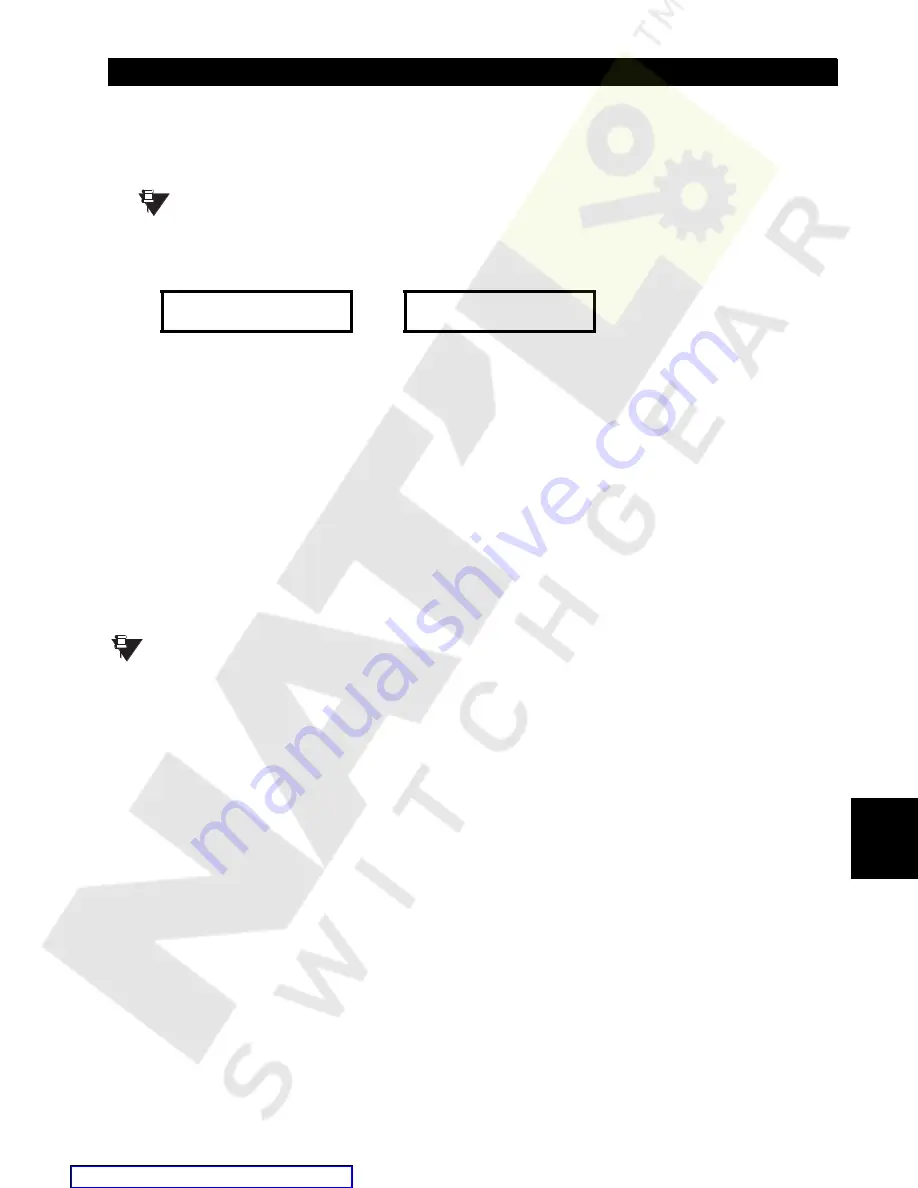
GE Multilin
745 Transformer Management Relay
8-31
8 COMMISSIONING
8.5 PROTECTION SCHEMES
8
2.
Slowly decrease the frequency until the output relay(s) operate. Check that the frequency at which operation took
place is the selected frequency setting.
3.
Slowly reduce the current. Note the current at which the output relay(s) reset. Check that this dropout current is the
minimum operating current selected in the settings.
If current sensing is not enabled, then the element will continue working all the way down to a current
level of 0.02
×
CT A.
4.
Increase the current back to nominal. Verify that the relay(s) operate.
5.
Check that the Trip and Pickup LEDs are on and one of the following trip messages is displayed:
6.
Slowly increase the frequency until the Pickup LED and output relays reset. Note the dropout level, which should be
the pickup plus 0.03 Hz. Check that the Trip LED is still on. The trip message remains on if the
UNDERFREQUENCY 1
TARGET
setting is "Latched"; if set to "Self-Resetting", the message resets when frequency is above the setpoint.
7.
For timing tests, the signal generator must be capable of triggering into step-wise changing of frequency or ramping
down to a pre-selected frequency in only a few milliseconds. Connect the Signal Source and Timer Start triggers as
shown in Figure 8–12: Frequency Element Testing on page 8–29.
8.
Set the current to rated CT secondary value, no voltage connection, and the pre-trigger frequency to the nominal fre-
quency (60 or 50 Hz).
9.
Set the post-trigger to 0.5 Hz below the Underfrequency 1 setting. If necessary, reset all targets and relays. Reset the
timer.
10. Initiate the frequency step and timer start. The Interval Timer will record the operating time of element. Compare this
time to the
S4 ELEMENTS
ÖØ
FREQUENCY
Ö
UNDERFREQUENCY 1
ÖØ
UNDERFREQUENCY 1 DELAY
setting.
11. Provided that the operate times are not scattered over a wide range, it may be desirable to repeat this test several
times and average the results. If there is a wide scatter, verify the test setup and ensure the signal source behaves in a
consistent manner.
The blocking from logic input, if enabled, can be tested as described in earlier tests for other elements.
c) UNDERFREQUENCY 2
1.
Disable all protection functions except the Underfrequency 2 function.
2.
Verify that settings match in-service requirements. Enter/modify settings and logic in the
S4 ELEMENTS
ÖØ
FREQUENCY
ÖØ
UNDERFREQUENCY 2
setpoints menu.
3.
Repeat the appropriate steps of Underfrequency 1 on page 8–29 for this element. The results must be compared to the
settings for the Underfrequency 2 element.
d) OVERFREQUENCY
Disable all protection functions except Overfrequency. Verify that settings match in-service requirements. Overfrequency
settings are modified in the
S4 ELEMENTS
ÖØ
FREQUENCY
ÖØ
OVERFREQUENCY
settings menu.
VOLTAGE INPUT FUNCTION (VOLTAGE INPUT ENABLED):
1.
Using the variable-frequency voltage/current source connected to terminals C11 and C12 for the voltage signal and H1
and G1 for the current signal, set the frequency to 60.00 Hz (or 50.00 Hz) and the voltage amplitude to the rated VT
secondary voltage. Set the current amplitude to rated CT secondary. Monitor the appropriate trip and auxiliary relays.
Reset all alarms and indications on the relay. The 745 display should remain unchanged with no trip indications.
2.
Slowly increase the frequency until the output relay(s) operate. Check that the frequency at which operation took place
is the selected frequency setting. As the frequency is varied, verify that the
A2 METERING
ÖØ
FREQUENCY
Ö
SYSTEM
FREQUENCY
actual value indicates the correct value of system frequency.
LATCHED
Underfrequency 1
OPERATED
Underfrequency 1
NOTE
NOTE