, set OL to 20A
•
460 VAC 19HP, set OL to 32A
The OL provides an output to the controller when
the overload has tripped (EOL).
Heater Contactor – HC
Is only active when in electric stand-by and unit
requires heat. This contactor is not interlocked
with any other contactor.
Heater Overload Relay – OLH
Provides 3 phase to the Heater Contactor. This is
not interlocked with any other contactors.
Fuse Block 1 – FB1
Main fuses for 3 phase Power from Electric
Standby (Both 230V and 460V).
Fuse Block 2 – FB2
Fuses for output of transformer (Voltage @ 230
Vac in a 460 Vac system).
Auto Phase System
The Auto Phase system automatically adjusts the
phase sequence of the power supply to correspond
with the wiring of the electric motor. The main
components of the system are the phase selection
module (PSM), and the two phase contactors
(PC1 and PC1). Contactor PC1 is wired to retain
the phase sequence. Contactor PC2 is wired to
change the phase sequence. The PSM senses the
phase sequence at PC2 and energizes the
appropriate phase contactor.
Troubleshooting the Auto Phase System
If the electric motor runs backwards:
1. Turn the electric power supply Off and check
the unit wiring. See the appropriate wiring
diagrams, schematics, and Figure 156.
a. The three wires from the PSM should be
connected to the PC2 terminals as follows:
Brown wire to terminal T1, Gray wire to
terminal T2, and Black wire to terminal
T3.
b. Bus bar/wires L1-01, L2-01, and L3-01
should be connected respectively to
terminals T1, T2, and T3 on PC2, and L1,
L2, and L3 on PC1.
c. Bus bar/wires L1A-01, L2A-01, and
L3A-03 should be connected respectively
to terminals T1, T2, and T3 on PC1, and
L3, L2, and L1 PC2.
d. Bus bar/wires L1A-02, L2A-02, and
L3A-02 should be connected respectively
to terminals L3, L2, and L1 on PC2 and
L1, L2, and L3 on CC.
e. Bus bar/wires T1A-01, T2A-01, and
T3A-01 should be connected respectively
to terminals T1, T2, and T3 on CC and L1,
L2, and L3 on OL.
f.
Wires T3 & T9, T2 & T8, and T1 & T7 for
the 230 V motor (or T3, T2, and T1 for the
460 V motor) should be connected
respectively to terminals T1, T2, and T3
on OL.
g. Wires L1, L2, and L3 should be connected
respectively to terminals X, Y, and Z in the
power receptacle.