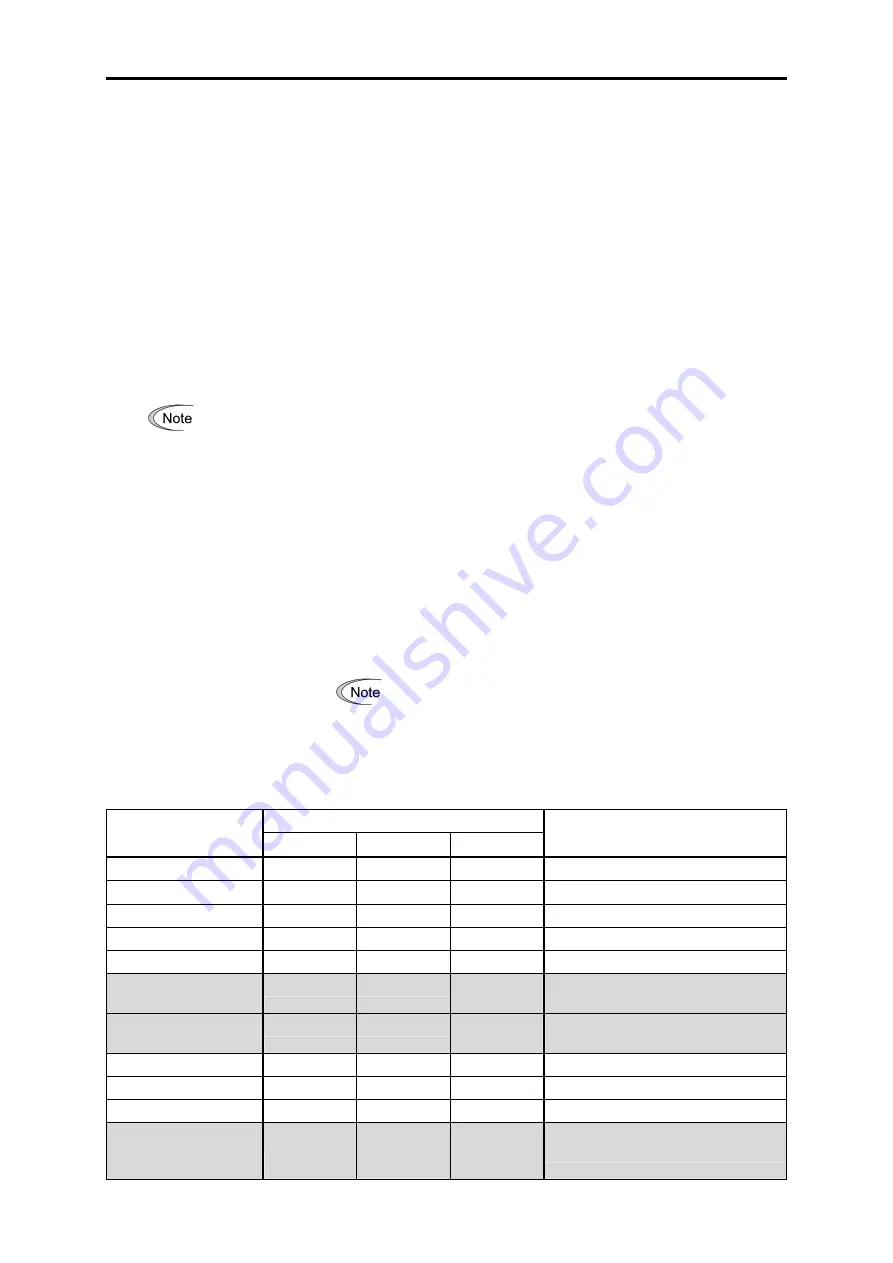
6-148
2) For installations into facilities which restart after instantaneous power failures, use the running restart
function which searches the direction and speed of free running rotation and picks up smoothly to
reengage drive or use [IL] of the X terminal.
3) For simple systems, hardware can be constructed as Figure 6.6.7. However, when a more complex
process sequence is desired, construction of a system structure which operates on communication with
PLC is recommended.
4) Configuring motor parameters
Direct parallel connection method is a control method where a single winding motor is operated in
parallel by plural inverters. Therefore, the motor constant required for inverter to control the motor is
"1/number of connected inverter units".
When an operation with reduced number of inverters, a characteristic of the direct parallel connection
system, is performed, the motor constants need to be changed. In this inverter, the motor constants can
be used by switching in the selection of motor constant switching function of X terminal by presetting
the constant codes of vector with speed sensor and sensorless vector for up to three motors.
At present, motor can be operated only by direct parallel connection with two or three inverters
or by the operation reduced to one inverter
Table 6.6.20 shows a setting method of motor parameters including the time of the operation with
reduced number of inverters.
When performing the operation with reduced number of inverters in the direct parallel connection system,
set the motor constants after determining the definitions of motor constant codes.
In the case of direct parallel connection of 2 units, use M2 codes as
reference motor constants.
In the case of direct parallel connection of 3 units, use M3 codes as
reference motor constants.
<Definitions>
• M1: Maximum number of
connected units
• M2: Maximum number of
connected units-1 unit
• M3: Maximum number of
connected units-2 units
The reference motor constants denote a state of connection in
which the ratio of motor (one-coil motor) to inverter becomes
1:1.
Table 6.6.20 Explanation of Change of Motor Constants in the Operation
with Reduced Number of Inverters
Parameter code
Parameter name
M1 code
M2 code
M3 code
Coefficient of setting value in operation
with reduced number of inverters
Drive control
P01
A01
A101
Motor selection
P02
A02
A102
Maximum speed
F03
A06
A106
Rated speed
F04
A03
A103
Rated voltage
F05
A04
A104
Rated capacity
P03
A05
A105
x (1/No. of units participating in direct
parallel connection)
Rated current
P04
A06
A106
x (1/No. of units participating in direct
parallel connection)
Number of poles
P05
A07
A107
%R1 P06
A08
A108
%X P07
A09
A109
Exciting current/
magnetic Flux weakening
current (-Id)
P08
A10
A110
x (1/No. of units participating in direct
parallel connection)
Summary of Contents for FRENIC-VG Series
Page 1: ...For the STACK type User s Manual User s Manual Option Edition 24A7 E 0045 3 ...
Page 2: ......
Page 3: ...High Performance Vector Control Inverter User s Manual Option Edition ...
Page 155: ...6 5 SX Bus Interface Card 6 79 Chap 6 CONTROL OPTIONS Figure 6 5 5 ...
Page 156: ...6 80 Basic Connection Diagram Figure 6 5 6 ...
Page 344: ......
Page 346: ...For the STACK type User s Manual User s Manual Option Edition 24A7 E 0045 3 ...