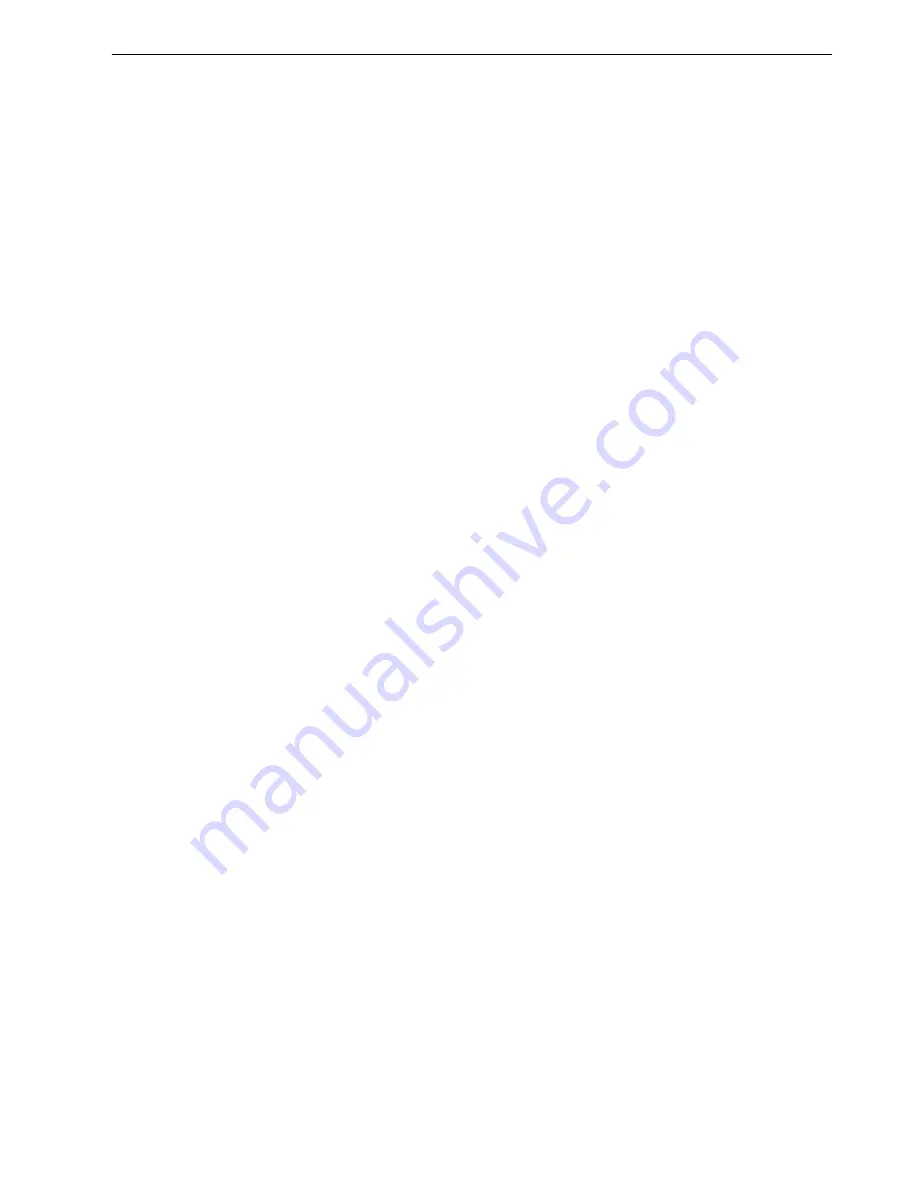
Refrigeration Service Operations
137
NOTE: When the compressor is removed
from the unit, the oil level should be noted,
or the oil removed from the compressor
should be measured so that the same amount
of oil can be added before placing the
replacement compressor in the unit.
Installation
1. Slide the compressor into the unit.
2. Place the compressor in position, install the
compressor belt on SmartPower units, and
install the mounting hardware.
NOTE: The compressor drive coupling or
clutch will only slide onto the coupling pins
in either of two positions, which are 180
degrees apart.
3. Install the service valves using new gaskets
soaked in compressor oil. Connect the high
pressure cutout switch, the pilot solenoid
valve line (if used), and install the compressor
oil filter.
4. Pressurize the compressor and test for
refrigerant leaks.
5. If no leaks are found, evacuate the
compressor.
6. Back seat the suction and discharge service
valves.
7. Tighten the compressor belt on SmartPower
units.
8. Operate the unit at least 30 minutes and then
inspect the oil level in the compressor. Add or
remove oil if necessary.
9. Check the refrigerant charge and add
refrigerant if needed.
Compressor Coupling Removal
(Standard Units)
1. After the compressor has been removed from
the unit, use the appropriate Allen tool
provided with removal tool P/N 204-991 to
loosen the center bolt which holds the
coupling to the compressor shaft.
2. Attach the tool to the coupling with the
provided socket head screws and spacers. Two
sets of spacers are provided with the tool, use
the short spacers with shallow compressor
mounting flanges and the longer set for deeper
flanges. The side with the countersunk holes
should be toward the coupling.
3. To prevent the tool and crankshaft from
rotating, use an appropriately sized bolt to pin
the tool to the flange. If a nut is used to
prevent the bolt from falling out, the nut
should not be tightened.
4. Use the appropriate Allen tool to loosen the
coupling mounting screw.
5. Once the center screw has been loosened,
back the head against the tool and it should
push the coupling off the crankshaft as you
continuing turning the center screw in a
counter-clockwise direction. Using this tool
will prevent the coupling from popping off
because the center bolt and flatwasher will
hold it in place.
Compressor Coupling Installation
(Standard Units)
In a tapered fit joint the entire twisting load
should be handled by the friction fit between the
two tapered parts. The key is only a backup and is
used to index the parts correctly. When a taper fit
is machined and assembled properly a key is not
needed. In fact, if the key is not installed correctly
it may be worse than no key at all! If the key does
not fit easily into the keyway, it will push the
tapered components apart and the reduced friction
could lead to slippage and premature failure.
The following procedure requires the key to be
fitted after the tapers are pulled together with
20 ft-lb (27 N•m) torque. This insures that the key
cannot hold the tapers apart when the final bolt
torque is applied.
Use the following procedure to install a
compressor coupling on the compressor
crankshaft.
1. Clean the compressor shaft taper and coupling
bore taper with a solvent that leaves no oily
residue (such as naphtha, lacquer thinner,
brake cleaner or the like).