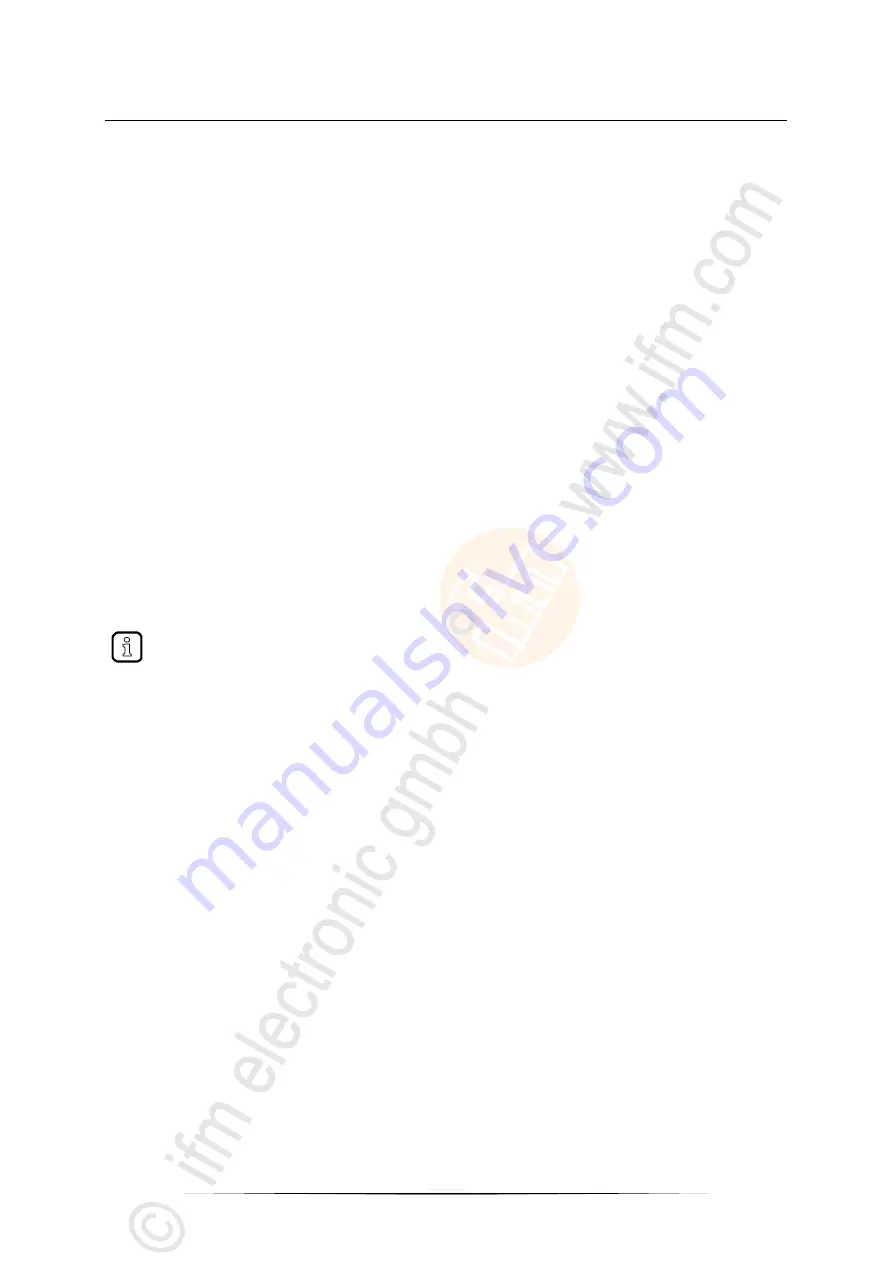
66
ifm
Programming Manual ecomatController/60-1 (CR711S) Operating System V2.5.0.n
2017-12-19
System configuration
Configure PLC
>
7.1.3
Manage files
23520
To transfer files between PC and device:
1 Select file view
► In the device tree: Double-click on symbol [Device (CR711S)]
► In the editor window: Select the [Files] tab.
>
The editor window shows the file structure on the PC on the left and on the device on the right
2 Transfer file from PC to device
► Highlight the file on the left
► Select device target directory on the right
► Star transfer using the [>>] button
>
The file is transferred to the device
3 Transfer the file from the device to the PC
► Highlight the file on the right
► Select PC target directory on the left
► Start the transfer using the [<<] button
>
The fle is transferred to the PC
>
7.1.4
Manage users and groups
23521
This function has not yet been implemented.