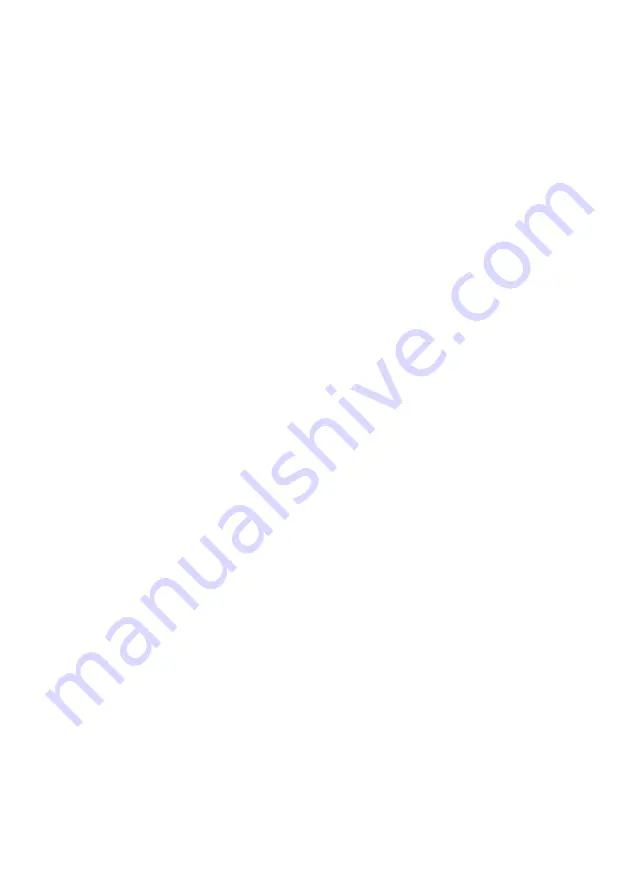
Festo — MSE6-C2M — 2022-08b
Functions
27
The timer has not yet exceeded the auto-controller delay time parameter value, Pm.17-18.
–
2 = UP: the Timer has expired.
The timer has overshot the auto-controller delay time parameter value, Pm.17-18.
The Q_low-Timer is reset in the following cases:
–
in the AUTO_WAIT module status, Em.3.8-11 = 9, and
in the AUTO_HOLD module status, Em.3.8-11 = 10, if the auto-controller flow rate limit value is
overshot, Pm.19-20.
–
by a reset control signal, 1 = active. The signal can be selected with the Q_low-Timer-Reset
selection parameter, Pm.28.0-28.1:
–
output Q_low-Timer-Reset, Am.0.2
–
electrical input DI0
–
electrical input DI1
–
logic operation: electrical input DI0 OR output Q_low-Timer-Reset, Am.0.2
Module status
The module status results from the status or status of sub-functions of the pressure regulation and
blocking function and is displayed in input, Em.3.8-3.11.
The individual module states are described in the Function states chapter.
Shut-off valve
Depending on the setting of auto user output control, Am.0.1, the shut-off valve is controlled either by
the user or by the shut-off valve auto-controller partial function.
The switching status of the shut-off valve is determined by the input Status shut-off valve input status,
Em.3.0.
The number of shut-off valve switching cycle is returned in different types and data formats:
–
16-bit or 32-bit input value via selectable inputs Em.5 and/or Em.6
–
16 bit parameter value, Pm.31-32
Pressure regulator
Depending on the setting of auto user output control, Am.0.1, the setpoint pressure for the pressure
regulator is determined as follows:
–
by the target pressure value set by the user
–
by the setpoint pressure value specified by the auto setpoint pressure sub-function.
Before forwarding to the pressure regulator, the setpoint value is limited to values between
2.5 … 10.0 bar within the module. The rise is limited to the set parameter value when the target
pressure is increased.
Monitoring of parameters
The unit pressure, Pm.8.0-8.1, flow rate unit, Pm.8.2-8.3, standard flow rate, Pm.8.6-8.7, auto-con-
troller flow rate limit value, Pm.19-20, re checked for permissible on input. In case of error, the
appropriate error message is generated if parameterisation error monitoring is activated, Pm.0.7.
Actuator supply monitoring
This function is used to monitor the actuator supply for undervoltage. In case of error, the corre-
sponding error message is generated with activated monitoring, Pm.0.2.