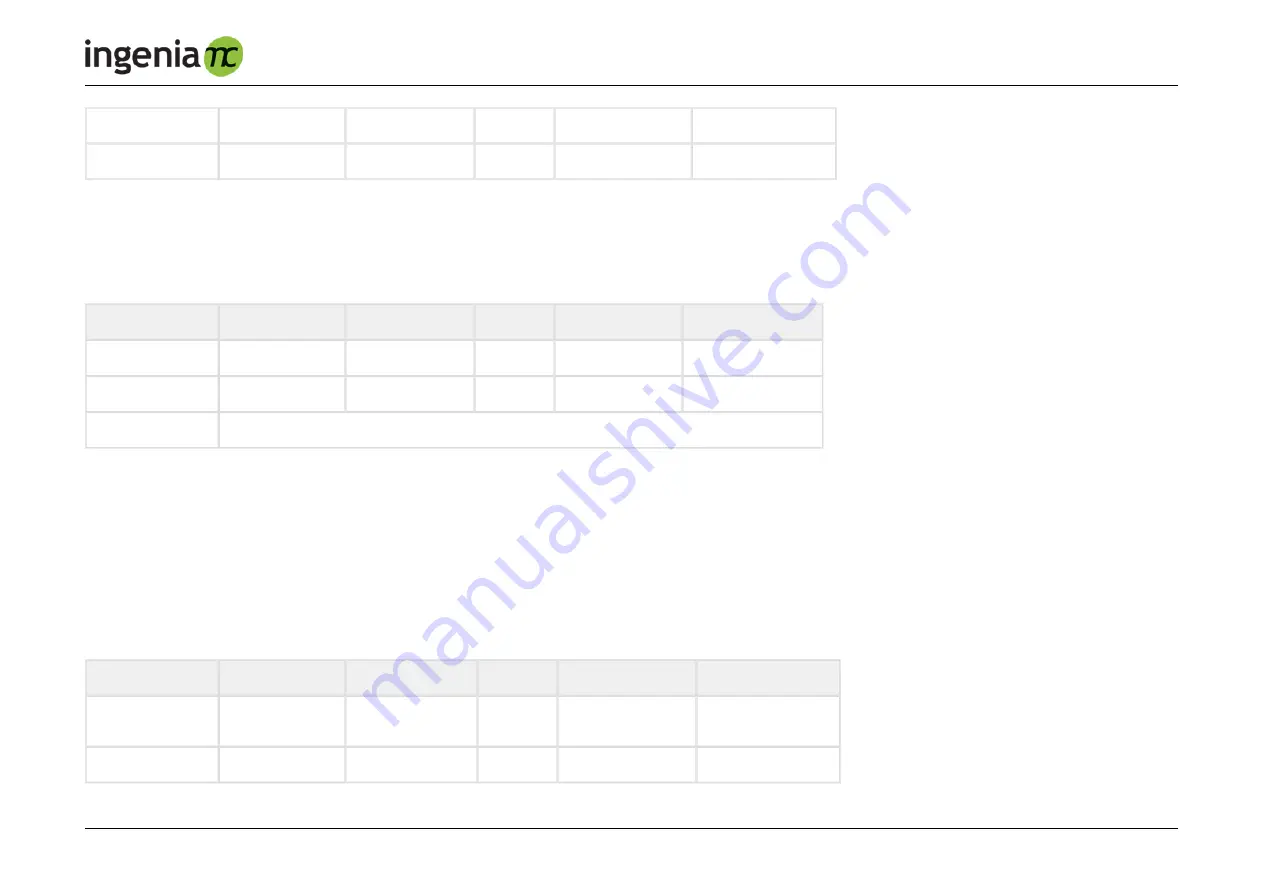
Installation Guide
INGENIA MOTION CONTROL
Confidential and proprietary information.
Unauthorized Copies Prohibited.
Page
of
89
307
Connector
TE Connectivity
Suggested cable
3M
For crimped cable
Some applications require single cables with crimp terminals. This makes the wiring cleaner and is a preferred option for volume applications. Jupiter connectors
include locking latches that provide audible click during mating and ensure assembly robustness.
Manufacturer
Manufacturer ID
Farnell
Digikey
Mouser
Connector
TE Connectivity
-
Crimp terminals
TE Connectivity
Suggested cable
Use 0.2 ~ 0.5 mm² (20 ~24 AWG).
<< Back to top
7.3.4 I/O mating connectors
For ribbon cable
The easiest and lowest cost option is using a 16 way flat ribbon cable with 1.27 mm pitch. Please see
.
Manufacturer
Manufacturer ID
Farnell
Digikey
Mouser
Connector
TE Connectivity
Suggested cable
3M