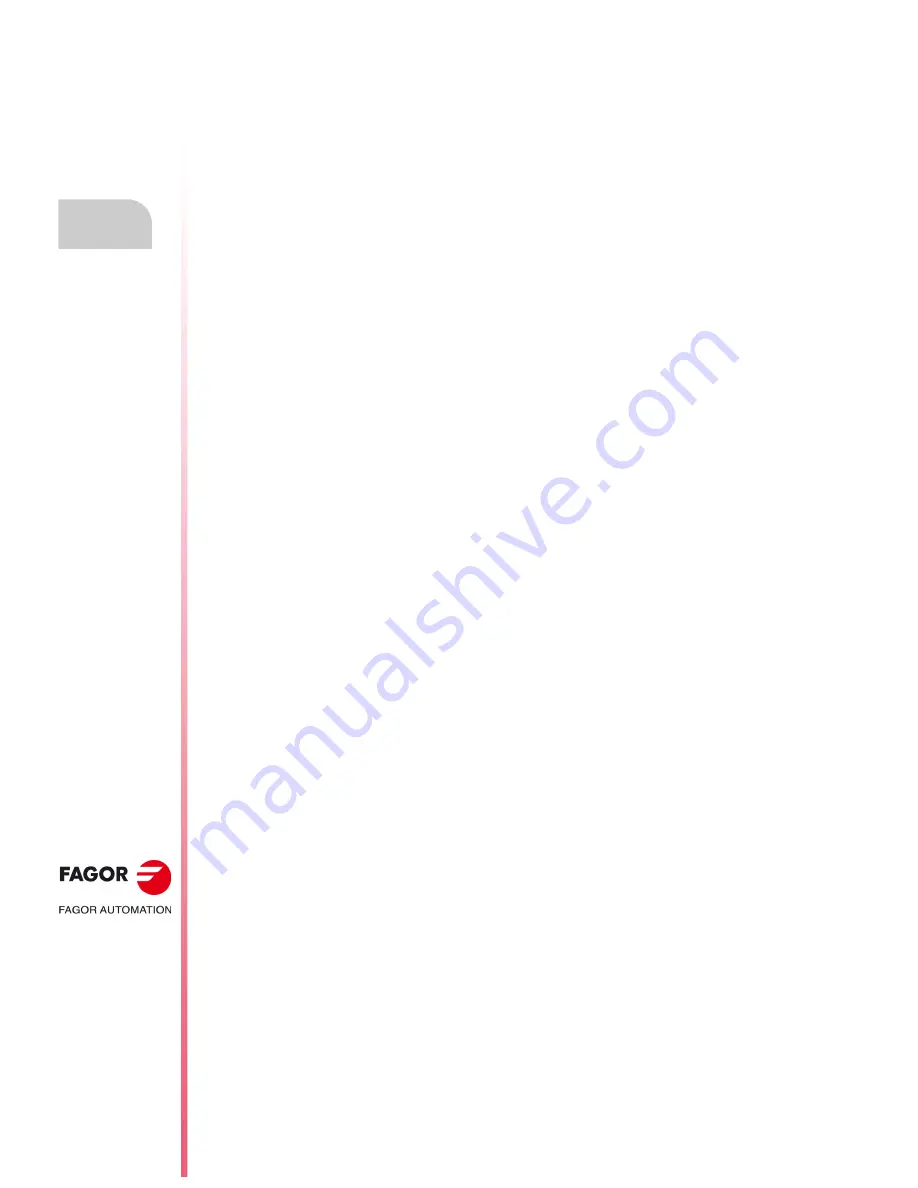
·234·
Operating manual
CNC 8055
CNC 8055i
13.
DIAGNOSIS
·T· M
ODEL
S
OFT
: V02.2
X
Adjustments
Drive parameters that may be modified.
Axis parameters. Indicate the axis, the name of the parameter and the set separated by a period.
Example:
X.CP1.0
Y.CP20.2
Z.SP1.1
Save and load the configurations of the oscilloscope
The system permits saving the current configuration into a file in ASCII format. To do that, set general
machine parameter STPFILE with the number to be assigned to the configuration file (the number
must be other than 0). The configuration file may be treated like any other program, sent out via DNC
or even edited.
When saving or loading a configuration, the CNC first checks if the file already exists in User RAM
and if not, it will look for it in the hard disk (KeyCF).
Several configurations may be saved in the configuration file. Each configuration must be assigned
a name of up to 40 characters.
The following softkeys are related to this feature.
Save
To save the current configuration, press the [Save] softkey and enter the name
to save it with up to 40 characters. If there is a previously saved configuration with
the same name, it will ask whether it must be replaced or not.
Load
To load a previously saved configuration, press the [Load] softkey and select it
from the list on the screen. If the configuration makes not sense (for example,
because the CNC does not have an axis that that configuration refers to), the CNC
will warn the user and it will only load the portion of the configuration read until
that error came up.
Delete
To delete one of the saved configurations, press the [Delete] softkey, select it from
the list on the screen and press [ENTER].
Reset
Pressing the [Reset] softkey resets the current configuration. There are neither
variables nor parameters selected and the rest of conditions (colors, trigger, etc.)
assume the values assigned by default.
Access to PLC resources
From the configuration screen, the system can access the PLC resources. The following syntax must
be used to access them:
• Marks: PLC.M1234
• Inputs: PLC.I25
• Outputs: PLC.O1
• Registers: PLC.R560
• Register Bit: PLC.B0R560
• Timers: PLC.T1
• Counters: PLC.C1
Access is also possible using the associated symbol.
Example: PLC.ENABLEX
An error will be issued when accessing a non-existent PLC resource.
Summary of Contents for CNC 8055
Page 1: ...CNC 8055 T Operating manual Ref 1705 Soft V02 2x...
Page 6: ...6 Operating manual CNC 8055 CNC 8055i T MODEL SOFT V02 2X...
Page 10: ...18 CNC 8055 CNC 8055i Declaration of conformity and Warranty conditions...
Page 14: ...10 CNC 8055 CNC 8055i Version history...
Page 20: ...16 CNC 8055 CNC 8055i Returning conditions...
Page 22: ...20 CNC 8055 CNC 8055i Additional notes...
Page 24: ...22 CNC 8055 CNC 8055i Fagor documentation...
Page 124: ...124 Operating manual CNC 8055 CNC 8055i 6 MANUAL T MODEL SOFT V02 2X Spindle movement...
Page 134: ...134 Operating manual CNC 8055 CNC 8055i 7 TABLES T MODEL SOFT V02 2X Tool Offset table...
Page 135: ...Operating manual CNC 8055 CNC 8055i TABLES 7 T MODEL SOFT V02 2X 135 Tool Offset table...
Page 138: ...138 Operating manual CNC 8055 CNC 8055i 7 TABLES T MODEL SOFT V02 2X Tool geometry table...
Page 196: ...196 Operating manual CNC 8055 CNC 8055i 10 PLC T MODEL SOFT V02 2X Logic analyzer...
Page 212: ...212 Operating manual CNC 8055 CNC 8055i 11 GRAPHIC EDITOR T MODEL SOFT V02 2X Modifications...
Page 240: ...240 Operating manual CNC 8055 CNC 8055i 13 DIAGNOSIS T MODEL SOFT V02 2X Interesting notes...
Page 253: ...Operating manual CNC 8055 CNC 8055i 14 T MODEL SOFT V02 2X 253...
Page 254: ...254 Operating manual CNC 8055 CNC 8055i 14 T MODEL SOFT V02 2X...
Page 255: ......